Introduction
The Extrusion process is a thermo-mechanical process that consists of forcing a product to pass through one or more holes of a specific size under pressure and temperature thanks to the Archimedes screw concept (also known as "endless screw").
The extrusion processes in the processing of extruded pet food and aquaculture, aim to achieve the cooking of the mixture of raw materials and ingredients giving it the form of croquette (pellet / kibble) that facilitates its subsequent handling.
The most important things that take place inside the extruders are the gelatinization of starches and texturization of proteins, both processes help to the greater digestibility, as well as to form a structure and texture that hosts other ingredients, minerals, fats in a stable and uniform way.
For a good gelatinization of starches and texturization of proteins moisture is needed (the one that is added in the form of liquid water and steam in pre conditioning and / or extruder), temperature is needed, part of the temperature input is given by the addition of steam, but the most important is carried out by the mechanical and friction work produced by the screws. And mechanical energy is also needed, granted by the shearing action of the screws.
Today there are two technologies available for extrusion, these are single screw (SSE) and twin screw (TSE). In this article we will talk about the features, advantages and disadvantages of each of these technologies.
Single Screw Extruders
In Single Screw Extruders we observe as a characteristic that the advance of the screw moves the materials through the channel by developing a 'drag flow', whose speed is directly proportional to the speed of the screw. Due to the constraint of the die in the discharge of the extruder, there is a "backpressure flow', which goes in the opposite direction to the drag flow. Therefore, the 'flowrate" in single screw extruders (SSE) is equivalent to the drag flow rate – backpressure flow rate.
The flow dynamics in the screw channel shows us that the fluid particles travel at different speeds and that they do not interact in their entirety, resulting in a dispersion of dwell times and an uneven mixture.
Consequently, the heat transfer as well as the entry of mechanical energy in the cooking section are very limited. In addition, the length of the shear depends on the space, which generates heterogeneities of the melting properties (cooking duration, temperature and pressure).
In short, Simple Screw Technology (SSE) features:
- A single process section.
- Dependence on performance and screw speed.
- A single operating point (performance combined with maximum screw speed and die opening area).
- Limitations in mixing, which limits heat transfer, mechanical energy input, and generates heterogeneities in particle fusion (cooking duration, composition, temperature and pressure).
- The higher the screw wear, the lower the extruder performance. A reduction of 10-20% can be observed during the life of the screw.
- 'Lubrication factors' in the composition of the mixture generate runoff, which reduces the performance of the extruder and the addition of mechanical energy.
Twin Screw Extruders
Twin Screw Extruders (TSE) have multiple process sections in series, (melting/cooking, vapor/gas extraction, vapors/positive displacement pumping), thanks to the different restrictions generated by the work of the screws. The process sections show high levels of mixing, good heat transfer and important shear work (addition of mechanical energy).
In the TSE, a very intense mixture is observed in the coupling area of the screws (macro mixing and micro mixing).
Consequently, the heat transfer coefficient in the sections is very high. Homogeneous fusions can be obtained, with a very good link of lipids. The expansion after traversing the die develops consistently, leading to an excellent density, texture and shape of the product, as well as a uniform final density and color.
In short, Twin Screw Technology (TSE) features:
- Multiple process sections in series.
- The performance and speed of the screw are unlinked. Therefore, for a mixture formulated, the TSE are characterized by its many operating points. In addition, the screw profile can vary extensively to modulate the addition of mechanical energy.
- The mixing process is very intense, which gives great benefits in relation to the quality of the product.
- The slippage of the mixture is compensated by the positive displacement pumping of the screws.
- Less sensitivity to changes in raw materials.
- Increased tolerance to changes in moisture, fiber aggregates and fats.
- Better quality and consistency of final product.
- Greater overall process flexibility.
- In Aqua Feed, the best possible uniformity and high level of degassing decreases the chances of pellets floating when Sinking Aqua Feed is produced.
- In Aqua Feed it allows us to produce, thanks to the action of the two screws, micro pellets up to 500 microns (0.5 mm).
- In the particular case of the Twin Screw Extruders of the French Company "Clextral" (top image of Clextral extruder), the proven advantage of being able to achieve the high quality of food by working with 2 to 3 % less humidity is achieved, implying significant energy savings in the subsequent drying process.
Conclusion
Both extrusion technologies are widely used in the pet food and aqua feed production sector.
Single Screw technology typically requires a lower investment cost, and somehow lower spare parts costs.
While the Twin Screws requires a higher investment that brings as advantages the possibility of working with a wider range of raw materials, with more fibers, more vegetal proteins and higher fat content.
Author: Eng. Diego Clivio
More info: www.cliviosolutions.com
You could be interested: New research brief: Dental stick extrusion utilizing spray dried plasma (SDP)
About company
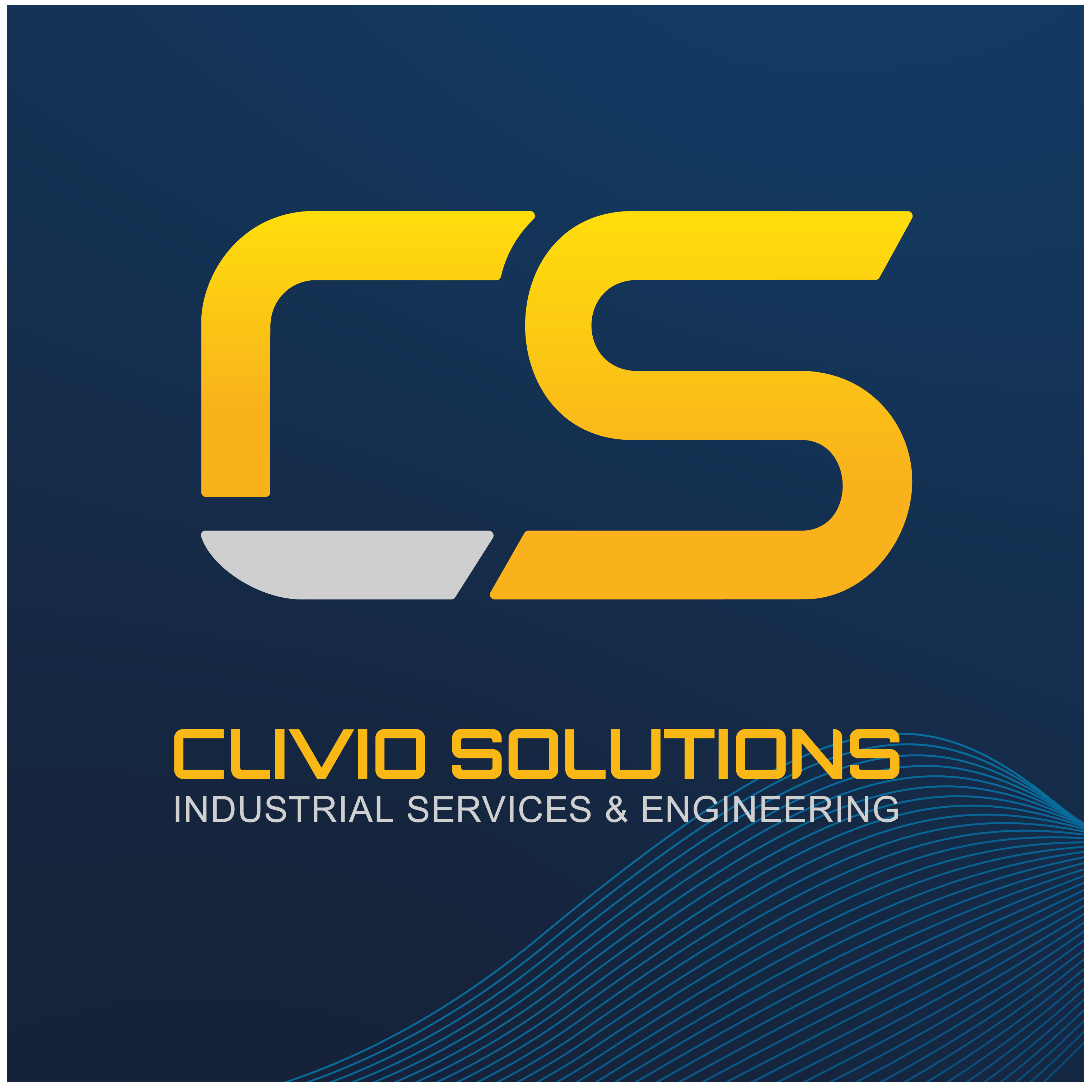
About company
At Clivio Solutions, we offer engineering services and high-level consulting, specializing in balanced food. Our experience enforces with prestigious associations, ensuring security, cutting-edge technology, and intelligent and sustainable solutions.
Our value proposition is based on integrity, a wide range of solutions, and a broad geographic breadth. We stand out for encouraging synergy being dedicated facilitators who offer continuous support characterized by unequaled reliability and quality.