Liquid palatants
Liquid palatants are delivered in bulk tankers or in an intermediate bulk container (IBC). Tankers are advised when large quantities are used; otherwise IBCs are recommended. IBC use also depends on the factory layout or use of multiple palatants. Commonly stored on site in agitated storage tanks, liquid palatants perform best when maintained between 70°F and 95°F.
Due to natural physical characteristics, liquid products may exhibit some separation. The separation will not have an effect on palatability and can be controlled by agitation just before use. When a tank is used to store the bulk delivery, the tank must contain an agitator to blend the product before use to achieve homogeneity. Mix the product just enough to keep it moving and to avoid inclusion of air. Too much air inclusion can cause foam which could affect the product quality.
Blending the product in the tank will also prevent potential formation of a water layer on top created by condensation when temperature differences occur. A watery layer will change the pH and preservative concentration causing a potential risk for mold and other bacteria to grow on top of the product. An agitator in the tank will also help prevent this watery layer.
To apply liquid palatants, suitable coating systems include drum coaters, batch coaters, screw coaters, augers or spinning disks. Set up the system to add the fat first, then the palatant. (Figure 1).
Once complete, blend kibbles properly to be sure a homogeneous coating is reached and to allow the fat and palatant to fully absorb.
Blending time depends on factory layout, required throughput and coater type.
For optimal kibble performance when applying a liquid palatant:
Keep air out of the palatant application process. Include baffles in mixing tanks and eliminate free-fall product return on recycle systems to help prevent fat from oxidizing, which can decrease palatability performance.
Avoid over-application. Carefully synchronize the kibble feed rate and the palatant application rate to prevent excessive application, which could increase moisture and lead to mold growth if not properly monitored during production.
Retention time. After the fat and digest dosing, a certain retention time allows flavors and moisture to distribute homogeneously over the kibbles.
Choose the correct spray nozzle for your application. Two recommended nozzle types are flat spray pattern and full cone spray pattern. The right nozzle choice depends on coater type and setup. The size, or opening, of the nozzle depends on the amount of the liquid you want to apply. The nozzle should form very small droplets, not a mist or a pouring liquid.
Marketplace
Prevent overspray. Aim spray nozzles to avoid excessive buildup on the augur or coating drum, which could compromise pet food quality over time as fines will stick to the liquid creating lumps composed of materials from multiple batches.
Carefully position palatant and fat spray nozzles. Ensure no more than 10% overlap in palatant spray patterns to support consistent performance. Also strive for no overlap between the fat and palatant application.
Dry palatants
Pet food palatants are packaged in standard dry bags or bulk bags. palatants are added after the fat or liquid palatant application. (Figure 2) The fat or liquid palatant acts as a tacking agent and is an integral part of the total palatability solution.
Dry palatants are fed into the coating system using a loss-in-weight or a volumetric feeder. Pulse dosing should be avoided to obtain a homogeneous spreading of the powder. The hopper of the feeder should contain an agitator to avoid bridging of the powder which would disrupt an even powder supply. (Figure 3: Palatant Application Process)
For optimal kibble performance when applying a dry palatant:
Coat kibbles evenly. Discharge kibble onto a plate or splitter to facilitate continuous flow of the desired kibble quantity which will secure accurate palatant dosing.
Avoid impeded flow. The small size of the feeders often requires the use of vibrators or flow assist devices.
Avoid palatant buildup on the coating system. Maintain the desired kibble level before applying dry palatant to avoid such buildup.
Source: AFB Intenational
You could be interested: Delayed Dry Palatant Coating: Does it Affect Palatant Recovery Rate and Palatability?
About company
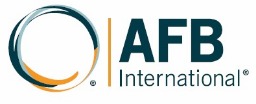
About company
WHAT WE DO
At AFB International, we develop and produce a full range of liquid and dry palatability enhancers. We use high-quality ingredients proven to optimize companion animal response and consumption.
Our specialty? Meeting your unique needs with custom support. Our worldwide staff of technical experts is ready to assist you with all aspects of palatability enhancement, from product development and testing to processing, logistics and more.
HOW WE WORK
Our successful customer relationships are built on clear, consistent communication—starting with really listening to understand your needs so we can respond quickly and effectively. And we keep listening. AFB scientists and technical service managers routinely travel to customer facilities to clearly understand the challenges at hand and the systems in place. Then we can recommend the best viable solutions.
OUR TEAM
AFB is dedicated to improving the health and wellness of companion animals worldwide through superior products and services. Our diverse, committed team works collaboratively to serve our clients. Get to know us—and let us know how we can help you!
HISTORY
AFB launched in 1986 and has grown to be the global science and technology leader in pet food palatability. Headquartered in St. Charles, Missouri, USA, AFB is a global company with state-of-the-art facilities in the United States, Argentina, Brazil, Mexico, the Netherlands, China, and Australia. AFB is a wholly owned subsidiary of Ensign-Bickford Industries, Inc., a privately held, family-owned, professionally managed technical business that traces its roots back more than 185 years.