

Bühler Group
https://www.buhlergroup.com/content/buhlergroup/global/en/homepage.html?cid=Webpage_Apf_HN-mini-site-CAM
Bühler Group
About the company
Who are we?
We are a Swiss family company with more than 150 years in the market, present in more than 140 countries, 30 manufacturing sites, and 100 service stations. Allowing us to be a leader in the supply of technologies and solutions for the transformation of grain into flour and food, as well as in the production of pasta and chocolate. We also provide the solution to produce feed, petfood and aquafeed. Our portfolio also includes die-casting, wet milling, and surface coating processes.
Bühler began operations in Mexico in 1959, and currently has headquarters and a service station in the city of Toluca, from which it serves the region of Mexico, Central America, and Cuba, with the sale of equipment and spare parts, engineering, automation, technological consulting, roll reconditioning among others.
How can we support the pet food, fish, and shrimp food industry?
Bühler is capable of supplying the complete solution for feed, petfood and aquafeed, based on the following pillars: food safety, efficiency, and sustainability. Therefore, we can provide from plant design, pre-engineering, installation, to automation services, plant assessments and training, all based on personalized attention from sales, technology, and customer service, seeking to develop our customer´s success with long-term relationships.
Our process solutions range from the grain receiving, cleaning and handling systems, storage, ingredient dosing, mixing, fine and wide grinding, extrusion (single or double shaft extruders), pelleting, drying, coating, and cooling. Enabling the production of wide range of products: sizes, colors, textures, and ingredients.
We invite you to learn about the success stories of our customers around the world, our solutions and, above all, to schedule an appointment with our industry specialists, who look forward to serving you.
Products
Company News
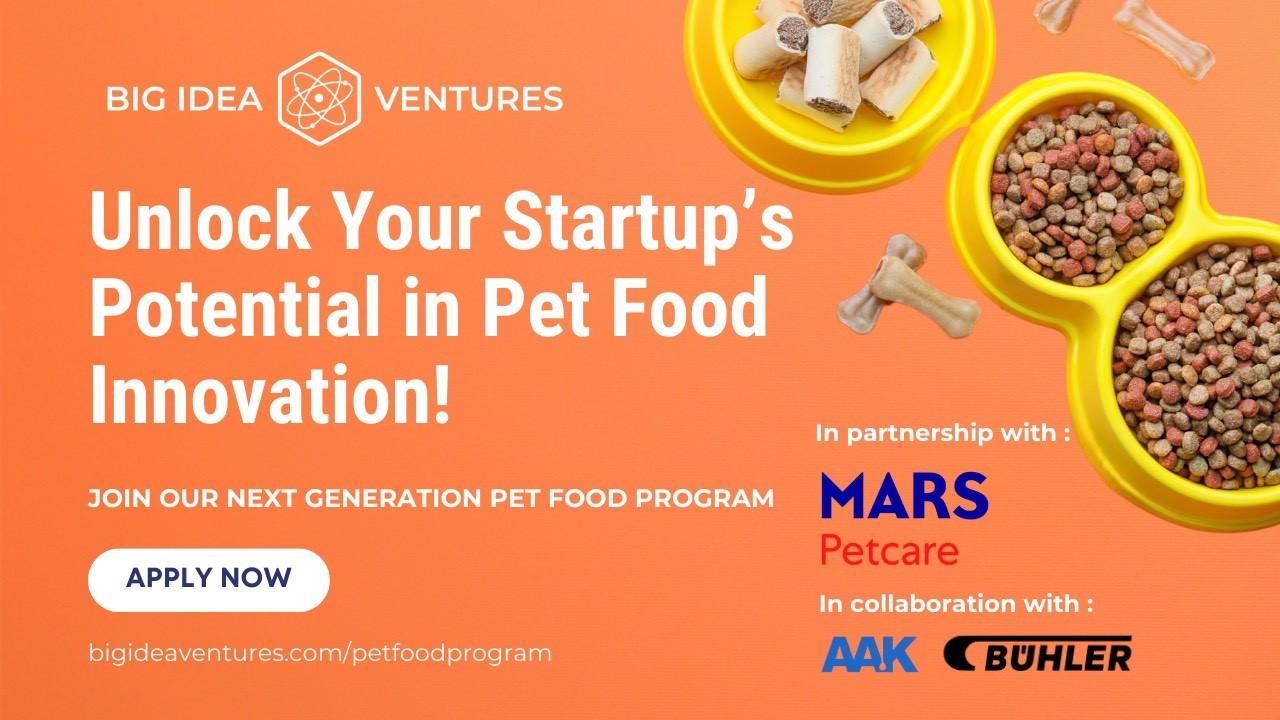
2+ MIN
03/09/2024
Exciting News: Big Idea Ventures, in partnership with Mars Petcare and Bühler Group, is launching the Next Generation Pet Food Program
The program is open to any food start-ups developing sustainable proteins and fats, novel ingredients with top-notch nutritional profiles, or pioneering processing technologies like upcycling food waste. It will run online in October and November, with participants joining us in Singapore during the International AgriFood Week on November 18, 2024. A message from Mars Petcare For our 100,000 Petcare Associates, Our Purpose: A BETTER WORLD FOR PETS also means a more sustainable world for pets, people and for the planet. We are constantly focusing on finding new ways to help pets and their owners live happy, healthy lives together. We are committed to investing in innovation to help us source the best ingredients to support healthy pets while reducing our environmental footprint. We are working on a number of research and development projects to identify new and innovative ingredients that reduce our environmental footprint and are nutritious for pets, focused on innovations in: Wet Animal Protein Solutions: Seeking innovative, sustainable sources of wet animal protein. Oil & Fat Solutions: Developing substitutes for traditional chicken fat and pork fat. Fiber Reduction from Protein-Rich Sources: Working on projects to reduce fiber content from protein-rich sources. Why It Matters We believe that our Purpose: A BETTER WORLD FOR PETS, also means a more sustainable world for pets, people and for the planet. We seek to support innovative businesses and actively foster collaboration opportunities in the pet care space, with the aim of contributing to a more dynamic and progressive industry that addresses the evolving needs of pets and their owners. To help us source the best ingredients to support healthy pets while reducing our environmental footprint, we are partnering with companies that focus on developing new and novel ingredients which are safe, lower carbon, available, nutrient dense, and delicious – while ensuring animal welfare, safety and quality are at the forefront. How you can join them? In collaboration with Mars Petcare, and with the support of AAK and Bühler, we have crafted a unique program tailored for human food startups eager to innovate in the sustainable pet food space. This program offers the chance to gain direct insights and support from pet food experts as you develop your initial pet food concept. Once your concept and pitch are polished with the BIV team, you'll have the exciting opportunity to travel to Singapore and present your innovation to a prestigious audience! For more information, visit us HERE Source: Big Idea Ventures
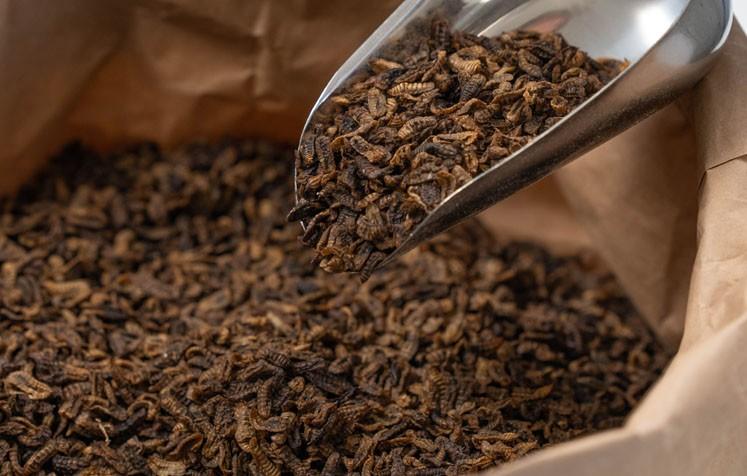
3+ MIN
06/12/2023
Agroloop commissions Bühler to provide proven insect-rearing tech for animal feed
Swiss company Bühler will deliver its proven crate-based nursery and rearing technology, enabling a quick ramp-up of the plant for commercial production. By the end of 2024, Agroloop plans to launch its first products, contributing to a more sustainable animal feed value chain. Industrial-scale insect plant Following its foundation in 2017 and the operation of a pilot facility, Agroloop got the green light to implement an industrial insect plant in Hungary in 2022. Now, they have selected all execution partners and are working at full speed to construct the plant and get it operational. In the new plant, Agroloop will produce more than 25,000 metric tons of black soldier fly larvae that will be turned into sustainable feed ingredients for the pet food, aquaculture and livestock sectors. The plant is only the first step in Agroloop's strategy to make insect feed ingredients available for the Central and Eastern European (CEE) agribusiness. 'The abundance of food processing by-products presents a unique opportunity for Agroloop's multi-plant rollout strategy in the CEE region, ' says István Nagy, co-founder and CEO of Agroloop. 'We leverage our strategic partnership with the leading regional feed producer UBM Group to improve feed quality and sustainability by creating future-proof feed formulas. This enables Agroloop to focus on rapid expansion and solidifies our position as a key player in the region.' Tech for short ramp-up time Agroloop's insect growth technology has a big influence on plant yield, directly impacting the performance of business. Agroloop has chosen Bühler's nursery and rearing technology for their insect growth system, which has several years of track record in the insect industry. 'We've assembled a technology supplier portfolio to build our plant. Bühler is crucial in providing this design's framework and core components. By choosing Bühler's technology, Agroloop can enter the value chain with the highest standards,' says István Nagy. Sustainable protein in demand In pursuing sustainable and environmentally friendly practices, the CEE region increasingly turns to alternative sources for feed ingredients. By incorporating insects into the feed supply chain, the region can address environmental concerns, reduce dependence on imported protein sources, and contribute to a circular economy approach. In addition, innovative feed formulations containing insects can optimize animal health and growth, thus leading to more efficient livestock production systems. Insects can be reared on agricultural and food processing by-products, transforming these materials into high-quality protein. This approach reduces the environmental impact of this value chain and creates a closed-loop system where resources are reused and recycled. The EU has previously depended on imported protein sources for animal feed, contributing to deforestation and habitat destruction in other parts of the world. By embracing the commercialization of insect-based livestock feed, the region can increase feed efficiency, reduce reliance on external sources, and contribute to local and regional food security. Andreas Baumann, head of market segment insect technology at Bühler, adds: 'The incorporation of insect ingredients in animal feed presents a compelling solution to the challenges faced by the livestock industry.' 'Besides providing nutritious and sustainable protein sources, insects empower local economies to become self-sufficient. That is why insect protein is key to a more sustainable and resilient food system.' Yesterday, Food Ingredients First reported that the UK Edible Insect Association said that European Novel Food regulations impose an 'extremely high barrier to entry for edible insect companies and ignore the sector's potential to build a more sustainable food system.' In other insect-based developments, US-based scientists recently revealed they are targeting dairy waste reduction by mass-producing the black soldier fly that feeds on it and evaluating the insect's potential as a feed for livestock and domestic pets. ' by Bühler
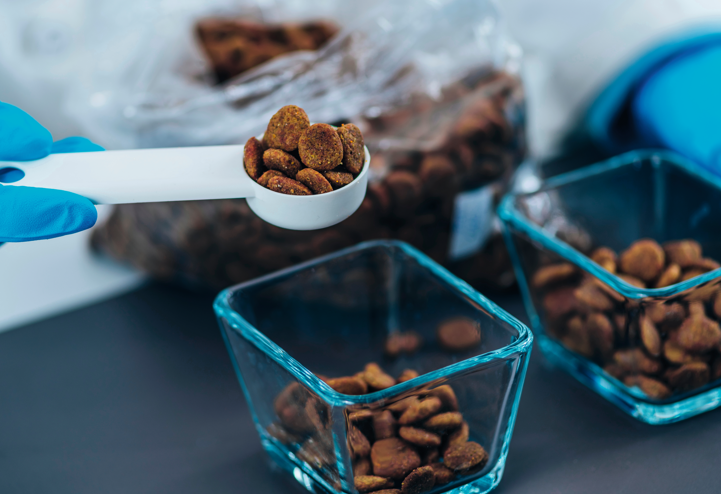
3+ MIN
22/09/2023
Deadly mycotoxins in pet food cost pet health and brand trust, Bühler has an answer
Product recall is expensive One of the major costs of mycotoxin contamination is market recall. Recalling a product from the market is not cheap, in fact, the Grocery Manufacturers Association (GMA) discovered that the average cost of the market recall is USD10 million in direct costs alone. The financial hits of product recall include: disposing of the product, reimbursing customers, and business interruption. The GMA survey showed that 81% of respondents deemed the financial risk of market recall to be 'significant to catastrophic.' Contaminated product damages brand image Financial costs and damage to health are not the only repercussions of mycotoxin contamination. Once the media are aware of the situation, brand image can take a significant hit. For consumers, it takes a lot to repair trust in a brand, and while brand damage is difficult to measure, this can further cost companies millions in lifetime value. Contaminated product can cause mass waste Before the LumoVision, contaminated grain would have been disposed of in large amounts. During testing, if the batch has a high concentration of mycotoxin, in many cases, the entire batch is destroyed. In fact, as few as 2 highly contaminated grains in 10,000 can render an entire batch unsafe. The Food and Drug Association (FDA) estimates that USD932 million is lost per year to crops contaminated with mycotoxin. This removal of the contaminated material may protect the consumer, but it costs businesses and the environment a lot more. What can be done? Bühler SORTEX faced the challenge of mycotoxin contamination head-on. After discovering a breakthrough 'invisible indicator' of contamination on the spectral scale, Bühler created the LumoVision, an optical sorter that can reduce the aflatoxin level by up to 90% (as indicated by industrial trials). This reduction brings many samples to regulation levels, saving companies from the costs of large-scale material waste and market recall. It works by analyzing the color each kernel fluoresces as it passes under powerful UV lighting in the sorter. It is known that contaminated kernels fluoresce a specific bright green color, a substance called kojic acid, which is produced by the Aspergillus fungus at the same time as it produces aflatoxin. LumoVision's proprietary, highly sensitive cameras and a powerful LED-based UV lighting system can precisely detect this color of fluorescence. Within milliseconds of detection, air nozzles deploy to blow contaminated kernels out of the product stream. When dealing with toxins, early intervention is critical. This is not only important in reducing the toxins consumed by pets, but also to lower wastage and the environmental footprint. Without proper cleaning and sorting, poisonous mycotoxins can cause large-scale wastage of materials, mass market recalls, and harm to pets. Dr. Gerardo Morantes, Director of Food Safety-Americas Region at Buhler, had the following to say: 'Mycotoxins are a worldwide concern. However, technology made possible by Bühler SORTEX enables a preventative solution, meaning that mycotoxins can be dealt with early, stopping the spread and removing the contamination to meet regulatory standards.' Without intervention, mycotoxin contamination can bare a large cost for businesses, including, brand reputation, market recalls and material waste. With the SORTEX LumoVision, brands can stay profitable, customers can stay happy and pets can stay safe. For more information on how Bühler and LumoVision are kicking out mycotoxins, visit their webpage. Source: All Pet Food Magazine
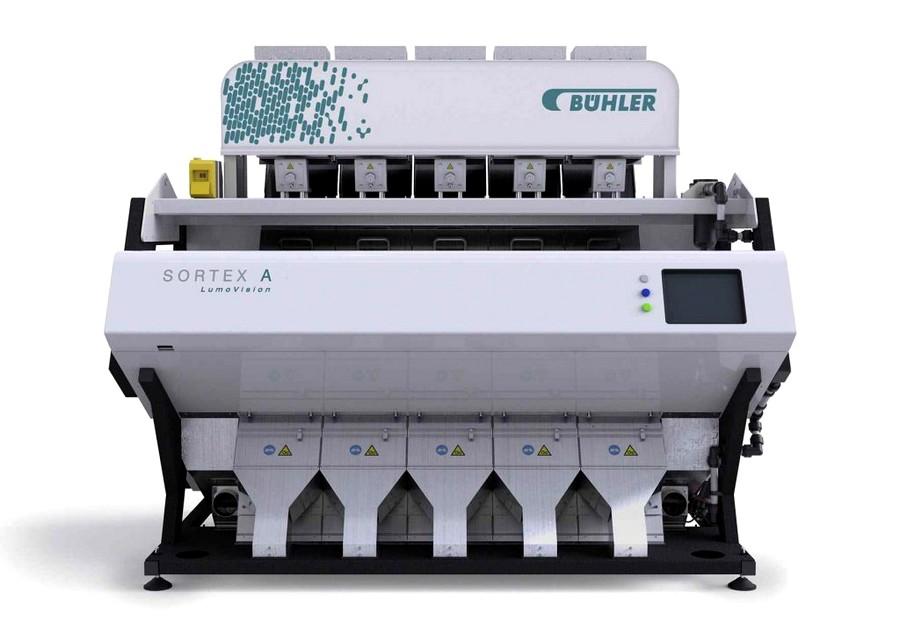
3+ MIN
17/08/2023
Bühler offers solution to reduce mycotoxin levels in pet food
Mycotoxins, a poisonous chemical found in the corn used in pet foods, are causing animal sickness and irreparable brand damage. To solve this issue, SORTEX LumoVision, a solution developed by Swiss technology group Bühler, uses the spectral scale to kick out mold from pet food, keeping the costs of market recall down and pets safe. In 2021, the FDA (Food and Drug Administration) alerted customers of fatal levels of aflatoxin, a strand of mycotoxin that attacks the liver, found in 1,000 lots of pet food. From the bad batch, it is reported that 130 dogs died. This statistic provoked lawsuits and anger from dog owners and the wider industry. However, the damage of mycotoxin contamination does not stop there. RECALLING PRODUCT IS EXPENSIVE One of the major costs of mycotoxin contamination is market recall. Recalling a product from the market is not cheap, in fact, the Grocery Manufacturers Association (GMA) discovered that the average cost of market recall is USD10 million in direct costs alone. The financial hits of recalling product include: disposing of the product, reimbursing customers, and business interruption. The GMA survey showed that 81% of respondents deemed the financial risk of market recall to be 'significant to catastrophic'. CONTAMINATED PRODUCT DAMAGES BRAND IMAGE Financial costs and damage to health are not the only repercussions of mycotoxin contamination. Once the media are aware of the situation, brand image can take a significant hit. For consumers, it takes a lot to repair trust in a brand, and while brand damage is difficult to measure, this can further cost companies millions in lifetime value. CONTAMINATED PRODUCT CAN CAUSE MASS WASTE Before the LumoVision, contaminated grain would have been disposed of in large amounts. During testing, if the batch has a high concentration of mycotoxin, in many cases, the entire batch is destroyed. In fact, as few as 2 highly contaminated grains in 10,000 can render an entire batch unsafe. The Food and Drug Association (FDA) estimate that USD932 million is lost per year to crops contaminated with mycotoxin. This removal of the contaminated material may protect the consumer, but it costs businesses and the environment a lot more. WHAT CAN BE DONE? Bühler SORTEX faced the challenge of mycotoxin contamination head-on. After discovering a breakthrough 'invisible indicator' of contamination on the spectral scale, Bühler created the LumoVision, an optical sorter that can reduce the aflatoxin level by up to 90% (as indicated by industrial trials). This reduction brings many samples to regulation levels, saving companies from the costs of large-scale material waste and market recall. It works by analysing the colour each kernel fluoresces as it passes under powerful UV lighting in the sorter. It is known that contaminated kernels fluoresce a specific bright green colour, a substance called kojic acid, which is produced by the Aspergillus fungus at the same time as it produces aflatoxin. LumoVision's proprietary, highly sensitive cameras and a powerful LED-based UV lighting system can precisely detect this colour of fluorescence. Within milliseconds of detection, air nozzles deploy to blow contaminated kernels out of the product stream. When dealing with toxins, early intervention is critical. This is not only important in reducing the toxins consumed by pets, but also to lower wastage and the environmental footprint. Without proper cleaning and sorting, poisonous mycotoxins can cause large-scale wastage of materials, mass market recalls, and harm to pets. Dr Gerardo Morantes, Director of Food Safety-Americas Region at Buhler, had the following to say: 'Mycotoxins are a worldwide concern. However, technology made possible by Bühler SORTEX enables a preventative solution, meaning that mycotoxins can be dealt with early, stopping the spread and removing the contamination to meet regulatory standards.' Without intervention, mycotoxin contamination can bare a large cost for businesses, including, brand reputation, market recalls and material waste. With the SORTEX LumoVision, brands can stay profitable, customers can stay happy and pets can stay safe. By Bühler Group
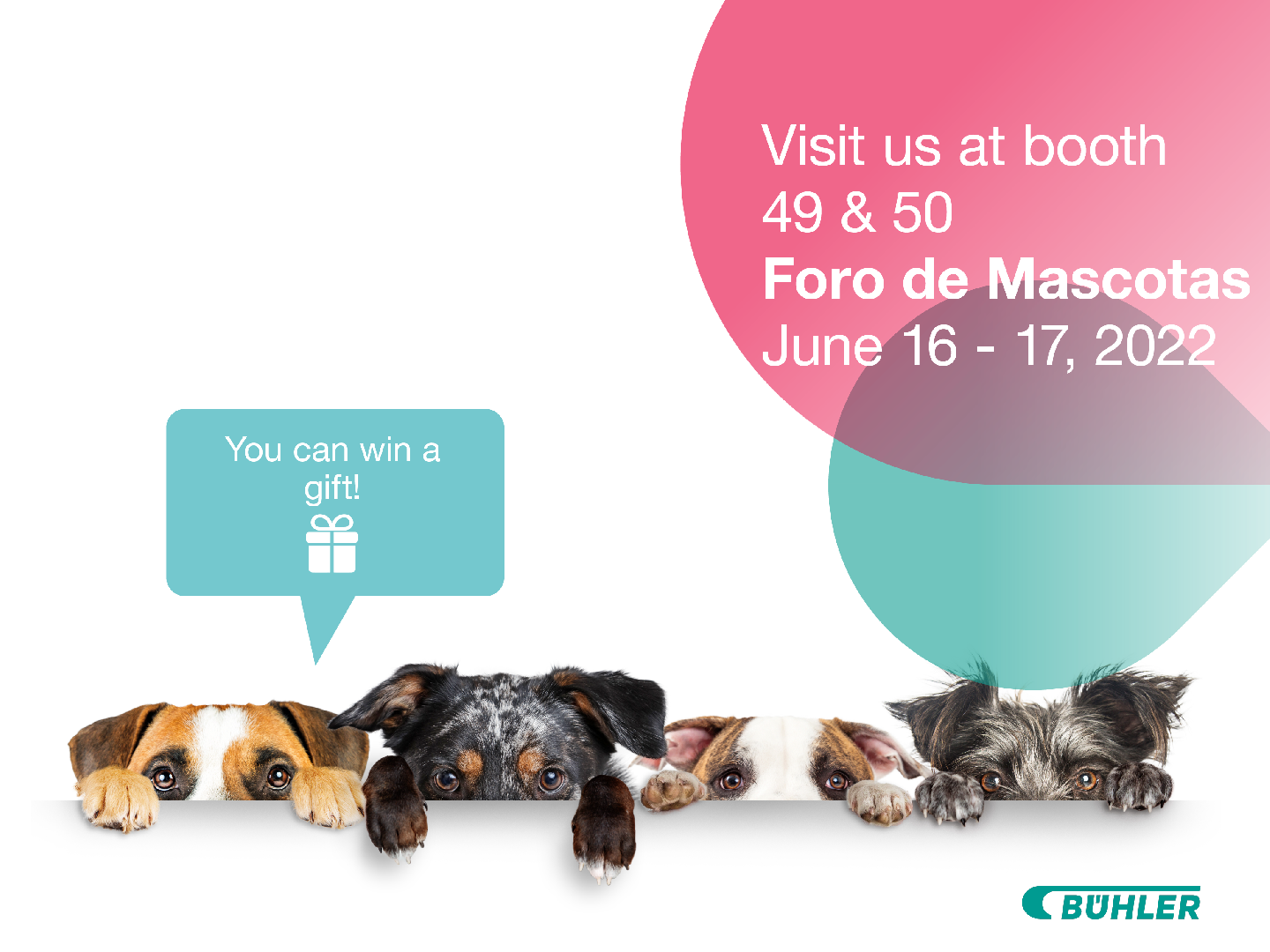
1+ MIN
30/05/2022
Bühler invites you to participate in an event focused on trends in pet food industry!
Foro de Mascotas, June 16 & 17, Expo Guadalajara,Guadalajara, Jalisco. Bühler invest part of its profits in research and development of solutions that accomplish the needs of their clients, developing versatile, flexible, and automated solutions to produce final products with different shapes, sizes, moisture levels and more. In recent times, the food industry has tightened its food safety policies, without leaving behind pet food and aqua feed industries, driven mainly by more informed consumers who became more demanding in the quality of the products they buy. During this event you will be able to enjoy talks focused on the main trends, best practices, and the possibility to meet different suppliers of the industry. Show you some of our Products Multi-impact technology Single screw extruder SmartFeed Dryer Source: Bühler Group
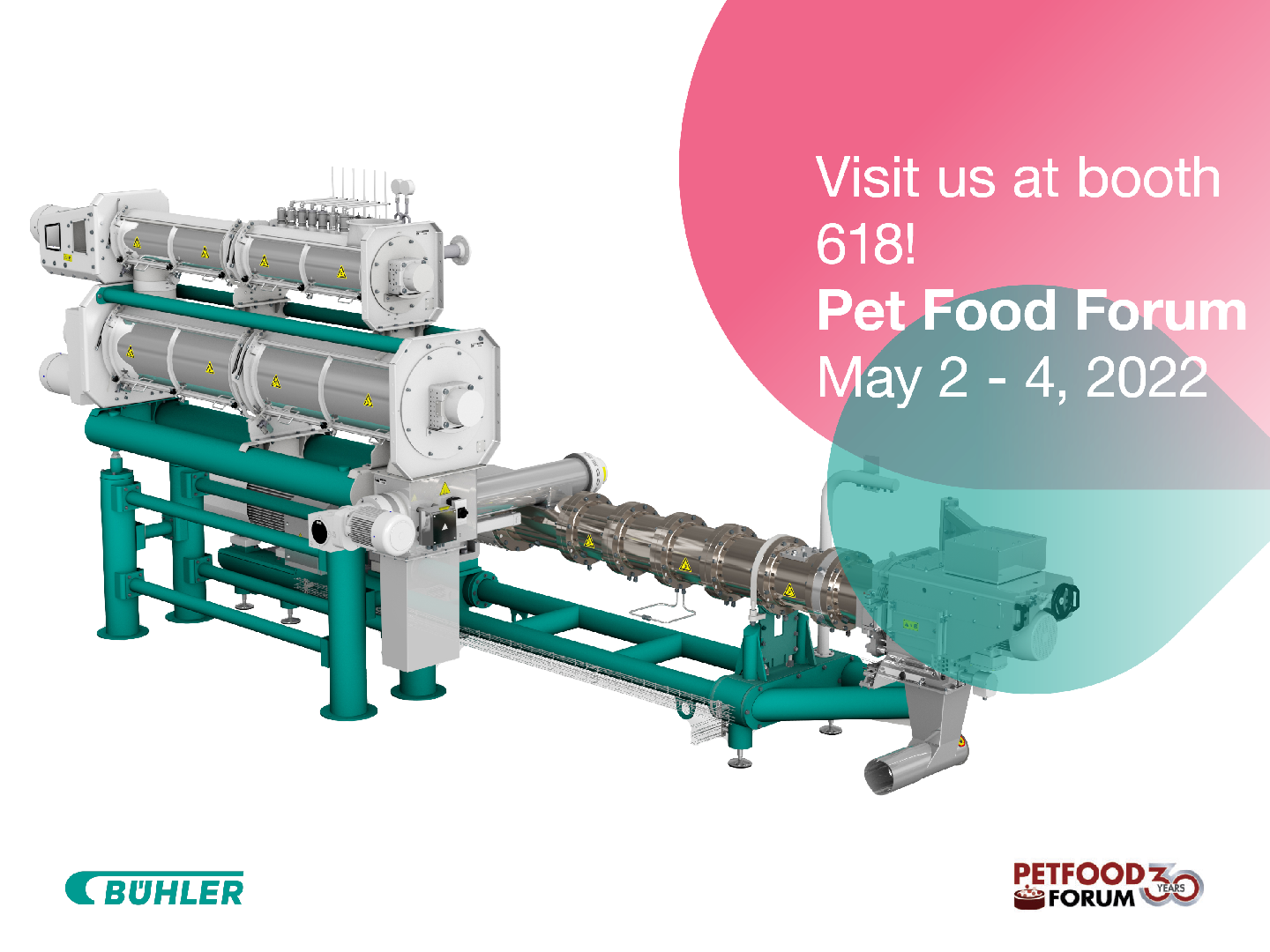
1+ MIN
27/04/2022
Bühler will participate in Pet Food Forum
Discover how Bühler's new Single-screw extruder can change the way you look at pet food production. Its versatile modular design offers real benefits such as minimized downtime for greater profitability and intelligent recipe memory for consistently high product quality. Visit us and our experts will be happy to assist you!
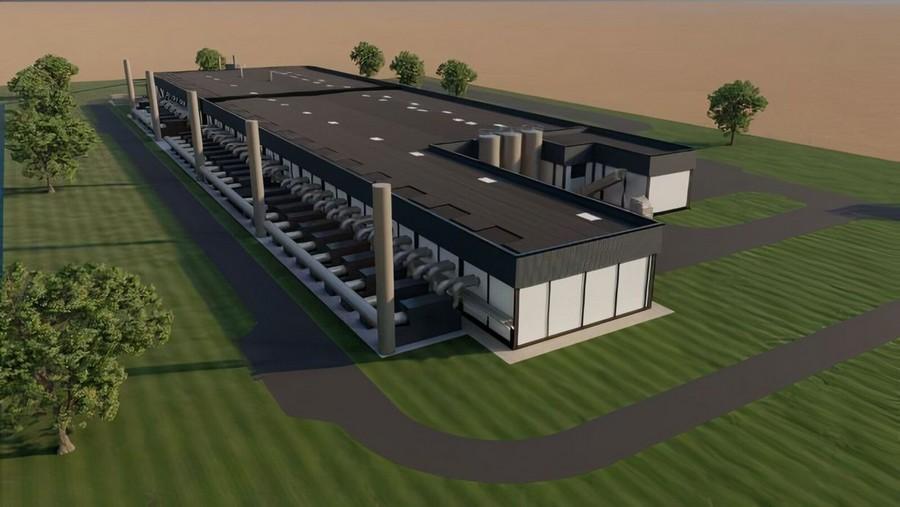
3+ MIN
23/12/2021
Bühler builds large-scale insect plant for Agronutris in France
This collaboration is a major milestone for both organizations. It reinforces Bühler's commitment to ambitious targets that will help mitigate climate change and build a more sustainable food system and supports Agronutris' goal to establish itself as a world leader for sustainable nutrition. The plant is planned to go into operation in 2023. The 16,000 square meter insect plant in Rethel, France, when operating at full capacity, will process up to 70,000 tons of organic residues and produce high-quality protein for the aquaculture and pet food markets every year. 'With the launch of this new site, Agronutris is entering its industrial deployment stage. The facility of Rethel will be our springboard for the further industrial development of our activity,' says Mehdi Berrada, CEO of Agronutris. 'Bühler is a world-leading company with a tremendous experience in the food and feed sector. We trust in their capabilities to support us in the insect industry. This allows our teams to focus on our core activities: insect biology and operational management of our production flow. Our research and development activities make for our competitive advantage.' Bühler's solutions for Agronutris will cover the entire supply chain. This includes feedstock preparation to provide safe, palatable, and nourishing feed to the larvae and a fully automated larvae growth system with sophisticated climate control. Bühler will also deliver the processing line to efficiently transform the grown larvae into protein meal and lipids with consistent quality, as well as the frass (excrement) handling system for a secure offtake of the rearing residues. In addition, Bühler will be responsible for the entire automation and the timely project execution. The latter encompasses engineering, procurement, manufacturing, supply, installation, and commissioning. 'The new project with Agronutris is a milestone for us. It confirms our goal of establishing ourselves as a key solution provider for the insect industry and to increase the inclusion of insect proteins in animal feed. Our solutions contribute to more sustainable feed supply chains,' says Andreas Baumann, Head of Market Segment Insect Technology at Bühler. Growing Demand To feed 10 billion people who are expected to live on our planet by 2050, about 250 million metric tons of additional protein will be necessary every year. This is an increase of 50% compared to today. The industry must address this challenge with a more sustainable production of existing sources of protein as well as alternative sources for direct human and animal consumption. Edible insects can play a unique role in upcycling food waste streams to high-quality proteins, which makes them an increasingly important source of protein while being environmentally friendly. The market of insect proteins as feed is expected to significantly grow in the next ten years. The total turnover of insect feed operators is expected to achieve EUR 2.2 billion per year by the end of the decade. This growth will be led by two main sectors: the aquaculture sector, which will make up for 30% of sales volumes of insect producers by 2030, and the petfood sector, which will account for 40% of the insect protein sales volumes by 2030. Agronutris aims to contribute to the emergence of this industry and to become one of the global leaders of the sector. The growth of its team (joined by entomologists and agro-industry experts), its recent fundraising of EUR 100 million, and the collaboration with major companies such as Bühler, are some of the factors that will allow the company to live up to this ambition. Bühler is committed to reduce water, energy, and waste by 50% in its customers' value chains by 2025. This will help mitigate climate change and be the foundation of a more sustainable food system. Insects offer a unique opportunity. They are not only a healthy source of protein for food and feed, but they can be fed on waste, therefore converting food waste into protein. And their frass can be used as a fertilizer. That is why they are an important pillar in Bühler's strategy to become the leader in sustainable proteins for food and feed. by Buhler group All Pet Food
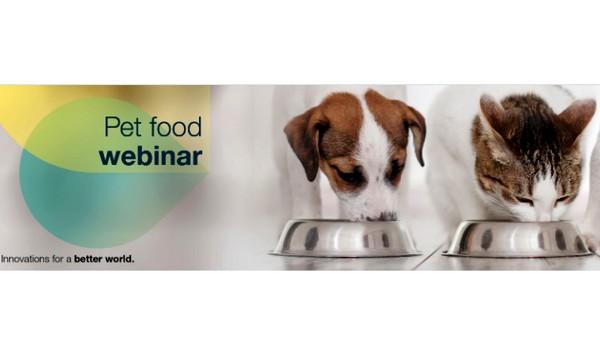
2+ MIN
12/05/2020
Pet Food Webinar - Buhler
In recent years, the requirements for pet food have increased significantly: different sizes and shapes, specific moisture contents and formulations and trends such as fresh meat have to be considered. Additionally, premium pet food needs to be healthy, flavorsome and attractive to animals and their owners.
In this webinar we show you how you can produce high quality pet food in an efficient and safe way. Find out how the new Bühler Single-Screw extruder minimizes downtime and reduces product recalls thanks to its hygienic design.
Overview
Title: Efficient and safe pet food production
Date: Wednesday, May 27, 2020
Time: 03:00 PM Central European Summer Time
Duration: 45 minutes
Content will be in English.
What can you expect from this live experience event:
10 minutes about current trends and challenges of the pet food market
20 minutes about pet food production and the Single-Screw extruder
15 minutes for your individual questions
Speakers
Marcel Ramseyer
Head of Market Segment Pet Food - Bühler AG
Marcel Ramseyer, 37, Swiss and Dutch citizen, has been appointed as the new global segment manager for Bühler's pet food business in January 2020. He holds a degree in mediatechnics, an executive MBA in general management and international marketing and a CAS in Leadership. He has been with Bühler since 1998 and got to know the company from the bottom up, first in various positions in project management, then in marketing- and product management, followed by heading the CF and VN R&D department at Bühler Bangalore / India during a two-year stay abroad. In 2016 he took over the management of the marketing & service department within the business area value nutrition.
Nandor Caluori
Area Sales Manager South America & Switzerland (Business Unit Human Nutrition) - Bühler AG
Since January 2020, Nandor Caluori is responsible for the Sales & Service business of the Latin-American & as well the Swiss market regions of the Human Nutrition business unit (HN-BU). He is operating out of the Sales-Excellence team at Bühler's headquarter, based in Uzwil Switzerland. Nandor is 33 years of age & owner of the Swiss and Italian citizenship. With Bühler he has been since 2002 & has therefore a profound knowledge background from various different positions within Bühler (HN-BU Customer-Service, Upgrade-kit/ Retrofit-sales business for Europe, global commissioning engineer). Education wise he holds a Bachelor of Science degree in Business Administration & has a mechanical background due to his apprenticeship & on-the-job experience.
To be registered in the Webinar Click HERE
by All Extruded
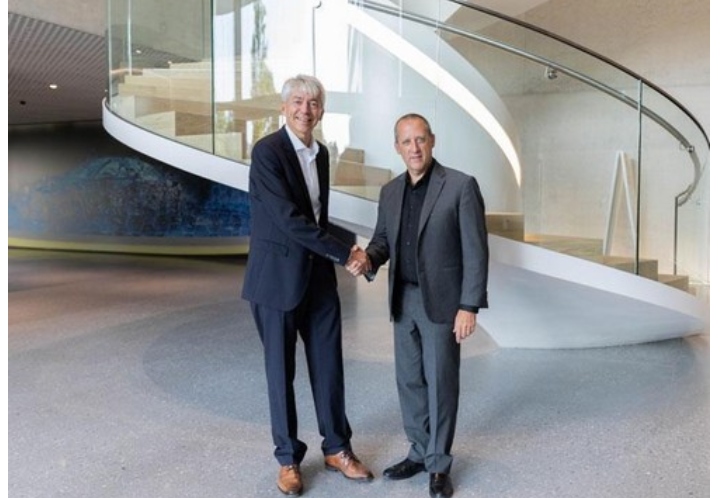
4+ MIN
04/09/2019
Buhler and Premier Tech to Form a Strategic Cooperation
Swiss Bühler Group and Premier Tech from Canada, announced the formation of a strategic cooperation for industrial flexible packaging solutions. Both companies agreed to build a design and manufacturing center in China. 'Combining the portfolio and expertise of Premier Tech and Bühler will enable future packaging solutions which are significantly more efficient, accurate and food safe by using automation technologies', says Johannes Wick, CEO of Bühler's Grains & Food business. 'The two companies are complementing each other in a perfect way with Bühler's strong footprint and market position in China and Premier Tech's recognized know-how in the field of automated packaging technologies,' says André Noreau, CEO of Premier Tech's Systems and Automation business. In grain processing, packaging is the last step before transporting flour to bakeries and other food processors, rice to distributors or pellets to farms. In many cases – especially in developing countries – the bagging operation is still done manually. This is not only inefficient, costly, and slow, but also implies a certain variation of weight and therefore a higher give away of the packaged goods. Palletizing solutions are increasingly important to allow for efficient warehousing solutions. The market and technology leading companies – Premier Tech in packaging and Bühler in grain and food processing – are now establishing this strategic cooperation to meet these market demands and create new cost-effective packaging solutions. Bühler brings its know-how of high-quality manufacturing and supply chain management in China as well as its digital solutions, whereas Premier Tech contributes with its superior packaging expertise and technological leadership in this field. In bringing these competencies together, the strategic cooperation will develop automated, food safe and accurate bagging and palletizing solutions. The strategic cooperation will allow Bühler to provide better turnkey projects with competitive packaging solutions from China while continuing to deliver high-end products such as Bühler's bagging station Maia from its own manufacturing network in Europe. At the same time, Bühler will continue to design and market their proven weighing portfolio (since scales such as Tubex are not part of the agreement) and further improve its digital services allowing for full transparency and traceablity. Premier Tech will gain better access to the Chinese market by using the cost-effective and modern packaging solutions arising from the strategic cooperation, or by combining them to its internationally renowned CHRONOS technology portfolio in weighing, bagging, and palletizing. This strategic cooperation is planned to result in a joint venture for design and manufacturing during 2020, with Bühler focusing on sales of turnkey plants around the world, and Premier Tech on packaging systems in China. Both companies will continue to sell their products through their existing channels. About Premier Tech Making a difference, this is what we are all about at Premier Tech. One team driven by the shared passion to deliver solutions that we better the lives of people, businesses and communities. At Premier Tech, People and Technologies connect in lasting, transformative ways, giving life to products and services that help feed, protect and improve our world. We are committed to creating sustainable solutions that help bring beautiful gardens to life, increase crop yields, improve the efficiency of manufacturing facilities, treat and recycle water, and much more as we keep innovating. For more than 95 years, Premier Tech has been growing internationally, driven by the collective power of its 4 500 team members in 27 countries. Backed by a quarter-century-long track record of solid growth, Premier Tech today records sales of nearly CAD 1.0 billion. About Bühler Billions of people come into contact with Bühler technologies to cover their basic needs for food and mobility every day. Two billion people each day enjoy foods produced on Bühler equipment; and one billion people travel in vehicles manufactured with parts produced with our machinery. Countless people wear eye glasses, use smart phones, and read newspapers and magazines, all of which depend on Bühler process technologies and solutions. Having this global relevance, we are in a unique position to turn today's global challenges into sustainable business. We want every human being to have access to healthy food. We want to do our part to protect the climate with energy-efficient cars, buildings, and machinery. Our motto is creating 'innovations for a better world.' Bühler invests up to 5% of turnover into research and development. In 2018, over 13,000 employees generated a turnover of CHF 3.3 billion. As a Swiss family-owned company, Bühler is active in 140 countries around the world and operates a global network of 30 production sites. by All Extruded
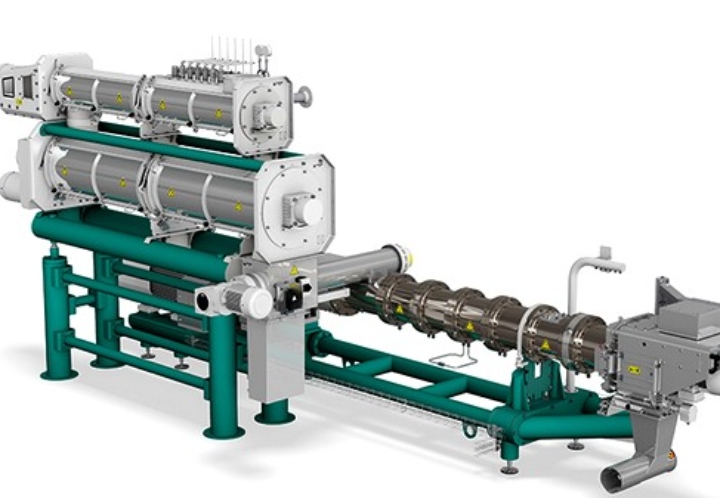
3+ MIN
22/07/2019
Bühler Launches Single-Screw Extruder PolyOne
Bühler has launched the multifunctional single-screw extruder PolyOne for the pet food and aqua feed industry at VICTAM International 2019 trade fair. At VICTAM International 2019 trade fair, Bühler is showcasing solutions for the entire feed value chain, with a special focus on how to use digital services to make the feed industry safer, and more profitable. LumoVision, the revolutionary data-driven maize sorting technology, finds its way into the feed processing industry. Today, Bühler has launched the multifunctional single-screw extruder PolyOne for the pet food and aqua feed industry. Bühler has launched its new single-screw extruder PolyOne today, designed to consistently deliver high product quality for the pet food and aqua feed industries. 'PolyOne enables our customers to maximize their productivity, and helps to prevent product recalls,' says Christoph Naef, Head of Business Unit Nutrition at Bühler Group. PolyOne meets highest food and feed safety standards thanks to its perfected hygienic design. It is a modular system so Bühler can adapt PolyOne to customers' specific needs, such as higher capacities. Kubex T: High-capacity pellet mill with full process transparency Kubex T provides highest process transparency thanks to an application that connects it to Bühler Insights, the pioneering cloud platform for the food and feed industry. A dashboard visualizes data for customers, making their processes transparent. This allows for seamless tracking and brings production downtimes to a minimum. Algorithms and Bühler experts help millers to optimize the mill's parameters. With it, customers achieve higher profits and lower production costs thanks to innovations in intelligent process optimization. Kubex T is designed for high-capacity pelleting. Customers will use up to 20% less energy compared to conventional pellet mills, benefit from high production capacities of up to 80 tons per hour, and a customer-driven design, all of which are the result of extensive Bühler research and development in cooperation with leading feed millers. Bühler LumoVision: data-driven grain sorting technology for feed and food Bühler showcases its breakthrough sorting technology for the feed industry. LumoVision minimizes toxic contamination in maize and improves yield, by identifying and removing cancer-causing, aflatoxin-infected grains. It does this more accurately and at greater speed than any previous solution. Developed in partnership with Microsoft, LumoVision is a significant advance for the maize processing industry in its fight against toxic metabolites produced by fungal molds called mycotoxins, the most poisonous of which is aflatoxin. The innovation can eliminate up to 90% of contaminated maize. 'Advances in digital technology, together with our sorting, food, and feed safety expertise, make this an unrivalled system that contributes to solving a major global security challenge,' says Matt Kelly, Managing Director of Digital Technologies at Bühler. Aflatoxin is classified as a primary human carcinogen by the International Agency for Research on Cancer. Approximately 500 million people worldwide are at risk of exposure to it and it is estimated to cause up to 155,000 cases of liver cancer every year and contribute to stunting the growth of millions of children. by buhlergroup.com