

Cablevey Conveyors
https://cablevey.com/
Cablevey Conveyors
About the company
Cablevey Pet Food Conveyor Systems
Cablevey Pet Food Conveyor Systems are suitable for moving all sorts of pet food materials and mixes. No matter what form your materials are in, we can move them in a gentle and sanitary manner. And our pet food conveyors can be engineered to service any part of the production process from processing to mixing to packaging.
Flexible Design
Our cable and tube conveyor systems are modularly designed to offer flexibility for wide-ranging applications. Component parts come in a variety of sizes, tube diameters and tube materials. We also offer a full range of feeders, cleaning and transfer system components. No matter what your processing facility layout, we have pet food conveyor solutions for you.
Custom Solutions
Each and every pet food conveyor system is custom specified by our engineering department. This ensures that all systems are optimized to client needs. Design considerations typically include how much can be moved without breakage, how far, how high, and how fast you need to move materials. The configuration and available space within processing environments are also taken into consideration. The bottomline is that our engineers and library of system parts can solve just about any pet food conveyor movement needed.
We’ve engineered pet food conveyor solutions for production facilities large to small.
Products
Company News
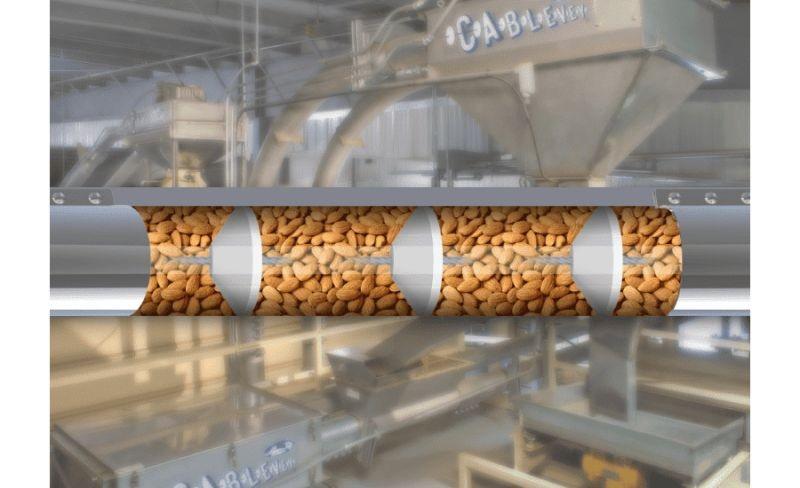
6+ MIN
04/12/2023
Countdown to Pet Food Conveyor Launch: Starting Up On Time and With Confidence
To move delicate pet food products or powders, most processors do extensive homework before purchasing a tubular drag cable conveyor to ensure that it meets their needs in terms of function and price. After the purchase, the conveyor must be expertly assembled and tested to ensure smooth production startup and continued performance. The challenge is that the typical third-party contractors installing various plant systems might need to become more familiar with specialized pet food conveyors and, thus, are more prone to make costly errors. A more prudent choice is using the OEM's team of experienced technicians. The OEM's experts have the advantage of designing the specialized conveyor and understanding its installation, operational requirements, and potential problem areas. 'If a tubular drag cable conveyor is installed incorrectly by a third party, it often needs to be completely pulled apart and rebuilt, which is costly and time-consuming. If the conveyor is run incorrectly, damage will occur, and components must be replaced. All this only delays startup,' says Terry Derby, Director of Parts and Field Service for Automated Handling Solutions (AHS). AHS is the service-focused subsidiary of Cablevey Conveyors, an Oskaloosa, Iowa-based conveyor manufacturer that has been designing, engineering, and servicing enclosed cable and disc tube conveyors for 50 years and is in more than 65 countries. As a solution, pet food processors seeking superior conveyor performance from the start rely on expert-supervised installation and commissioning to ensure they will be ready to run products on time, at the necessary volumes. Today, a tubular drag cable conveyor requires considerable expertise to install. These systems gently move material through a sealed tube using a coated, flexible, stainless-steel drag cable pulled through on a loop. Solid circular discs (flights) attach to the cable, pushing the product through the tube without air. 'This type of conveyor is uniquely engineered to transport delicate materials gently. The tubes form a continuous loop that must be carefully assembled for a tight fit to ensure no misalignment or gaps between sections. While the modular components lend great flexibility to system design, each component must act in concert with the rest for proper conveyor functionality,' explains Derby. After selecting and purchasing a conveyor, the pet food processor's next step is installing it, which often requires professional assistance. Reliability Starts with Supervised Installation Whether relying on internal staff members for installation or contracting the job to an outside team of millwrights or skilled pipefitters, supervised conveyor installation can ensure proper system installation. Getting expert assistance is still essential during installation, even with the manual that has detailed instructions and QR-code links to videos for each conveyor component. 'Supervised installation is important to ensure that your system is installed properly so you don't run into maintenance problems due to an improper install,' says Derby. Derby insists that 'supervised installs are probably the most important support service we offer.' This step is often neglected when a less experienced third party performs the installation, which can escalate costs. At this point, AHS is frequently asked to complete final preparations and correct any problems before production startup, a process known as commissioning. 'When a processor brings us to their facility after declining a supervised installation, we often have to work backward for a day or two to correct issues. Having us there for supervised installation eliminates the need for correction and any idle contractors waiting on us for the repair, so it pays for itself,' says Derby. In the case of AHS, the company's technicians have logged hundreds, if not thousands, of hours on-site in various manufacturing facilities worldwide. This singular focus gives them the knowledge and expertise to streamline the installation process and prevent issues that can lead to system inefficiencies, product loss, or complete system failure. As part of the supervised installation, skilled technicians ensure the correct positioning of the conveyor's hangers and the proper torque for couplings. The system is properly cleaned to remove any metal fragments or foreign contaminants introduced during installation. In addition, the technician confirms that all conveyor inlets are in place and that all discharges are functioning. Even seemingly minor gaps or misaligned areas in the conveyor tubing can become a severe issue. 'If gaps are in the conveyor's tubes, the discs will 'catch' when crossing the joint, causing excessive wear on the cable and motor. If not corrected, this could lead to premature failure, production downtime, and added repair and replacement costs,' says Derby. According to Derby, another common wear item in tubular drag cable conveyors is sweeps, areas where the tube changes direction. He explains that sweeps are where the cable is under the most significant tension and where the discs rub inside the tube. Since sweeps show the first signs of wear, proper installation can reduce the wear and significantly prolong tube and cable life, simplifying maintenance. 'With a supervised install, processors can ensure that their conveyor is assembled correctly to enable seamless startup, reliable production, optimal output, and greater longevity for the system and its parts. Our reputation is on the line to get it right from the start,' says Derby. In addition, a supervised installation includes a full report outlining actions to correct any issues found. Due to the attention to detail, a supervised installation also preserves the standard warranty for the system's components. Of course, operators also play a critical role in conveyor performance. For this reason, having experts onsite can be one of the best ways to train the operators and maintenance crew on properly running, cleaning, and maintaining the system. Reliable Production Requires Expert Commissioning When the installation is complete, the next step is to schedule commissioning. The average commissioning visit for a single-system installation usually lasts an entire day. The onsite commissioning process readies the conveyor for total production and identifies any immediately correctable issues to keep the startup on schedule. At this point, the system must be installed entirely, including all mechanical and electrical components. The conveyor material must also be ready for introduction to the system. This is where a botched installation by a third party can come to light without supervised installation by the OEM. 'We are often asked to 'fix' poor installations by third-party contractors. We have had to tear whole systems apart. This frequently requires a complete rebuild and replacement of damaged parts, which adds cost, creates downtime, and delays startup,' says Derby. In the case of AHS's commissioning service, the technician conducts an inspection using a camera that runs through the entire system layout to ensure that everything is correctly assembled and ready for testing. The technician then performs a test run of the product, from the inlet feed through the sweeps to the discharge outlet, and verifies that it flows at the desired speed. 'Tailoring the conveyor to the material conveyed can require adjustments to fine-tune the process. With the commissioning, the goal is to increase efficiency, production volume, and reliability,' says Derby. He adds that 'checking the system's health' also uncovers any issues that might arise, which technicians can address to prevent production downtime. He points out that commissioning also extends Cablevey's standard warranty. As a final step in the commissioning process, the technician issues a report for the processor that documents all findings from the full-system inspection. Completing conveyor installation, commissioning, and start-up is only the start of the OEM's and processor's relationship since the system's lifespan can be decades. In addition to traveling on-site for emergency service calls, the company offers an annual service visit to conduct a detailed system inspection and address any issues, identify worn parts, ensure predictive maintenance is being conducted, and provide any additional training needed. This complete system audit aims to extend the conveyor's lifespan and prevent unexpected downtime. 'Our mission is to provide conveying equipment and ensure it performs as required, with minimal downtime and maintenance. Once a pet food processor buys a system, they become part of our family. We will continue to support them every way we can, even as their needs evolve,' concludes Derby. By Del Williams is a technical writer based in Torrance, California. Source All Pet Food
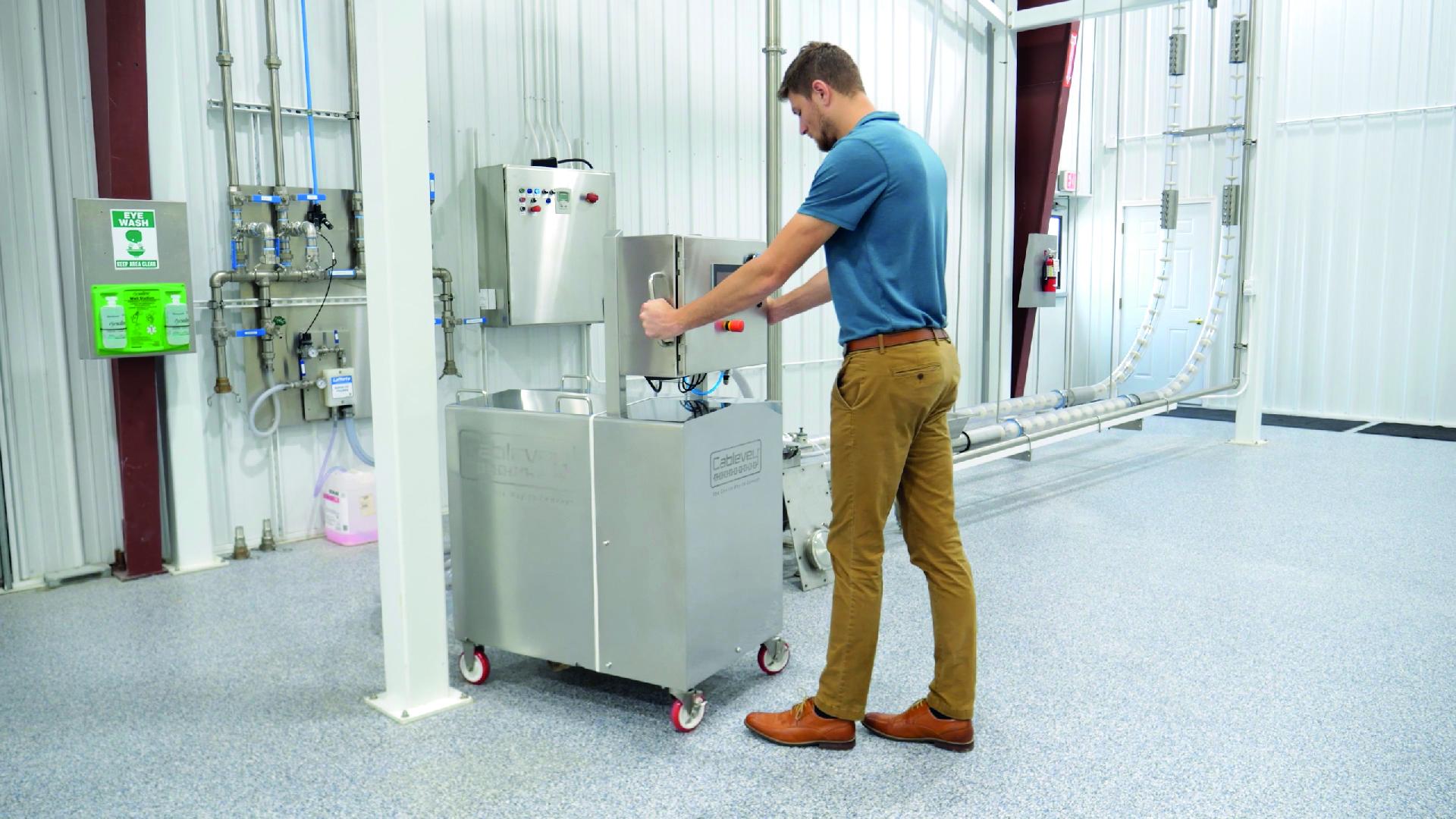
4+ MIN
27/11/2023
Mobile 'Smart Cart' Automates Food Conveyor CIP for Pet Food Manufacturers
To promote food safety and sanitary compliance, pet food manufacturers are increasingly seeking the ability to clean-in-place (CIP), an automated method of cleaning the interior surfaces of tubular drag conveyors without disassembly. Now, with the advent of mobile tools like an innovative 'smart cart' that quick-connects to any tubular conveyor and enables simple, customizable 'single button cleaning recipes,' CIP is becoming easier, faster, less labor-intensive, more repeatable, and almost fully automated. Tubular drag conveyor systems gently move product through a sealed, enclosed tube using a drag cable and circular discs pulled through on a loop, so they are ideal for delicate items. Designed to handle a variety of different forms and sizes, from kibble to seeds or pellets and nutrients, tubular conveyors maintain both quality and proper proportions. In a wet CIP process, the system is flooded with water, flushed, rinsed, cleansed, and thoroughly sanitized. Although the process is very effective, streamlining its automation and simplifying the process for all a facility's tubular drag conveyors has been a priority for leading innovators in the industry. 'The standard system required port hookups to water lines and installing piping. The processor also had to make decisions, such as which water temperatures to utilize, or whether to use a cleaning solvent - and the correct amount to add manually,' says John Adair, Engineering and Quality Director for Cablevey Conveyors, an Oskaloosa, Iowa-based conveyor manufacturer that has designed, engineered, and serviced enclosed cable and disc tube conveyors for 50 years, and is in more than 65 countries. To simplify the wet cleaning process, Adair and his engineering team at Cablevey have developed a small, mobile 'smart cart' with integrated water line hookups that a single technician can easily take to any tubular drag conveyor in a facility. The cart is specifically designed to be a fraction of the size of similar carts on the market to facilitate mobility. When the cart is in position and connected to water lines, the CIP process is automated and controlled by a programmable logic controller (PLC) that reduces the need for manual labor and virtually eliminates the risk of improper cleaning. 'Once it is set up, all you do is press a button, and it will bring in the required amount of water at the correct temperature with the necessary amount of solvent for cleaning,' says Adair. The smart cart is designed to store and utilize pre-programmed CIP recipes to flush various residual materials from the tubular drag cable conveyors in a facility before new production runs. The cleaning recipes enable even those with very little training to use the cart, which is helpful in today's tight labor market and allows the technician to move on to other tasks once the cleaning process begins. The use of easily executable recipes ensures a superior, repeatable clean that essentially 'error-proofs' the process. This is particularly important when the technician may be new or less familiar with the production equipment. 'Depending on the product conveyed, sometimes all you need is a wet rinse or a specific cleaning solvent. All that information is saved, so after the first cleaning, it can be automatically repeated. Just push a button to start the appropriate recipe, whether you have one conveyor running multiple products or dozens of conveyors running various products,' says Adair. To meet strict compliance standards, the smart cart also documents all critical CIP information, such as water volume and temperature, chemicals used, and cleaning time by date, in an easily retrievable data log. Since decreasing production downtime between conveyor cleanings is a priority for pet food manufacturers, Cablevey provides new capabilities with the cart that expedites the CIP process. Currently, the CIP process floods the tubular conveyor system but is not designed to clean the discs specifically. 'Operators would manually clean each disc and advance the system disc by disc when the discs had to be cleaned of particularly viscous substances,' says Adair. Once it is set up, all you do is press a button and it will bring in the required amount of water at the correct temperature with the necessary amount of solvent for cleaning. Now, as an option on the cart, a disc washer can be integrated with the conveyor turnaround to spray a pressurized cleansing solution on the discs. This helps to remove stickier substances that could remain after routine CIP cleaning. 'The disc washer sprays high-pressure water directly on the discs, so it acts like an automatic car wash. At the push of a button, the discs and cable are run through, and spray cleaned, which reduces CIP time and eliminates the need to manually clean the discs,' says Adair. To further reduce downtime, Cablevey also offers a new sanitary blower option. 'After the wet CIP process, a sanitary blower attachment on the smart cart can dry the discs and other parts of the system 75% faster than typical air drying,' says Adair. He points out that the faster the conveyor is cleaned and dried after a product change, the sooner it can be put back into service, which improves profitability. According to Adair, Cablevey's Mobile Smart Cart was already available since it was officially unveiled at Pack Expo, a premier packaging and processing show held at the Las Vegas Convention Center in September. The event featured full-scale setups of machinery in action. The company also offered traveling demo smart cars to customers in September for free so clients could test drive the units. Pet food manufacturers can now purchase the demonstration unit used in their facilities, with hands-on training available immediately. While the pet food manufacturing industry is aware that automated CIP can improve conveyor system production uptime, barriers to implementation have slowed adoption. Utilizing a mobile smart cart with integrated water hookups will help manufacturers easily implement CIP in tubular drag conveyors throughout their facilities: expediting conveyor cleaning, production changeover, and sanitary compliance. By: Del Williams - Technical writer based in Torrance - California Source: All Pet Food Magazine
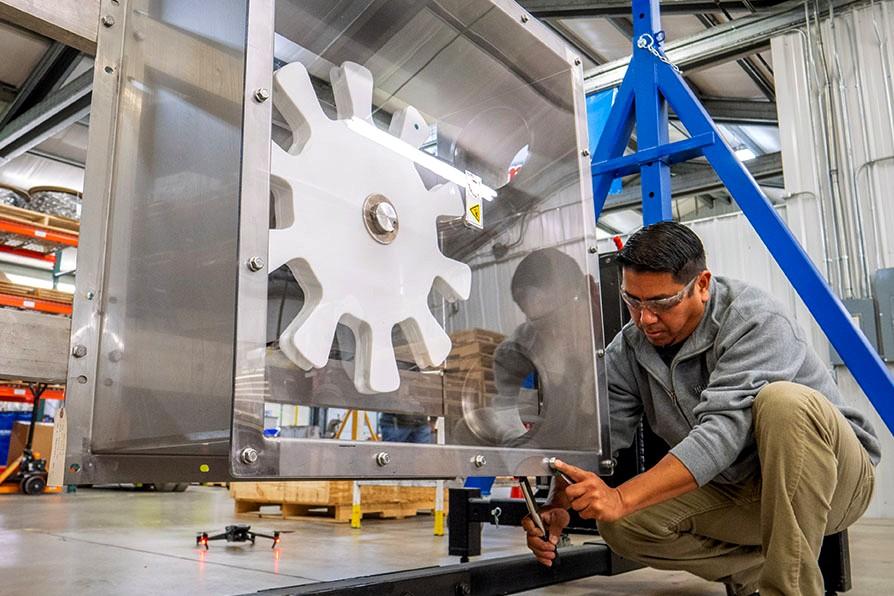
4+ MIN
29/08/2023
New German test facility allows processors to try solutions before they buy
These systems come as an investment, making it crucial for manufacturers to understand what they're buying before pulling out the company credit card. This is where OEM test facilities come into play, which offer processors the opportunity to try before they buy, often supported by the expertise of seasoned process engineers and salespeople who represent the supplier and its solutions. Testing, testing According to Emmanual Ricohermoso III, Ph.D., testing and facility manager at Automated Handling Solutions (AHS) Germany GmbH, parent company of Cablevey, testing equipment before making a purchase is a progressive approach that can optimize design and material selection for durability, efficiency and environmental impact. 'From the client's perspective, conducting product testing offers them the valuable opportunity to experience the device firsthand before making a purchase commitment,' Ricohermoso added. 'It allows them to assess the device's performance, functionalities and suitability for their specific needs without the obligation of buying it outright. Additionally, during the testing phase, clients can engage directly with our knowledgeable team, leveraging their technical expertise to address any questions or concerns they may have. 'This interactive experience fosters better communication and understanding between our team and the clients,' he added. 'Ultimately, seeing the device in action reinforces the clients' belief and confidence in its capabilities, validating the effectiveness of the solution being offered, or simply, 'to see is to believe.'' The company's 645-square-meter (6,942-square-foot) testing facility is centered around a test workshop equipped with product transfer systems from brands that fall under the AHS and Advanced Material Processing (AMP) umbrella, including Cablevey, Spiroflow, Kason and Marion. The test workshop itself accounts for 71% of the total space. According to Ricohermoso, the German test facility was designed to not only enable testing of conveyors and material transfer systems from point A to point B, but to also integrate relevant processing steps including bag conditioning, bulk bag discharging and filling, dewatering, sieving, mixing and drying. 'Additionally, the test facility boasts a cutting-edge, in-house laboratory dedicated to material characterization,' he noted. 'This enables our engineers to gain a deep understanding of the material properties, allowing them to design tailored solutions that meet the specific needs of our customers. The Friedrichsdorf test facility is now up and running and saw its first customer in early May 2023. Ben Ayrton, managing director and vice president of operations and supply chain for AHS and AMP in Europe, noted that the facility is now fully operational and offers more than 50 products for customer trials and testing across all four brands. 'We are immensely proud to have the most comprehensive testing facility in Continental Europe,' Ayrton said. 'Our expansion and future is exciting, as in addition we are looking forward to introducing a brand new 5,500 m square production facility in the UK in the first half of 2024.' The Friedrichsdorf facility will serve multiple AHS and AMP brands for testing, spare parts, European engineering and sales, as well as aftermarket spare parts and maintenance teams. Prioritizing positive client experiences Understanding why clients want to test or compare equipment performance is the No. 1 consideration when developing a test plan. For example, Ricohermoso said one of the main focuses for today's pet food processors is throughput. Once he has a better idea of a client's priorities, Ricohermoso requests a Material Safety Data Sheet (MSDS) to better understand the handing requirements and potential risks related to the product or material in question. He also asks for cleaning, process flow integration, and tolerance information to create a comprehensive test plan for the client. 'If the client's primary objective is to observe the operation without specific test requirements, I take the initiative to design the test plan myself,' Ricohermoso said. 'The clients are then given time to review the plan internally and communicate any concerns they may have. 'By following this streamlined process, we ensure that the test day runs smoothly, with clear communication and alignment between our team and the clients.' Leaning on OEM expertise Cablevey operates in more than 66 countries and has delivered its solutions for the food, pet food, coffee, powder, nut and frozen food industries for over 50 years. Such equipment includes enclosed cable and disc tube conveyors. 'Cablevey provides a gentle conveying solution, making it particularly suitable for products that are sensitive and have low tolerance for breakage,' Ricohermoso said. 'Its unique conveying method ensures that fragile products can be transported without compromising their integrity or quality.' At Cablevey's stateside test facility — which is located in Oskaloosa, Iowa — the company recently launched a 360-degree immersive experience enabling virtual visits in real time. A Zoom-meeting format developed during the COVID-19 pandemic now allows Cablevey to showcase test runs of its machinery in-person and online simultaneously, which provides convenience for those unable to travel or larger work groups, according to the company. Ricohermoso noted the company plans to add this capability to the German test facility over the next few months.
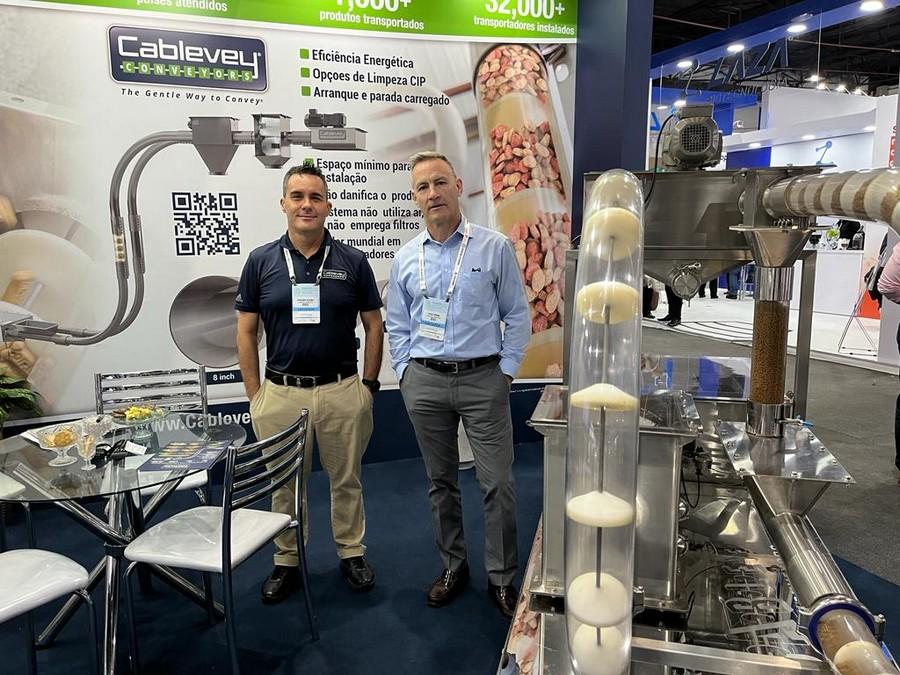
1+ MIN
25/08/2023
Automated Handling Solutions at FENAGRA 2023 in Brazil
Brad very brieflly introuced himself and the Company, the owners of Cablevey Conveyors and Spiroflow, and highlighted its prsence in the pet food sector. Brazil has been a key market for them within the LATAM region, so they have already planned to grow agresively in that market About Automated Handling Solutions AHS combines expertise in specialty conveyor and material handling and automation equipment technologies to help processors manage their lines effectively and efficiently. AHS' products target applications in high value environments and can support both wet and dry media. Primary end markets served include food and beverage, pharmaceutical, nutraceutical, specialty chemical, and high value industrial. AHS is May River Capital's (May River) newest platform company. by All pet Food
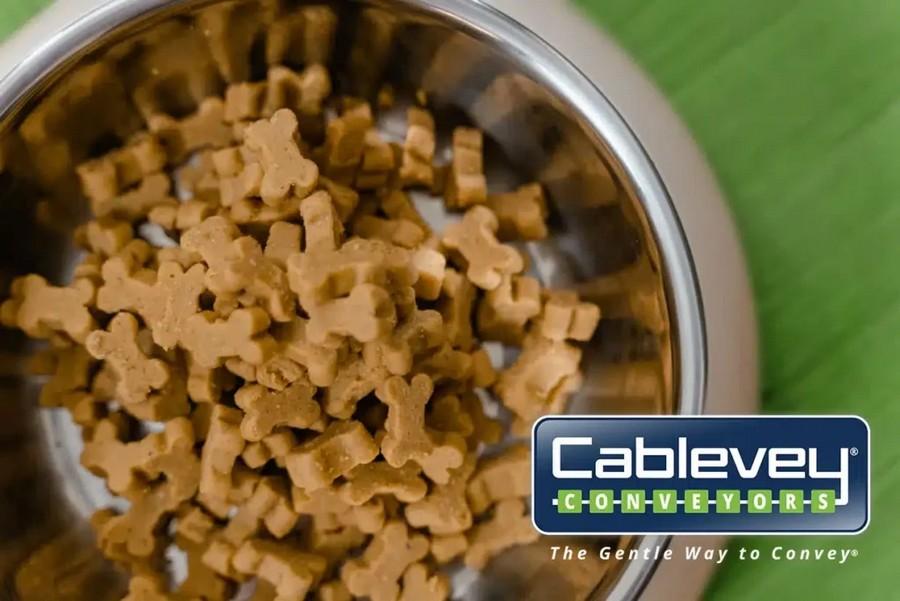
3+ MIN
10/08/2023
Pet Food Industry Trends for 2023
Growth is a great opportunity, but it also requires planning when it comes to how pet foods are conveyed in your facility. How are companies preparing to handle this type of growth at their processing facilities?
In October 2022, Cablevey Conveyors commissioned the independent research firm, Ascend2, to conduct a research study titled Evaluating and Implementing New Conveyor Systems. The 16-page study (download for free) asked 290 food processing professionals in the United States and the United Kingdom to provide their insight on critical considerations when evaluating conveyor systems.
In this article, we will review and analyze the findings from 72 food processing professionals that are conveying pet food. What are they doing to prepare for growth?
Finding #1: Budgeting for Growth.
85% of facilities processing pet foods are increasing their budget for conveying equipment and maintenance in the next 12 months. 35% tell us that they are increasing significantly the budget needed to meet growth opportunities. Why the increase in the budget? The increase is in response to how much these businesses grew in the past year.
Finding #2: Can your workspaces facilitate needed growth?
An important consideration of growth is your workspaces and facility requirements. What conveying systems are best for the space that you have available?
According to the pet food processing experts surveyed, the #1 conveying system (46%) for maximizing available space is cable and disk conveyors. What are a few questions should you ask when evaluating the right conveyor system to optimize the space at your facility?
Do you have enough floor space or ceiling height to accommodate certain conveyor types? Does the layout of the conveying system take into account easy access for cleaning and maintenance, worker safety, and operational performance? Here is a short video that shows a pet food conveying layout.
Finding #3: Consider maintenance and downtime when you plan.
For pet food, what conveying systems are the most efficient? Cable and disc conveyors lead the pack (by a wide margin) at 54%
What are a few questions should you ask when evaluating the right conveyor system when it comes to maintenance and downtime?
Questions to ask:
How much time will be spent disassembling and cleaning the system? Will maintenance and downtime costs exceed any savings that you realized when purchasing the system?
Finding #4: Don't forget energy efficiency.
What contributes to energy efficiency? The size of the motor and the amount of horsepower required to run a conveying system can have a major impact on production costs. What conveying systems is the most energy efficient for pet foods? Cable and disc conveyors are #1 at 44%.
Here are two questions to ask regarding energy and efficiency:
How much energy will this system use?
Is there a high or a low cut-off point at which this system becomes inefficient?
Conclusion
The pet food industry is growing and evolving. This research study provides insight into the specifics of how industry professionals are preparing for that growth and making the best decisions for their facilities.
The research points to cable and disc conveyors as the superior solution for pet foods. Tubular conveyors help streamline pet food processing and maintain both quality and proper proportions in nutritional mixes, snack foods, and other pet food products, product characteristics important to pet food purchasers.
To find out if a Cablevey system is the best solution for conveying your pet food, have the Cablevey Testing Center perform a free test for you. The Testing Center will provide you with the data to help you make the most informed decision for your specific need.
This article only covers a portion of the finding from the Ascend2 research study. Download Evaluating and Implementing New Conveyor Systems for more insight into the food processing industry.
by Cablevey Conveyor

11+ MIN
05/05/2023
Your Go-To Guide For Stainless Steel Conveyors In Food Processing
Automated conveyor systems play a vital role in virtually every stage of food processing, from transporting raw ingredients to packaging finished products. What's more, in the food and beverage industry, hygiene is of the utmost importance. That's why stainless steel conveyors are such a popular choice in this sector (especially for conveying food).
Stainless steel is easy to clean and disinfect, making it the ideal material for conveying foodstuffs in accordance with FDA regulations. In this blog post, we will explore the use of stainless steel construction conveyors in the food production industry in more detail. We'll also look at some of the benefits of using this type of conveyor and explain how you can keep it clean and sanitary
What is stainless steel?
Let's start by taking a closer look at stainless steel. This is an alloy of iron, chromium, and, in some cases, other metals such as nickel and molybdenum. The main feature of stainless steel that makes it so suitable for food handling is its resistance to corrosion. This means that it won't rust when it comes into contact with oxygen. Regular steel (carbon steel), when exposed to oxygen, will transform into iron oxide (rust). Rust is porous and can flake off, becoming an excellent source of contamination. Stainless steel, on the other hand, forms a protective chromium oxide layer on its surface that prevents oxygen from reaching the iron beneath. As a result, it is much more resistant to corrosion than regular steel. What's more, stainless steel is also non-toxic and non-allergenic, which is important when you are conveying food products.
Benefits of stainless steel conveyors
Corrosion resistance is just one of the many benefits of using a stainless steel conveying solution in food processing. Let's take a look at some of the others:
No product contamination – Unlike other materials that degrade over time and release particles into the product, stainless steel is inert and won't contaminate the conveyed material. It is also non-porous, meaning bacteria and other contaminants cannot become trapped on the surface.
Easy to clean and sanitize – Because of its smooth surface, stainless steel is very easy to clean and disinfect. This is essential in the food industry, where hygiene is of paramount importance. We'll get into more detail about cleaning stainless steel conveyor solutions later on.
Doesn't change food flavor – Outgassing is a phenomenon that can occur with certain materials, whereby they release gasses that can change the taste of food. Stainless steel is completely inert and doesn't outgas, so you can be sure your product will not be affected.
Resistant to high temperatures – Stainless steel can withstand high temperatureswithout being damaged. This means it can be used in applications where the product being conveyed is hot.
Resistant to low temperatures – Just as stainless steel can withstand high temperatures, it is also resistant to low temperatures. This means it can be used in applications where the product being conveyed is frozen.
Of course, these are not the only benefits of using a conveyor system for food made from stainless steel. Stainless steel is also a very strong material that is able to support heavy loads, making it ideal for use in the food industry.
Is a stainless steel conveyor sanitary?
To start answering the question of whether stainless steel food processing equipment is sanitary, we first need to understand what the term 'sanitary' means.
In the food industry, the term 'sanitary' refers to an environment or piece of equipment that is free from contaminants such as bacteria, viruses, and other microorganisms. This is different from the term 'clean,' which simply refers to the absence of visible dirt. A piece of equipment can be clean but not sanitary, for example, if it has been cleaned with a cleaning solution that is itself contaminated.
So, are stainless steel conveyors sanitary?
The answer is no – no material is inherently sanitary. However, stainless steel is one of the most hygienic materials that you can use in food handling. This is because it is non-porous and non-absorbent, meaning that bacteria and other contaminants cannot become trapped on the surface. It is also made for easy cleaning and disinfection.
That said, even stainless steel conveyors can become contaminated if they are not used and maintained properly. It is important to remember that bacteria and other microorganisms are everywhere – on our skin, in the air, and even on stainless steel. If left untreated, these contaminants can quickly multiply, compromise food safety, and cause foodborne illnesses.
This is why it is so important to follow good hygiene practices when using stainless steel conveyors. In particular, you should ensure that the conveyor is cleaned and disinfected regularly, even if it is made of a food-grade material.
Cleaning and sanitizing stainless steel conveyors
Each facility has its own cleaning and sanitizing procedures developed according to the products being conveyed and the level of contamination risk. However, there are some basic steps that you can follow in cleaning and sanitizing your stainless steel conveyor:
Remove loose dirt and debris – The first step is to remove any loose dirt and debris from the surface of the conveyor. The reason why it is important to do this first is that you don't want to spread contaminants around when you are cleaning. You can remove loose dirt and debris by brushing, vacuuming, or using compressed air.
Pre-rinse – After you have removed the loose contaminants, you should pre-rinse the conveyor with water. This helps to remove any remaining impurities from the conveyor surface.
Apply cleaning solution – Which cleaning agent you use will depend on the type of contaminants present and the manufacturer's recommendations.
Rinse – Once you have applied the cleaning solution, you should rinse the conveyor with clean water. This helps to remove any remaining cleaning solution and contaminants from the surface.
Inspect – Before sanitizing, you should inspect the conveyor to ensure it is clean. In particular, you should look for any areas that may have been missed during the cleaning process.
Apply sanitizing solution – The final step is to apply a sanitizing solution to the conveyor. This helps to kill any remaining bacteria and other microorganisms. Once you have applied the sanitizing solution, you should rinse the conveyor with clean water.
Note that some sanitizing agents may not need to be rinsed off, so be sure to check the solution manufacturer's instructions.
Increase cleaning efficiency
It's no secret that cleaning, sanitizing, and maintaining conveyors can be time-consuming. In fact, according to our State Of Conveying 2022 report, 54% of food processing managers and engineers said that cleaning and maintenance are the most challenging aspects of conveying. Reasons for this include:
Downtime – When conveyors are taken offline for cleaning, it can lead to significant downtime and lost productivity.
Cleaning frequency – The more often a conveyor is used, the more often it will need to be cleaned. This can make it difficult to keep up with the cleaning times and schedule, especially if the conveyor is in constant use.
Complexity – Some food product handling conveyors are more complex than others, which can make them more difficult to clean. For example, some conveyors have many nooks and crannies that can be difficult to reach.
Fortunately, there are methods you can use to increase the efficiency of your cleaning process. Have you come across clean-in-place (CIP) mechanisms?
Clean-in-place systems
A CIP system is a method of cleaning that uses special equipment to clean the interior surfaces of the conveyor without disassembling it. CIP systems are often used in the food and beverage industry, as they are an effective way to clean complex equipment quickly and efficiently. Cablevey offers two main types of CIP systems:
Dry cleaning – Using brushes, air knives, urethane wiper discs, and special sponges with sanitizers. Dry cleaning is typically used for conveyors that move material that is not wet or sticky.
Wet cleaning – Using water jets, sanitizers, and detergents. Wet cleaning is typically used for conveyors that move wet or sticky material.
In this day and age, where every minute counts towards productivity, a CIP system can make a big difference.
the conveyor type matter?
If you choose a stainless steel conveyor for your food processing plant, does the type of conveyor matter? The answer is yes; of course, it does. The material the conveyor is made of is just one small part of the equation. You also need to consider the environment in which the conveyor will be used and the type of product that will be moved on the conveyor. Here are some common food manufacturing conveyors:
Belt conveyor
Perhaps the most widespread of all conveyors, belt conveyors are generally used to transport light to medium-weight products. A belt conveyor is composed of a belt that rests on two or more pulleys, which in turn rotate on shafts. The pulleys and shafts are powered by an electric motor. The belt on this type of conveyor can be made from a variety of materials. You can get plastic belt conveyors, rubber belt conveyors, and even metal belt conveyors. Not all of these represent a food-grade conveyor, though. Benefits:
Good for fragile materials
Can transport a variety of products
Drawbacks:
Not for steep inclines or vertical conveying
Not for wet or sticky products
If not enclosed, it poses a high risk of contamination
Bucket conveyor
Bucket conveyors, or bucket elevators, are composed of a series of buckets that are connected to a belt or chain. The buckets lift materials, such as grain, up to the top of the conveyor, where they are discharged into a chute. Even though horizontal bucket conveyors exist, incline conveyor options are more common, as they take up less space and can be used in a variety of settings.
Benefits:
Low driving power – energy efficient
Good for facilities with small floor plans
Good for inclines and vertical conveying
Drawbacks:
Ridiculously difficult to clean and maintain because of a lot of moving parts
Pneumatic conveyor
The main principle of material conveying in pneumatic conveyors is entrainment. In this type of conveyor, air is used to move materials through a system of tubes. A blower or a vacuum pump can generate the airflow.
Benefits:
High conveying speeds
Low preventative maintenance and cleaning costs
Flexible design – suitable for a variety of settings
Drawbacks:
Extremely hard on conveyed materials – material damage is common
It requires a lot of power to control the speed
Can be noisy
Tubular chain conveyor
A tubular chain conveyor is composed of a chain that runs inside a tube. Circular discs are evenly spaced along this chain, creating space between them for the conveyed material to fit into. The discs move along the tube, propelling the material forward.
Benefits:
Fully enclosed
Can be used for inclines and vertical conveying
Gentle conveying
Drawbacks:
Chain is in direct contact with conveyed material – high risk of contamination
Difficult to clean and maintain
Tubular cable and disc conveyor
We saved the best for last. For specific material types, such as breakfast cereal, snack foods, nuts, beans, coffee beans, rice, and similar, tubular cable and disc conveyors are the best option. These conveyors work on a similar principle as tubular chain conveyors, with one major difference – instead of chains and discs, they use cables and discs. There is no direct food contact with the cable, which decreases the risk of contamination. Also, these conveyors are easier to clean and maintain.
Benefits:
Fully enclosed
Gentle conveying – suitable for fragile materials
Extremely low risk of contamination
Easy to clean and maintain
Drawbacks:
Not for viscous or sticky materials
Which conveyor to choose?
A stainless steel conveyor system is only as good as the application it's being used for. Different conveyors are better suited for different tasks. To help you make a better decision, here are the top considerations you need to take into account:
Conveyor type – As we've seen, there are many different types of conveyors. Make sure to choose the one that's best suited to your needs.
Material type – Not all materials can be conveyed by all conveyors. Some materials are too fragile, while others are too dense. Make sure that the conveyor you choose can handle your material.
Conveyor throughput – The amount of material that needs to be conveyed will play a big role in deciding which type of food processing conveyor to choose.
Conveyor size and layout – Not every conveyor is suitable for every facility. The size of your facility and the layout of your production line will play a big role in deciding which conveyor to choose.
Some other considerations are the cost of the conveyor, the energy efficiency, and how easy or difficult it is to clean and maintain the conveyor.
Go for a sanitary design
We've already explained how no material is completely safe from contamination. Even if you choose a food conveyor system that's easy to clean, there's always a risk of bacteria and other germs getting into the food. That's why it's important to go for a sanitary conveyor design. A hygienic design minimizes the risk of contamination. It includes:
Easy access for cleaning – The conveyor should be designed in a way that allows easy access for cleaning. All parts of the conveyor should be accessible for cleaning, and there should be no dead spots where bacteria can accumulate.
No traps in the conveyor frame – The conveyor frame design has to prevent food from getting trapped in it. All food should be able to fall freely from the conveyor, without getting caught in any nooks or crannies.
No areas where water can accumulate – The conveyor should be designed to prevent water from accumulating anywhere on it. All wet areas should drain quickly, and there should be no places where water can pool.
No fasteners – Welds should be used instead of fasteners to prevent food from getting trapped in them.
It stands to reason that deciding exactly which type of stainless steel conveyor to choose for your food processing facility is a big decision. But with the right information, you can make the best choice for your needs.
Conclusion
Here are the main takeaways from this article:
Stainless steel isn't sanitary by default. But it is an excellent material for conveyors because it's easy to clean and doesn't rust.
The cable and disc conveyor is the best type of stainless steel conveyor for food processing applications. These food conveyors are fully enclosed, gentle, and have a low risk of contamination.
When choosing an industrial conveyor, consider the type of conveyor, the material you're conveying, the throughput, the size and layout of your facility, and the cost.
Make sure to choose a conveyor with a sanitary design to minimize the risk of contamination. A sanitary design includes easy access for cleaning, no traps in the conveyor frame, no areas where water can accumulate, and no fasteners.
Ready to buy a stainless steel conveyor for your food processing facility? Cablevey Conveyor can help you find the perfect one for your needs. Contact Cablevey today to get started
By Cablevey Conveyor
Source: All Pet Food
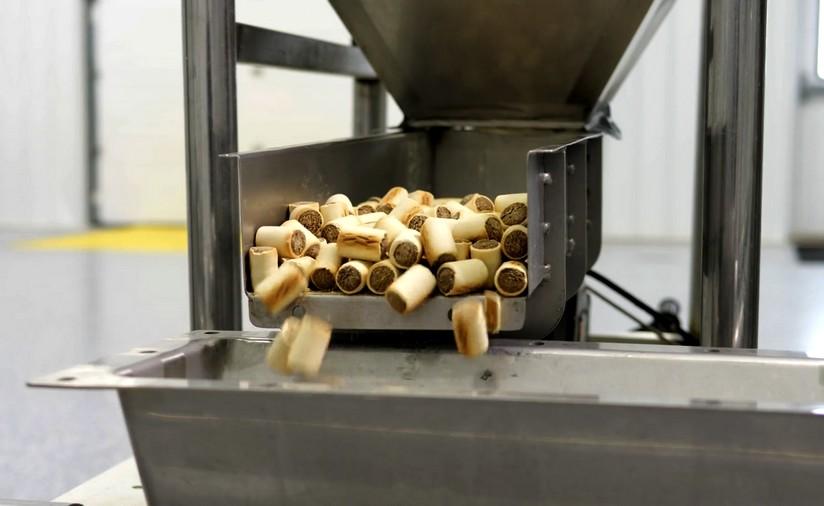
5+ MIN
19/04/2023
Pet Food Processors 'Test Drive' Conveyors at World-Class Facility
Even when people love the look of a car or SUV, most would not complete a purchase before a test drive to confirm how the vehicle performs on the road. Similarly, today an increasing number of pet food processors are realizing the importance of 'test driving' conveyor equipment at OEM test facilities, which use their actual product to ensure the equipment meets processor quality, flow, and cleaning requirements before they make the purchase.
In response, some OEMs have invested in state-of-the-art test facilities that allow pet food processors to run product on the same type of equipment they are considering for purchase, while benefitting from expert consultation to optimize their process.
'We encourage pet food processors to test their products [at our facility] and observe the results to ensure it meets their needs. They can ask questions in real time. They can test for fines or degradation. They can see for themselves how the product flows in the conveyor and how easy it is to clean,' says Larry Van Zee, Executive VP, retired at Cablevey Conveyors, a mechanical conveyor manufacturer that serves the pet food, specialty food, coffee, powder, nut, and frozen food markets. In more than 66 countries, the company has designed, engineered, and serviced enclosed cable and disc tube conveyors for over 50 years.
At its full-service product test center in Oskaloosa, Iowa, the OEM has tested more than 1,900 products, including pet food, beans, rice, grains, cereals, coffee, chocolate, and caramel corn peanut snacks, for some of the largest global brands. All products are run through a tubular disc and cable conveying system to observe the effects and fine-tune the results.
According to Scott Berning, Cablevey's Product Testing Manager, there are multiple reasons pet food processors decide to visit the test center. 'Customers may have products that we know will run well on tubular cable conveyors, but they want to see it in operation with their own eyes,' says Berning. 'They want to ensure the product will run properly, and their quality department typically checks as part of their due diligence before purchasing equipment.'
Berning adds that when Cablevey's applications department designs and quotes a conveyor and the manufacturer lacks sufficient experience conveying a specific product, the email quote states it is 'pending successful product testing.'
Some pet food processors want to evaluate tubular cable conveyors against other conveying options they may also be considering, such as bucket elevators or chain conveyors. Others are already familiar with tubular cable conveyors based on experience and want to show their managers that a similar solution could be implemented at their current facility.
Once the pet food processor is at the site, Cablevey product specialists and engineers typically consult with the customer to determine their specific goals and issues to be resolved. From this, they can proceed to design a conveyor with a set of features that addresses specific challenges.
'Our technicians and engineers can diagnose and prescribe a solution whether the concern is breakage, temperature, stickiness, abrasiveness or other issues,' says Berning. He notes that when pet food processors test products at the facility, they are provided full documentation of the results, including a detailed report with video and recommendations.
According to Berning, testing for product fragility and damage is usually the primary concern of processors. 'No matter the product, pet food processors want to keep their product intact and avoid damage during conveying,' says Berning.
He points out that tubular drag cable conveyors excel at reducing product damage since the units gently move product through a sealed tube using a coated, flexible stainless-steel drag cable pulled through on a loop. Solid circular discs (flights) are attached to the cable, which push the product through the tube without the use of air. These conveyors can transport delicate, precise blends for a wide variety of food types, and up to 2000 cubic feet per hour of materials in versatile layouts and configurations.
Still, quality assurance checks can be essential for processors, even those transporting products that seem hard to damage.Reducing product loss and maintenance is also important to pet food processors.
'Processors want to place their material in an inlet and then have all of it emerge from the discharge with minimal losses,' he says. Since tubular cable conveyors are sealed from end-to-end with product traveling one way in enclosed tubes, there is essentially no product loss and no issue with carry-back.'
Ease of cleaning the conveyor is also a top priority of pet food processors. Surprisingly, many processors visit the facility to witness how easily the conveyor can be cleaned. 'People come here from across the United States just to watch me perform a conveyor wet-clean and washdown even though it is something I have to do every day,' says Berning.
Traditional alternatives like screw conveyors can be difficult to clean and require time-consuming disassembly, as well as some heavy lifting after each product changeover. 'One processor told me that it took six of his technicians about eight hours to clean their screw conveyor system. They had to pull a big auger out of the screw conveyor, which was dangerous to handle,' says Berning.
Tubular drag cable conveyor systems offer easier, safer options for dry and wet tube conveyor cleaning. Equipment such as brush boxes, urethane wipers, air knives, inline sponges, and inline bristle brushes can facilitate multi-step, essentially automated Clean-In-Place (CIP) wet cleaning.
The wet cleaning process internally cleans the cable conveyor tube in several steps, starting with a water rinse followed by foaming agent, a sanitizing rinse, and a final water rinse. Once the system is thoroughly flushed out, drying is achieved by attaching urethane wipers to the tubular conveyor's discs, which 'act like a squeegee' to remove any residual water.
For those unable to visit the test facility in person, Cablevey now offers the ability to view and respond to product testing live in a 'virtual visit' with a link to real-time video and a Zoom meeting type format - an option developed during the COVID-19 pandemic. With this technology, the tubular cable conveyor manufacturer can host both in-person and virtual visits simultaneously, which is helpful when larger work groups such as quality assurance teams have an interest in evaluating the conveyor.
'In one recent product test, a team of four visited our facility in person while twelve others watched virtually,' says Berning.For those who wish to experience the world-class facility in greater detail, Cablevey has created a 360-degree immersive virtual tour of its product test center (https://cablevey.com/test-your-product/).
Embedded within the virtual reality (VR) experience is product information as well as videos. The video library demonstrates how tubular cable conveyors transport different materials such as pet food, coffee beans, grains, bird seed, tea leaves and breakfast cereals. How-to videos illustrate potential layouts, components, technologies, cleaning, and maintenance options.
With easily accessible, advanced product testing facilities, pet food processors can view and verify in real-time that their investment in new conveying equipment will meet their requirements. Processors who 'test drive' their product in this way will not only enhance their product quality and productivity, but also experience a significant advantage over competitors.
By Del Williams -Technical writer based in Torrance, California. - Cablevey Conveyor
All Pet Food
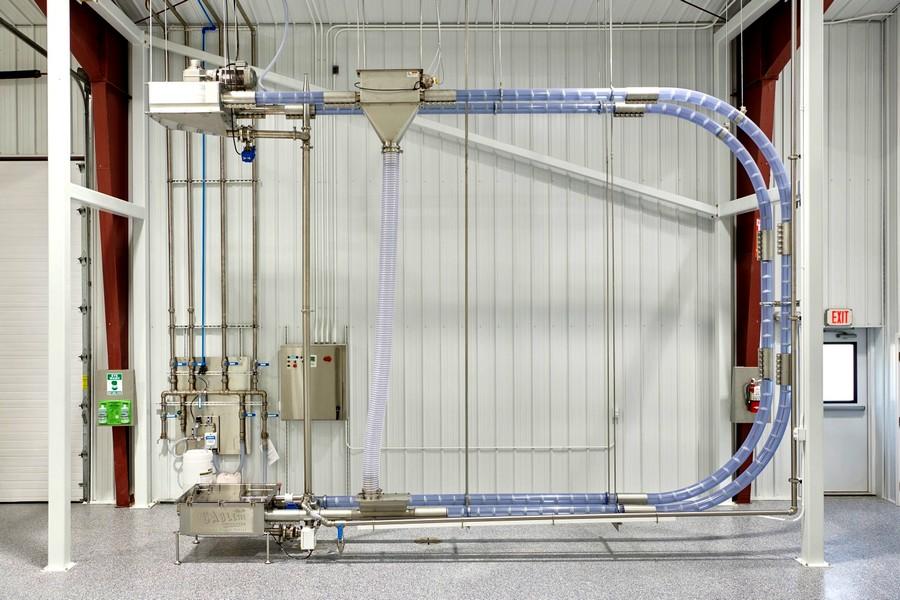
6+ MIN
24/01/2023
Boost Profit with Gentle Conveying Without Air
To convey such delicate food product, processors should avoid conveyors that may force the fragile material through stressful phases during transport that could impact its integrity, while still meeting high throughput requirements. Given this need, some food processors are reconsidering conveying fragile, high-value products using high-velocity air power through tubes, bends, or sweeps before it is unceremoniously dumped into bins or containers.
In the coffee industry, for example, processors go to great expense to roast whole beans. However, the beans can be damaged by high-velocity air conveyance, compromising flavor and aroma, according to Gary Schliebs, a Process Engineer and Director of Plus One Percent…Engineered Solutions, a consulting firm that works in the food industry and markets food industry conveyor equipment globally.
When a whole macadamia nut is broken, its value can drop by half. Instead of a premium price for whole nuts, damaged nuts are often sold at a substantial discount, and often crushed for use in cooking or processing further upstream in the food industry.
'Many high-value food products can be fragile and need very gentle handling. Otherwise, whole forms can be broken, crushed to bits, and even turned to powder. This significantly lowers the value of the product, and damaged portions may need to be removed or disposed of to prevent perceived quality issues that could prompt customers to turn to other brands,' says Schliebs.
'In some cases, more than 10% of delicate product can be damaged by high-velocity air-power systems. The cost to the industry is compounded because the damage often comes at the end of the process, after considerable value has been added, only to have it degraded by a poor choice in the selection of transfer conveying equipment,' adds Schliebs, who frequently consults on food engineering equipment design, plant layouts, and process flows.
The Limitations of Air Conveyors
A wide range of fragile, high-dollar-value food products can be prone to excess breakage when conveyed at high velocity by airpower, such as in pneumatic and aeromechanical systems.
Pneumatic conveyor systems utilize air by creating air pressure above or below the atmospheric level. These systems use filters that require regular replacement. The two main types of pneumatic conveyors – dilute phase and dense phase – differ by speed and pressure, and both can be configured as a pressure or vacuum system.
In dilute phase conveying, the food product is suspended in the air as it is transported through the conveying pipe at extremely high velocities of typically 3,400-5,000ft/min. While the product usually has minimal breakage during straight pathways, most systems have bends and sweeps where it can be forced through constricted areas, quickly change direction and be damaged. In such cases, high-dollar value food often can be too fragile.
Dense phase pneumatic conveyor systems, where the product is not suspended in air since it is heavy or abrasive, function at lower velocity than dilute phase. However, with air speeds of about 700-1,500ft/min., delicate food items are still susceptible to breakage at bends and sweeps.
While aeromechanical conveyors have a different method of conveyance, these enclosed, high-capacity mechanical systems can also degrade delicate product. With these systems, a wire rope with evenly spaced discs within a tube travels at high speed, running in sprockets at each end of the conveyor. This generates an internal air stream traveling at the same high velocity as the discs that carry product along in the tube. However, these conveyors may also force vulnerable materials through stressful phases during transport, which could impair their integrity.
'Any fragile or friable food product conveyed at high velocity is prone to damage, particularly if it changes direction or exits with impact. This can be the case with both pneumatic or aeromechanical conveyors,' says Schliebs.
A Gentler Approach Boosts Profitability
According to Schliebs, a gentler alternative to protect sensitive, high-value food products is to utilize tubular cable conveyors. These systems move product through a sealed tube using a coated, flexible stainless-steel drag cable pulled through on a loop. Solid circular discs (flights) are attached to the cable, which push the product at low speed through the tube without the use of air, preserving product integrity and minimizing waste.
'Food industry manufacturers can decrease product damage down to 1-2% with a slower process like a Cablevey Conveyors tubular cable system. With it, the product is gently transferred at low speed, so there is minimal to no damage,' says Schliebs.
Cablevey Conveyors is an Oskaloosa, Iowa-based premium, specialty material moving, mechanical conveyor company that has designed, engineered, and serviced enclosed cable and disc tube conveyors for almost 50 years, and is in more than 66 countries.
In the food industry, the conveyors are utilized for products such as nuts, cereal, coffee, snacks, pet food, beans, and seeds. The systems can convey up to 2000 cubic feet per hour (56m3/hr.) of flakes, pellets, shavings, crumbles, granules, regrind, chunks, parts, prills, and powders with numerous layouts using multiple inlets and outlets.
Since the material is carried between the flights, it is also much easier to safely convey some sticky or easily compacted materials in a tubular cable conveyor than in air-powered conveying systems, where such materials can form plugs.
'With pneumatic or aero-mechanical conveying systems, any soft or sticky material, like dried fruit, can smear and adhere to surfaces, particularly at bends and sweeps that change direction, which is not an issue with tubular cable conveyors,' says Schliebs. According to him the tubular cable conveyor's modular construction can also help reduce product damage by enabling it to slide out on a gentler gradient, rather than simply drop out, as is more typical with conveyors utilizing air.
'To minimize product damage, it is important for food industry manufacturers to not only transfer gently, but also get product in and out of the conveyor safely and gently as well. That is more achievable with a conveyor like Cablevey that allows product to slide down rather than drop out the end,' says Schliebs.
In fact, most tubular cable conveyors have interchangeable components that allow the conveyor to be easily expanded or reconfigured to change the length, conveying path and the number of inlets and outlets. These modifications are more complex and time-consuming with a pneumatic conveying system because it has more components and electrical connections
Also, another bonus of the Cablevey systems is that the 'footprint' can be quite small compared to other conveyor systems, and that really helps with tight and compact manufacturing areas.
'Because of the 'bespoke' design of each Cablevey system for customer specific requirements, we can tailor the design to be very 'non- intrusive' in the work area and not hinder access for people and maintenance, as other systems can. This is a real bonus for safety, access and saving floor space, which is another cost to manufacturing,' said Schliebs.
Less energy use, less noise
Since pneumatic systems convey product at high velocity, this typically requires larger, power-hungry motors that run fans, blowers and rotary valves. In a dense phase system, a pressure tank requiring compressed air consumes additional power. In terms of noise level, pneumatic conveying systems also generate considerable noise. Aero-mechanical systems, running at high speed, generate considerable motor and disc noise as well.
Given that smaller motors are used, tubular cable systems are quieter overall and utilize much less energy. 'A low-speed tubular cable system is quiet enough to easily have a conversation around it while it is running,' says Schliebs. 'In regards to energy, it utilizes about one-tenth that of pneumatic systems. For dense phase models, the electricity savings by using a tubular conveyor can be sizeable, with 1-year ROI in some cases.'
by Cablevey Conveyor
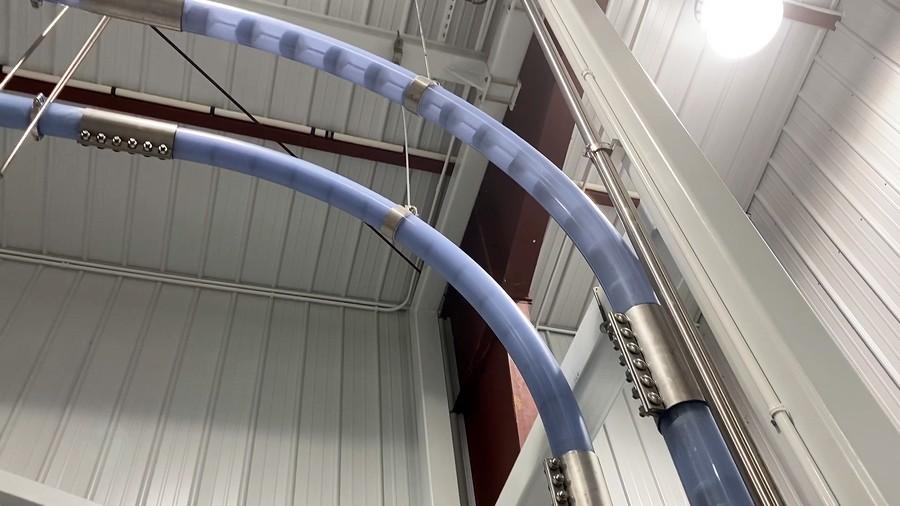
5+ MIN
26/12/2022
Protect Against Pet Food Recalls with the Right Conveyor System
With the threat of contamination from harmful pathogens such as salmonella, listeria, and E. coli a continual concern, pet food processors are seeking to protect not only the public but also their companies' bottom lines from the massive costs, reputational damage, and greater regulatory scrutiny associated with recalls. The goal is a safe, clean, sanitized working environment. According to the FDA's Food Safety Modernization Act (FSMA) Final Rule for Preventive Controls for Animal Food, 'Every facility that produces animal food with a hazard requiring a preventive control must have a recall plan.' (https://www.fda.gov/food/food-safety-modernization-act-fsma/fsma-final-rule-preventive-controls-animal-food). The FSMA Final Rule for Preventive Controls for Animal Food has various key requirements. Among these, covered facilities must establish and implement a food safety system that includes an analysis of hazards and, if necessary, risk-based preventive controls. The rule sets requirements for a written food safety plan that includes details about the facility's hazard analysis and resulting preventive controls. Given the increasing number of outbreaks and recalls traced to post-processing contamination of foods, it is no surprise that the Preventive Controls Rule requires manufacturers to implement a food safety plan with the goal of preventing sanitation deficiencies. The rule covers sanitation practices for food-contact surfaces, preventing microbial and chemical cross-contamination, and monitoring potential environmental pathogens for critical equipment like conveyors. As a result, quality assurance teams are paying more attention to the type and design of conveyance systems used to help meet pet food safety standards. This includes identifying potential harborage points where debris and pathogens can collect, as well as implementing best practices to save on costs to clean equipment, perform regular testing, and maintain the environment. 'Every day we are asked for recommendations about the sanitary design of equipment,' says Justin Kerr, founder of Factor IV Solutions, LLC, a food safety consulting firm that has worked with hundreds of food processors and harvesting operations throughout North America. 'With conveyors, ideally there should be minimal harborage points, they should protect products from the environment, and be easy to clean.' Kerr says Factor IV Solutions assists food processors to develop Sanitation SOPs (SSOP: Sanitation Standard Operating Procedures) related to conveyors that include regular verification testing of food contact and non-food contact surfaces. However, given the risks of contamination, the potential for recalls, and the additional costs associated with regular cleaning and testing, it's advisable to select a conveyor that eliminates many of the potential risk factors. Selecting a Conveyor System In the pet food processing industry, open conveyor systems like bucket elevators and belt conveyors can be more vulnerable to contamination. With open systems, products can be exposed to pathogens, contaminants, or moisture in the surrounding environment. Product can also spill onto the plant floor and make its way into drains. Consequently, processors that use such conveyors must maintain strict environmental controls including constant swabbing, testing, and quality assurance. Closed conveyor systems, on the other hand, effectively seal off products from the outside environment. Even then, it is still necessary to control the environment. Although there are several types of closed systems, one popular example when conveying high-value foods is tubular drag cable conveyors. These systems gently move products that are prone to breaking or crumbling through a sealed tube using a coated, flexible stainless-steel drag cable pulled through on a loop. Solid circular discs (flights) are attached to the cable, which push the product through the tube without using air. The coated cable ensures that no debris accumulates within the strands of the cable, as the cable is totally sealed. 'An enclosed conveyor like the Cablevey provides a controlled environment that reduces the risk of exposure to contaminants and pathogens from outside the system when properly maintained,' says Kerr. 'Because it is closed, it is less susceptible to aerosols and over spray from adjacent lines.' Oskaloosa, Iowa based-Cablevey Conveyors is a specialty conveyor company that has designed, engineered, and serviced enclosed cable and disc tube conveyors for over 50 years, with installations in over 65 countries. The company's product can be as small as powdered material or as large as whole potatoes, and is increasingly used to convey pet food, coffee, cereal, nuts, produce, and specialty foods. 'When we conducted trials and verification testing, we found that tubular cable conveyors maintain greater repeatability cleanliness over a longer period of time than open systems due to the controlled environment within the enclosure,' says Kerr. Additionally, Kerr notes that closed conveyors significantly reduce potential harborage points for contamination. 'Tubular drag cable conveyors are very simple in construction, without standard joints, threaded bolts, and plastic-to-metal connections,' says Kerr. Superior Cleaning Kerr points out another advantage: the enclosed conveyors also enable a 'wet cleaning' process without wetting the surrounding areas, in which the systems can be quickly and effectively flooded with water and sanitized without disassembly. While not all pet food processing materials are suited to wet cleaning, such as hygroscopic materials that readily absorb and retain moisture, the process minimizes potential contamination for other types of food. The wet cleaning procedure begins with a water rinse followed by foaming agent, a sanitizing rinse, and a final water rinse. Once the system is thoroughly flushed out, drying is achieved by attaching urethane wipers to the tubular conveyor's discs, which act like a 'squeegee' to remove any residual water. 'Within the tubular system, all wash factors can be repeatably controlled – water chemistry, temperature, physical action, and time – so every surface is equally cleaned,' says Kerr. He notes that clear tubes are available that offer the additional benefit of visual inspection or verification. Since a complete and thorough cleaning can be accomplished without disassembly of the system, the entire process only takes 20-90 minutes, depending upon the layout, product, and desired level of cleanliness. This can substantially reduce disruptions and downtime during production changeovers and eliminate the need for additional dedicated conveyor lines. Regular cleaning can be automated through the plant's distributed control system. 'A benefit of Cablevey is the repeatability and verification of surfaces cleaned and the ease of maintaining them,' says Kerr. 'You can do verifications against cleanliness and hold [the cleanliness] over a greater period of time.' When a pet food processor wants to ensure that a conveyor will meet its sanitation requirements, equipment suppliers like Cablevey often allow quality assurance teams to perform tests prior to purchase. 'Sometimes customers come to our test lab so they can run product and conduct swab tests before and after wet cleaning and review the results for themselves,' says Morgan Bailey, Communication Specialist at Cablevey Conveyors. In the pet food processing industry, the stakes are high when it comes to preventing safety issues. With the threat of contamination from harmful pathogens always a concern, processors are seeking to protect both the public and their companies' bottom lines from the massive costs associated with recalls. As a result, quality assurance teams are analyzing the type and design of conveyance systems more closely. Enclosed conveyors that are capable of automated wet cleaning can help mitigate risk and prevent many safety issues. These conveyors provide an extra level of protection by keeping debris and pathogens from collecting. They also save on costs by eliminating the need for manual cleaning. As processors continue to seek ways to improve safety, enclosed conveyors will become an increasingly popular choice. by: Del Williams, Cablevey Conveyors All Pet Food
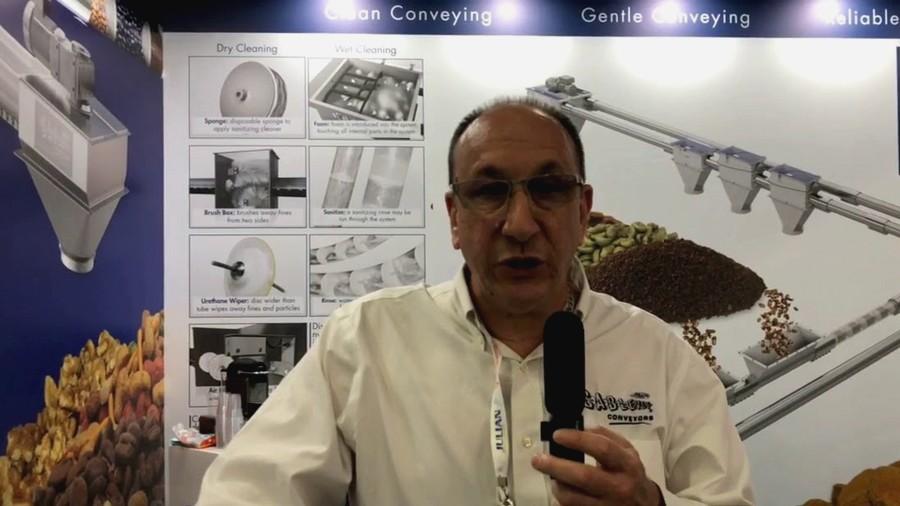
3+ MIN
10/08/2022
Q&A with Karl Seidel, Marketing Director of Cablevey Conveyors
The findings reveal there is a high level of automation in food processing, with most companies operating multiple conveyor lines, yet mixed satisfaction related to the diverse types of conveyor operating systems:
We sat down with Karl Seidel, Marketing Director at Cablevey to ask about the survey results.
What was the goal of this survey?
Basically, we were seeking to discover what is working and what is not. Where can conveying technology improve and what else can we be doing to help companies achieve their goals and be successful?
How many people participated in the survey?
We reached more than 200 professionals within the food and processing industries including production managers, engineers, and executive managers. They represented multiple product categories including snacks (55%), frozen foods (42%), breakfast cereal (32%), nuts (31%) and coffee (30%), followed by other product types such as pet foods, seeds, beans, specialty grains, hemp and powders.
Were there any surprises?
Our service technicians and consulting engineers deal with food processing firms on a daily basis, paying plant visits or conducting tests. We were aware that the vast majority, 83% of companies surveyed, have installed multiple conveyor lines within their facilities. A fourth of respondents operate more than 25 conveyor systems across business units, so the industry is highly automated.
What stood out in this report was the fact that energy consumption and maintenance issues were cited as the main drivers for conveyor selection and purchase decisions, not throughput, as you might imagine or even the initial purchase price of the system.
Why these two features in particular?
I believe these responses illustrate the critical thinking and long-range planning by plant managers and operators. As energy costs continue to increase and as companies strive to meet sustainability goals, energy consumption becomes a more critical factor in the long term. And labor shortages mean everyone is working a bit leaner. Lengthy or complex cleaning processes not only cause significant downtime, but they can also require a lot of labor. A conveyor system that is easy to clean and maintain helps save time and improves efficiency. In fact, 56% of survey respondents reported maintenance issues as the top reason for installing updated conveying systems.
If maintenance issues were a chief source of dissatisfaction, what was the greatest source of user satisfaction?
Many respondents tied user satisfaction to material damage, a critical challenge for those in the food industry for several reasons. Material damage is tied to product quality and appearance, as well as waste, and wasted products directly impact profitability and sustainability both. Relative motion and 'free fall' tended to introduce the greatest levels of material damage. Companies can reduce or minimize breakage by following best practices for conveying fragile materials. Cable/disc conveying was reported as the top choice to preserve product integrity for fragile materials.
Beyond maintenance and energy consumption, what were major factors related to conveying that concerned survey respondents?
After energy consumption, cleaning, and maintenance, other key considerations included product specifications, layout and available space, facility requirements, product volume or throughput, dust, and the noise level of the machine.
Outside of conveying, what are some of the pressing concerns in the industry?
We had 53% of respondents identifying supply chain issues as the most pressing industry challenge. And related to this, 39% cited product shortages as another major issue. On the upside, the industry is growing. Ninety-one percent of respondents reported business growth in the past year. Automation and particularly, the efficacy of the conveying system has a significant impact on an organization's bottom line.
A substantial portion or 40% of survey respondents who reported being 'extremely satisfied' with their conveying systems experienced growth of over 20% last year. While only 13% of those less satisfied or unsatisfied with their current conveying system experienced that same growth.
Who is more likely to make a change then? The dissatisfied customer?
Actually, an overwhelming majority of all respondents (86%) evaluate their conveying systems at a minimum, every six months. And those most satisfied with their conveying systems are most aggressive with their evaluation timetable, with 46% evaluating their systems every month. Increasing the frequency of your evaluation process can be a key factor to maintaining peak performance.
And collaboration is key. These evaluations should and often do involve in-house engineers, outside consultants, maintenance personnel, and local equipment representatives. There is a lot of insight to be gained by copying those following best practices and experiencing the greatest degree of success.
Source: Cabevey Conveyor
By All Pet Food
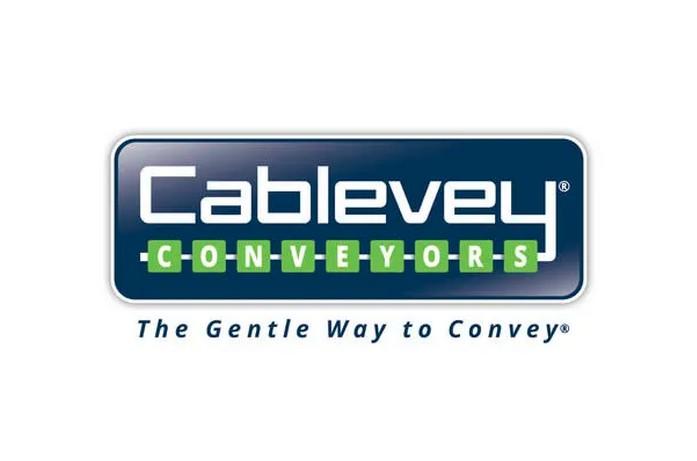
1+ MIN
02/08/2022
Cablevey® Conveyors Announces New Logo and Website
Celebrating 50 Years of Serving Its Customers For the past 50 years, Cablevey Conveyors has been moving leading brands forward with best-in-class conveyor technologies. This moment is a celebration of the past and a promise to the future as it looks forward to the next generation of technology, and the people who will guide it. "Cablevey has much to celebrate about its first 50 years with many notable achievements," said Brad Sterner, CEO. "The company has created groundbreaking conveying technology, installed tens of thousands of systems in 66 countries around the world, and created a great company for our employees and community in Oskaloosa to be proud of." "As we prepare for the next 50 years, it's the perfect time to launch our new brand, new website, and a new commitment to build on the successes we've had together in creating systems known for product integrity, energy efficiency and low total cost of ownership," he said. About Cablevey® Conveyors Cablevey Conveyors is a global specialty conveyor manufacturer that designs, engineers, assembles, and services tubular drag cable and disc conveyor systems. With customers in over 65 countries, the company specializes in moving materials for food/beverage and industrial powder processors that seek food-grade conveying performance with clean, fast, energy-efficient, and cost-effective systems. Learn more at www.cablevey.com Source: BusinessWire by All Pet Food
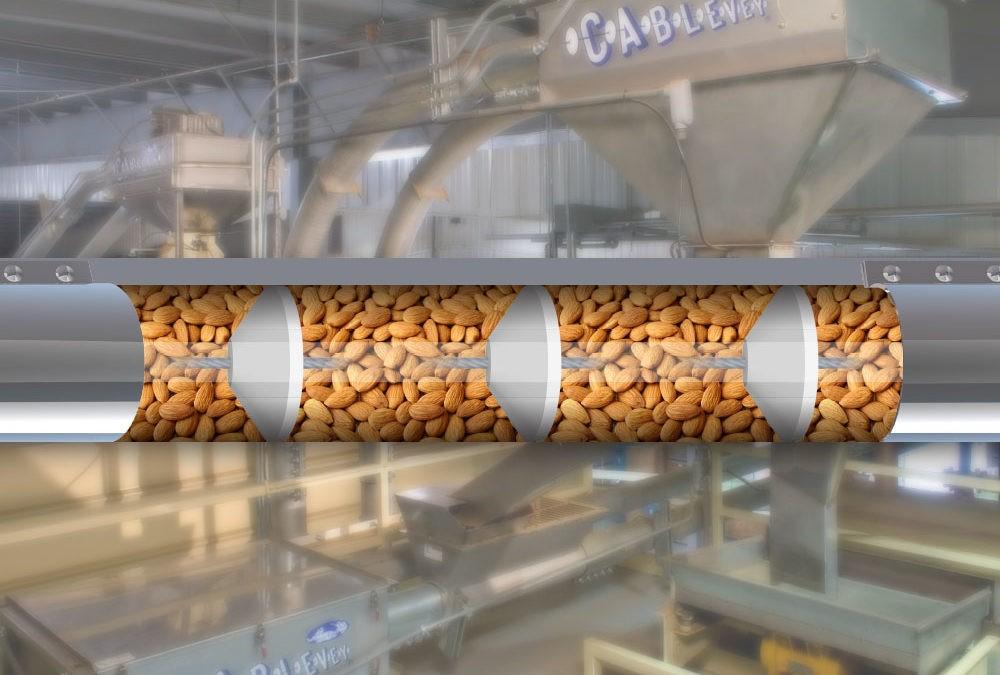
6+ MIN
26/07/2022
Pet Food Processors: Tubular Drag Conveyors Double the Volume
Pet food processors have long sought a safer, more energy-efficient means to convey product with less spillage, breakage, or downtime due to necessary cleaning and maintenance. Although tubular drag conveyors have offered these desired attributes compared to belt, bucket, or pneumatic systems, many in the industry selected these traditional options to move higher volumes or larger-sized products.
Now, however, 8' diameter tubular drag conveyors have become widely available that essentially double the volumes of smaller 6' units. This provides comparable volumes and pricing to conventional industrial systems and enables the transport of much larger product sizes than previously possible.
Tubular drag cable conveyors gently move product through a sealed tube using a coated, flexible stainless-steel drag cable pulled through on a loop. Solid circular discs (flights) are attached to the cable, which push the product through the tube without the use of air. These conveyors excel in transporting delicate, precise blends for a wide variety of food types in versatile layouts and configurations.
'Today, 8' tubular drag cable conveyors can move up to 2,000 Ft³ and 80,000 pounds per hour depending on the bulk density of materials. The units can transport product as large as whole potatoes and midsized grapefruit, and are increasingly used to convey pet food, cereal, nuts, and whole fruit,' says Clint Hudson, Engineering Manager at Cablevey Conveyors, a mechanical conveyor manufacturer that serves the pet food, specialty food, coffee, nut, powder, and produce markets.
Optimizing Food Processing
According to Bob Owen, Director of Product Performance at Cablevey, the primary reasons why industry professionals are turning to the higher volume tubular drag cable conveyors include improved power use, safety, product preservation, product quality, and production uptime.
1. Power Consumption
As energy prices continue to rise, pet food processors are paying more attention to reducing the power required to convey materials. Within plants, the motors needed to convey large volumes of food materials can vary greatly in power consumption. At the high end are pneumatic conveyors that utilize air to move product at high velocity through an enclosed line by creating air pressure above or below the atmospheric level. High-volume pneumatic conveyors generally require larger, power-hungry motors up to 20-50 HP or more that run fans, blowers, and rotary valves.
At the mid-range of power consumption are belt conveyors and bucket elevators. In a typical conveyor belt system, a belt forms a closed loop and stretches across two or more pulleys with a drive pulley that enables it to rotate continually. Bucket elevators move material using buckets attached to a rotating belt or chain. The buckets pick up material, move it to an endpoint, discharge material, and return to the starting point to pick up a new load. To convey a similar, high-volume amount of material, belt conveyors and bucket elevators would typically utilize approximately 25 HP motors, says Owen.
At the low end of power consumption are 8' tubular drag cable conveyors, which would usually use a 7.5 HP motor to move a comparable, voluminous amount of material.
'The drag cable pulls the solid circular discs (flights) attached to the cable at low speed through a loop, which requires less energy than conventional methods. The ample size and number of the discs on 8' units enable conveying a similar amount of material as traditional belt, bucket, or pneumatic units,' says Owen.
2. Safety
Open systems such as bucket elevators and belt conveyors are common in the pet food industry but have substantial drawbacks in terms of the potential for contamination. With either type of system, any product that is left uncovered can potentially expose it to contaminants and moisture in the surrounding environment. Open systems also allow product spillage onto the plant floor, which can present a slip and fall hazard if not promptly addressed.
Unlike open systems, closed systems like tubular drag cable conveyors and pneumatic units effectively seal off product from the outside environment and any potential contamination from that source. The enclosed nature of the systems ensures no dust escapes that could lead to an unsanitary and potentially dangerous coating of dust on the floor or process equipment. The result is a safer, cleaner, dust-free work environment and reduced risk of dust explosions if the product is in powdered form.
The enclosed systems also eliminate the inherent risk of slip and fall incidents due to product discharge onto the processing area floor.
3. Product Preservation
Enclosed conveyors prevent the product loss intrinsic to open systems such as belt or bucket utilizing units. Once food product is in the enclosed tube, it cannot fall out, and no powdered product is lost in the form of escaped dust. Preventing product loss can offer considerable benefits to the food processor's profitability with surprisingly quick ROI in some cases.
In the example of an international pet food manufacturer processing dog kibble, a bucket elevator was allowing excessive product loss due to spillage. 'When the pet food manufacturer switched to an 8' tubular drag cable conveyor, they minimized product spillage and reported a 1-year ROI for the system,' says Owen.
4. Product Quality
For product that is delicate or presents a higher value in undamaged form, preserving product integrity is important. However, the rough mechanical action of scooping/dumping product from buckets can cause incidental damage, lowering value. So can the high-velocity conveyance of pneumatic systems through vertical/horizontal tubing, turns, and sweeps, which can batter product during the process.
In contrast, tubular cable conveyors offer a gentler alternative. When the systems move product through a sealed tube using a coated, flexible stainless-steel drag cable pulled through on a loop, the solid circular discs attached to the cable push the product at low speed through the tube without the use of air, preserving product integrity and minimizing waste.
'After a cereal manufacturer turned to a high-volume tubular cable conveyor it was able to reduce product damage,' he says. The premium for processing high-value products whole and unblemished can be even greater for some products like nuts.
'One food processor that used almonds in its recipe was only able to sell its product for 40 cents a pound if the almonds were damaged. The same product sold for $4 a pound if the almonds were whole and undamaged,' says Owen. He notes that the processor chose to use a tubular cable conveyor to minimize product damage and optimize the sales price.
5. Production Uptime
To reduce production downtime, pet food processors also increasingly expect conveyor systems to be designed for easy cleaning and maintenance. In this regard, bucket elevators are particularly difficult to clean in preparation for production line changeovers. To clean them, each bucket must be time consumingly removed and cleaned inside and out to remove accumulated residue. Belt conveyors are usually cleaned with scrapers, but this can still leave product residue that must be removed with a more thorough method. If not cleaned properly, the food product conveyed must be discarded due to contamination, which equates to lost profit. Or worse, consumers could be harmed, resulting in costly recalls, damage to brand and reputation, or even potential litigation and liability.
With closed conveyors, cleaning is also a mixed bag. Pneumatic conveyors can still be relatively time consuming to clean and sanitize if any manual procedures are involved. With regard to maintaining cleanliness, tubular drag cable conveyor systems generally offer more options for dry and wet tube conveyor cleaning. These include brush boxes, urethane wipers, air knives, inline sponges, inline bristle brushes, and multi-step, essentially automated Clean-In-Place (CIP) wet cleaning.
'Using more automated forms of cleaning like inline wipers, sponges, and air knives or CIP wet cleaning can result in hours of additional production uptime after every product change, compared to conventional manual methods,' says Owen.
Pet food processors are generally more familiar with traditional belt, bucket, or pneumatic systems than with tubular drag cable conveyor systems. Previously, processors had selected these familiar systems when they required higher capacity. Today, however, 8' tubular drag cable units can basically match the high-volume output of the traditional systems but with significant advantages in power consumption, safety, product preservation/quality, and production uptime.
For more info visit https://cablevey.com
By Del Williams - Technical writer based in Torrance, California.
Source: All Pet Food
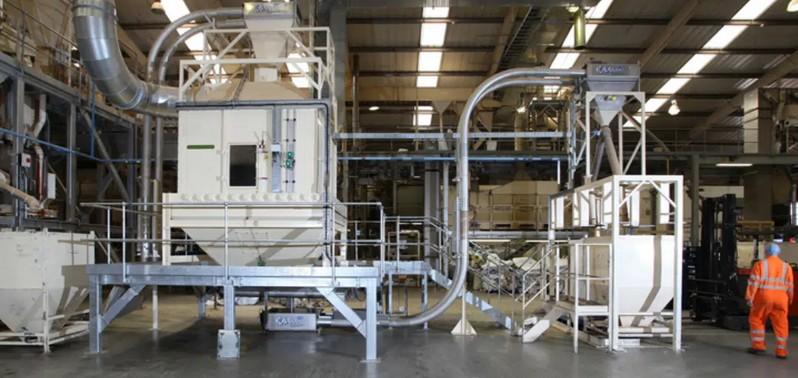
6+ MIN
06/07/2022
Are Pet Food Tube Conveyors Safe And Sanitary?
In 2021, the global pet food industry reached $110.53 billion and is expected to grow at a compound annual growth rate (CAGR) of 5.11% until 2029, when it will be valued at around $163.7 billion. Even though it was expected that the COVID-19 pandemic would have a negative impact on the pet food market – as it had on practically every other global market – the opposite occurred.
The pandemic led to an increase in pet ownership as people looked for companionship and turned to pets for emotional support. In addition, with more people working from home, they had more time to take care of their pets and pay attention to what they ate. Overall, the global pet food market experienced an increase of 4.75% in 2020 compared to 2019.
It is safe to say that pet ownership is at an all-time high. According to The American Pet Products Association, there are over 90 million households across the United States that have at least one pet.
Most of these pet owners are no longer interested in traditional pet foods. They seek healthy ingredients and demand higher transparency when it comes to nutritional labels. What's more, they are willing to pay extra for them. These trends do, however, raise some questions regarding safety and sanitization in pet food production.
Safety and sanitary regulatory compliance in the pet food industry
In the food processing industry – whether that is pet or human food – the safety of the product (food safety) is of paramount importance. A contaminated food product can result in recalls, severely affecting the company's image and revenue.
However, when it comes to the human and pet food industries, the liabilities go beyond mere recall and replacement costs. There is a potential for loss of life, which was the case with the Peanut Corporation of America's (PCA) 2008 tragedy. Nine people died, and over 700 others developed food poisoning due to salmonella contamination, which is a testament to what can happen when safety and sanitation policies are not strictly enforced. The pet food industry also had its share of unfortunate events, where pets have died as a result of contamination or wrong ingredient mixes ending up in the marketplace.
Since 2011, however, with the passing of the Food Safety Modernization Act (FSMA) – the largest food safety reform in the United States in the past 70 years – far stricter food grade regulations were put in place by the US Food and Drug Administration (FDA) concerning the pet food processing system.
As such, there's increased pressure on pet food manufacturers to pay closer attention to safety and sanitation. Pet food processing organizations need to shift their focus away from reacting to any foreign material contamination and look toward preventing it before it happens. It's for this reason that safety, sanitation, and easy cleaning are among the highest priorities when it comes to pet food conveyors.
Pet food material conveying challenges
Here are some of the most common safety and sanitary challenges that a pet food manufacturer might face:
Product breakage and line changeovers
One of the industry's most common issues is product breakage and degradation when animal feed is transported through pet food conveyors.
Several factors influence material degradation, including high conveyor speed, suboptimal inlet design, temperature changes, product shearing, and friction-induced separation. The immediate results may translate into wasted pet food products and higher production costs. It can also lead to a higher risk of cross-contamination of the conveying materials, particularly in the event of line changeovers.
When pet food manufacturers run different materials on the same lines, they need to clean and sanitize the feed conveyors between all changeovers to prevent contamination.
Sacrificing a bit of speed and overall production in favor of somewhat slower tube conveyors will help in minimizing many of the issues associated with product breakage. A tubular disc and cable conveyor has a more sanitary design overall and is easier to clean than other systems like a vibrating conveyor, roller conveyor, auger conveyor, infeed conveyor, chain conveyor, bucket elevators, pneumatic conveyors, and many other types of traditional conveyors.
Maintaining the right nutritional mix
It's also critical for pet food manufacturers to keep the right nutritional mix. Doing so consistently can prove to be a challenge with most conveyor systems. With ingredients having different densities and granularities, separation can lead to proportional inaccuracies.
However, Cablevey's cable and disc drag conveyor systems are better suited than buckets, pneumatics, spiral conveyors, vacuums, horizontal motion open conveyor belts, and other systems for moving material blends without altering the ratios designed by the nutritionist.
Cleaning cable and tube conveyors
The majority of production facilities use bucket elevators for their bulk handling. However, these systems are not exactly hygienically designed, meaning that they require extensive interior and exterior cleaning. As a result, you will have a lot of downtimes, particularly during line changeovers.
On the other hand, Tubular drag conveyors are excellent for food-grade applications because they comply with all of the FDA's sanitation requirements and specifications. Tubular cable and disc conveyors move bulk materials using high-strength, one-piece polymer discs. These are attached to polymer-coated 304/316 stainless steel cables that slide within stainless steel tubing, moving materials through the product stream gently, quietly, and dust-contained.
At the end of every conveying cycle, the discs remove any material fines or waste product from the tubing. Any material clinging to the disc and cable assembly will also be removed.
Ultimately, however, every facility will develop its own cleaning protocols. These will be based primarily on the sanitation regulations and challenges posed by the materials used. The material's reaction to water will indicate whether wet or dry cleaning would be the appropriate choice.
Wet or dry cleaning accessories can be quickly attached to the cable, allowing for fast and thorough cleaning of the system. This will help greatly in minimizing downtime between changeovers. Cablevey conveyors offer both wet and dry tube conveyor cleaning options.
Dry Cleaning
This internal tube cleaning option is applicable for 4-inch, 6-inch, and 8-inch system sizes and configurations and involves several pieces of equipment. These are:
Air Knife – This is a line insert strategically located to blow compressed air and eliminate any accumulated fines off of discs.
Brush Box – Another line insert that will brush off accumulating fines off discs.
Sponge Disc and Sanitizing Cleaner – This is a disposable sponge disc with an applied cleaning agent that's run through the entire system once and discarded.
Urethane Wiper Disc – Finally, this is a disc insert that wipes away any particles and accumulated fines.
Wet Cleaning
Wet cleaning is a fast and easy multi-step internal tube conveyor cleaning process. It is applicable for all the system sizes and configurations, just like the dry cleaning option. Here are the steps to wet cleaning in a tubular drag system:
Water Rinse – Once all material has been discharged from the system, water will be introduced to rinse out the inside of the tube and all other components.
Foam Agent – Second, a foam cleaning agent is introduced into the tube, cleansing all internal parts.
Sanitizing Rinse – A sanitizing rinse will run through the entire system, flushing out any remaining debris, contaminants, as well as the foaming agent.
Final Water Rinse – Lastly, a final rinse of hot water will flush out everything, including the sanitizing rinse, ensuring that the system and its components are all production-ready.
Conclusion
Pet food production facilities must adhere to stringent sanitation and safety regulations, just like human food production facilities. The right conveyor system will go a long way in ensuring compliance.
Tubular drag conveyors are an excellent choice for pet food handling because they are easy to clean and maintain. They also minimize the risk of contamination, helping you keep your facility running smoothly and efficiently.
Cablevey pet food conveyor systems are perfectly suited to move all pet food materials and mixes. Our pet food conveyors can also be engineered to service any part of the production process, making them the top conveyor choice for facilities that worry about finding a conveyor that fits their unique spaces.
Contact us today for more information on our pet food conveyor systems and to discuss your production needs with one of our experts. We look forward to working with you!
by Karl Seidel - Cablevey Cnveyors
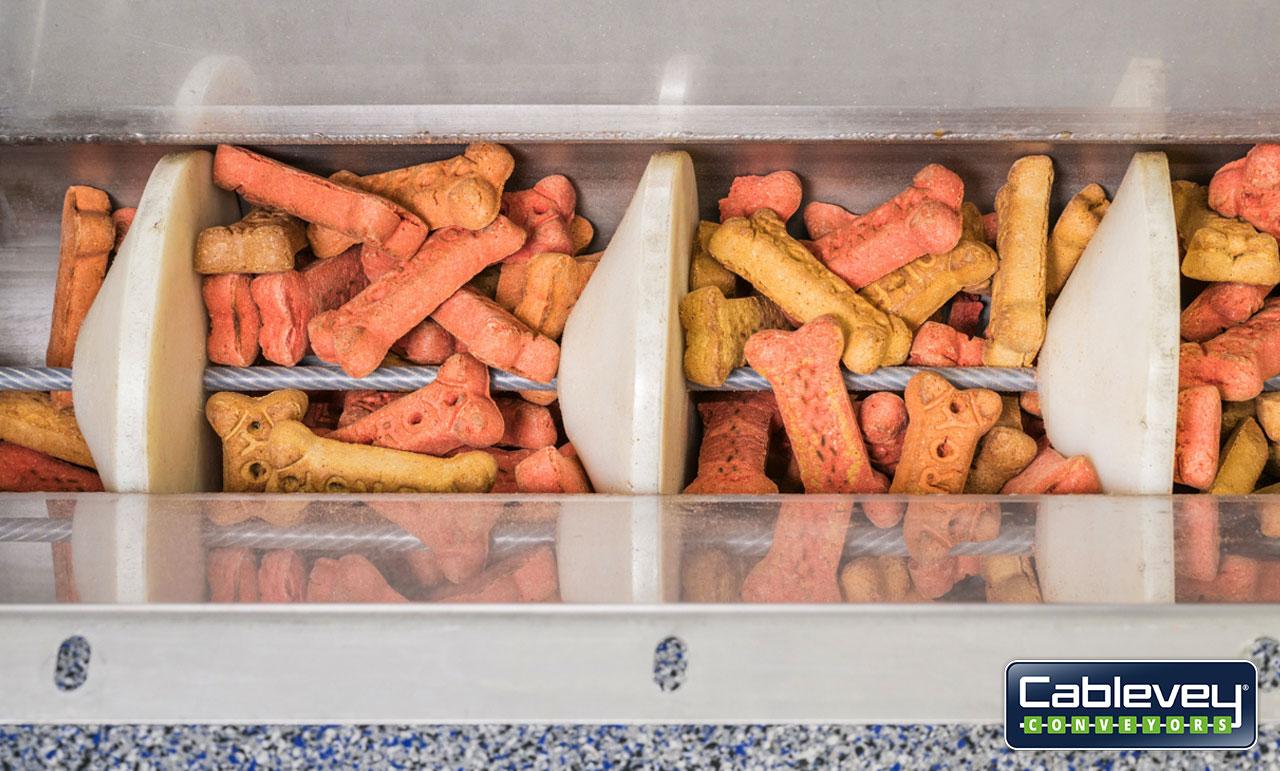
4+ MIN
27/04/2022
State of Conveying Industry Study Reveals Food Processing Industry Outlook
Cablevey® Conveyors, a global specialty conveyor manufacturer for the food/beverage and industrial processing industries, has released results from a new, proprietary survey conducted among food processing companies. The report, The State of Conveying: New Research for the Food Processing Industry, highlights market trends, preferences and challenges related to conveying systems, as well as top marketplace concerns. The findings reveal a high level of automation with most companies operating multiple conveyor lines, yet mixed satisfaction related to the various types of conveyor operating systems.
Key survey findings related to conveyor systems:
• Multiple Lines—83% of companies surveyed operate 6 or more conveyor systems in their facilities with 26% of companies operating more than 25 conveyor systems across business units.
• Conveyor Preference—Among the seven types of conveying technologies survey respondents reported using within their facilities, users were split on the technology most often used, when compared to the technology that generated the most user satisfaction. Respondents reporting using vacuum, pneumatic and cable/disc conveyor technologies most often, in that order. However, cable/disc conveyor systems generated the highest customer satisfaction scores in the study.
• Material Damage – User satisfaction was tied by many respondents to material damage, a critical challenge for those in the food processing industry where the appearance and quality of the end product at times can be damaged by some conveying systems. Relative motion and 'free fall' tended to introduce the greatest levels of material damage; cable/disc conveying was reported as being the top choice to avoid this risk.
• Conveyor Challenges— 54% of survey respondents reported cleaning and maintenance as top challenges related to conveying systems, followed by the corresponding down time associated with these tasks (33%). In addition, 56% of survey respondents reported maintenance issues as the top reason for installing updated conveying systems.
• Selection Factors—Energy consumption and ease-of-cleaning were reported tied as the top factors in the selection process for a new conveyor. Minimization of maintenance came in as the second most critical criterion; initial purchase price was relatively far down the list at #5.
• Evaluation Schedules – 85% said they evaluate their conveying system performance at least every 6 months. Sixty-one percent shopped or purchased a new system within the past 12 months.
Top findings for the food processing industry:
• Industry Growth—91% of respondents reported business growth in the past year.
• Supply Chain—53% of respondents identified supply chain issues as the most pressing industry challenge. Related to this, 39% of respondents cited product shortages as another major issue.
• Agility – 40% of respondents pointed to shifting changes in consumer demand as a challenge, noting the need for agility and rapid response to the market.
Cablevey contracted with independent outside research firm Ascend2, to reach more than 200 professionals at food processing firms including production managers, engineers, and executive managers. The most prevalent product categories being conveyed in the processing facilities included snacks (55%), frozen foods (42%), breakfast cereal (32%), nuts (31%) and coffee (30%), followed by other product types such as pet foods, seeds, beans, specialty grains and hemp.
High-Speed Conveying Systems Critical to Reach Production Goals
'What really stood out in this report was the fact that energy consumption and maintenance issues were cited as the main drivers for conveyor selection and purchase decisions,' said Brad Sterner, Cablevey CEO. 'While we're pleased to see that our cable/disc technology was ranked as the best performing platform to address these concerns, it points out that any automation system, including conveyors, can constantly strive to improve performance and help companies meet both production and sustainability targets.'
'In order to provide food security to a rapidly growing population, suppliers and operators must work together to streamline operations,' Sterner continued. 'The number of high-speed, sanitary conveying systems already in place within food processing facilities demonstrates the critical role they play to help achieve manufacturing goals.'
The Food and Agriculture Organization (FAO) estimates food production needs to increase by 60-70% to feed a global population of 9.3 billion in 2050. For the detailed copy of the survey results, visit The State of Conveying - Cablevey® Conveyors
About Cablevey Conveyors
Cablevey Conveyors is a global specialty conveyor manufacturer that designs, engineers, assembles and services tubular drag cable and disc conveyor systems. With customers in more than 65 countries, the company specializes in moving materials for food/beverage and industrial powder processors that seek food-grade conveying performance with systems that are clean, fast, energy-efficient and cost-effective. For more info, call toll free: 1 (800) 247-3344; Fax: +1 (641) 673-7419; email: [email protected]; or visit https://cablevey.com .
by Cablevey Conceyor
All Pet Food
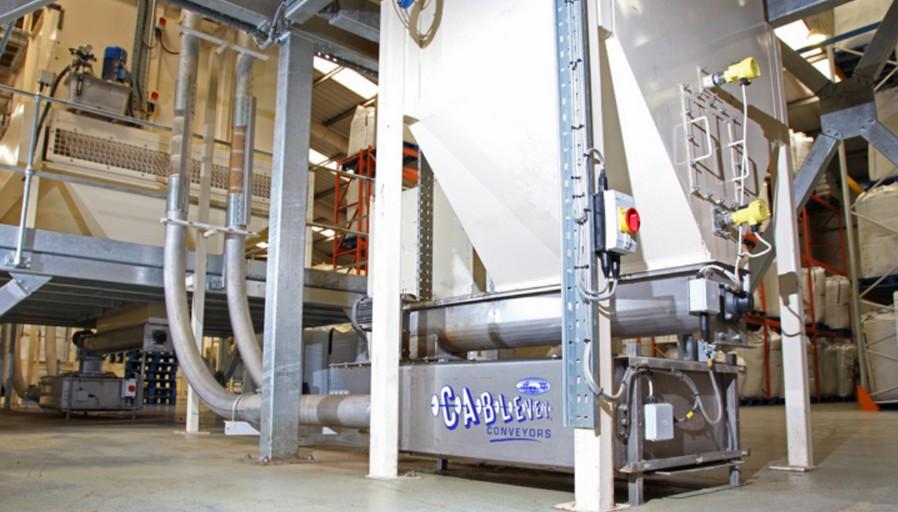
6+ MIN
18/02/2022
Advantages Of Tube Conveyors For Pet Food Manufacturers
Designed for bulk material handling over long distances, conveying systems have helped tremendously in streamlining processes, improving safety, as well as cutting down on manufacturing and labor costs. Today, you can find conveyor systems in almost every industry – from mining, agriculture, automotive to food processing, and, of course, the pet food manufacturing industry.
Pet Food Production Trends
As of 2020, the pet care industry had surpassed $179.4 billion at a compound annual growth rate (CAGR) of 5.2% despite the COVID-19 pandemic, or perhaps even because of it. Various reports stated that the demand for pets practically skyrocketed because of the pandemic. It is a well-known fact that pets minimize the feelings of loneliness and depression that were particularly common during the COVID-19 pandemic.
It's also important to mention that the pet food industry is growing about three times faster than packaged food industries. One major factor influencing this rapid growth mainly revolves around the customers' increasing awareness and concern about their pets' health. Other factors include:
The rising trends in nuclear families.
We are adopting more pets.
Pet humanization.
Premiumization.
The pet food market share can be further classified by pet type, product type, and ingredients, among several others. Dogs are the fastest growing market share based on pet type (cats, dogs, birds, fish, and others). Dry food is also expected to grow in dominance for dogs, whereas for cats, it is wet/canned food. Aside from dry and wet food, other product types include snack food, veterinary pet food, organic, and others.
Tube Conveyors
Tube conveyors are, as their name suggests, material handling systems that largely consist of a sealed tube through which the material is conveyed. They are often used in processing more fragile materials because they can protect the product from potential damage, such as collisions and exposure to high-velocity airflow.
Tube conveyors come in two main forms:
Cable and disc tubular conveyors – This conveyor uses a stainless steel cable encased in nylon to drag solid circular discs along the tube. These discs gently push the material forward through the tube.
Chain and disc tubular conveyors – Similar concept, except the cable is replaced with a chain that runs through the tube. The chain gently pulls the solid circular discs along, which pushes the material forward, similar to cable and disc conveyors.
Tube Conveyors vs. Bucket Elevators
Pet food manufacturers have plenty of options and solutions for using conveyor systems in their facilities. Most often, bucket elevators are used to transport food during processing. Yet, when it comes to bucket conveyors, there are several limitations and potential risks that need to be taken into consideration. Sanitary design and compliance are good examples.
According to the food-grade regulations set by the US Food and Drug Administration (FDA), the Food Safety Modernization Act (FSMA), and the Federal Food Drug and Cosmetic Act (FFDCA), pet food manufacturers are required to clean their conveyor systems regularly. There are many types of ingredients and materials handled and moved through these systems at different stages of the production process. All of these materials must adhere to the same sanitary requirements as human food products.
By their very design, bucket elevators are prone to causing spills, have limited layout options, require more space and maintenance. Bucket elevators are harder to clean and sanitize when compared to a tube conveyor system.
Enclosed tubing is typically made of stainless steel that is naturally corrosion-resistant. This steel may also incorporate a special finish that will make it easier to clean. Other alloys will have different properties from this point of view. Cablevey conveyors use both alloy 304 and 316, which have excellent anti-corrosive properties.
Tube Conveyor Benefits
Better Material Handling
When dealing with pet food, it's important to remember that some pellets are fragile products. Fish food, in particular, is especially prone to product breakage, which affects salability and packaging. Tube conveyor systems ensure that any product breakage will be kept at a minimum throughout the manufacturing process.
Maintaining Proportions
Building the right nutritional mix is a huge factor for pet food manufacturers to gain a considerably larger market share. As mentioned earlier, premiumization is a determining factor for the growing pet food industry, meaning that providing consistent product quality can make or break your profit margins. There have been reported cases when an incorrect mix of ingredients resulted in pet deaths.
However, maintaining the right proportions can be a challenge since ingredients can have variable densities and granularities. This can lead to separation issues and affect proportional accuracy. Cablevey's cable, disc and tubular drag conveyor system wins over buckets, pneumatics, vacuums, and other systems in this regard. This system moves material blends without actually changing the ratios designed by the nutritionist and employed by the manufacturer.
Eliminating Spillage and Product Loss
Cable and disc tube conveyors are enclosed systems that have minimal wear on long-lasting parts. Fugitive dust is kept at a minimum while also eliminating any spillage and product loss. The system also reduces the possibility of cross-contamination, which is relatively common with other transportation systems. And by using the included wiper disc and (optional) air knife, tubular conveyors can also be self-cleaning.
Flexible Design
Cablevey Conveyors also offer a great deal in terms of customization. Our tubular drag conveying systems come in different diameters such as 2″ (50.8mm), 4″ (101.6mm), 6″ (152.4mm), and 8″ (203.2mm) for different needs. Additionally, they feature a series of highly flexible and modular components that can cater to all sorts of factory floor requirements. These will help facilitate easy access and maneuverability throughout the factory. These components include the following:
Drive Units – Cables are pulled through a drive unit by an electric gear motor. Depending on the exact layout, the cable can enter and exit through either tube port so as to be in line with the specific system layout.
Funnel Outlets – Used to discharge materials from cleanouts and rotary discharges, Cablevey's funnel outlets come in various sizes and connection types to fit each plant's own needs.
Inspection Sections – Made out of food-grade plastic tubes, inspection sections allow you to inspect the conveyed product and observe the cleaning process. These inspection sections can also be installed vertically or horizontally, depending on your needs.
Sweeps – Cablevey's sweeps can change their travel to any desired direction and area available in different radius dimensions and many different angles to fit restricted spaces.
Compression Couplers – They hold the tubes together in perfect alignment for the discs to have a smooth path. Their food-grade rubber gaskets also ensure that no water, air, or dust will enter the system.
Inlet – The inlets come in various lengths and slopes to accommodate different needs and material flows. If desired or needed, multiple inlets can be used on the same system.
Turnarounds – Turnarounds contain a sprocket to move the discs and cable around the system smoothly with applied tension.
Discharges – The discharge mounted on the system can either be open or closed, allowing materials to pass through or exit the conveyor at that point.
Brush Boxes – Cables and discs pass through the Brush Box, removing any remaining particles.
Low Maintenance and Even Lower Costs
Tube, cable, and disc conveyors often use smaller drives than bucket elevators or tubular chain and disc conveyors. This translates to less noise pollution and less power usage, keeping operating costs low.
In terms of maintenance, tube systems require only periodic inspections of the discs, cable couplings, and other components. If a disc becomes damaged, pet food manufacturers only need to replace that disc without having to replace the entire cable system. And being a self-tensioning device, constant manual cable tension adjustments are not required as with other systems.
Conclusion
While plenty of conveyor manufacturers create systems for pet food processing, not all of them offer the same efficiency, gentle use, and sanitary conditions as Cablevey. Our pet food conveying equipment is perfectly-suited to move all sorts of pet food materials and mixes, regardless of their composition and fragility.
What's more, you can customize it to fit your unique needs and facility requirements while also enjoying the convenience of less downtime and maintenance at a minimum cost. Contact us if you'd like to know more about how our systems can help your pet food manufacturing facility.
by Karl Seidel - cablevey Conveyor
All Pet Food
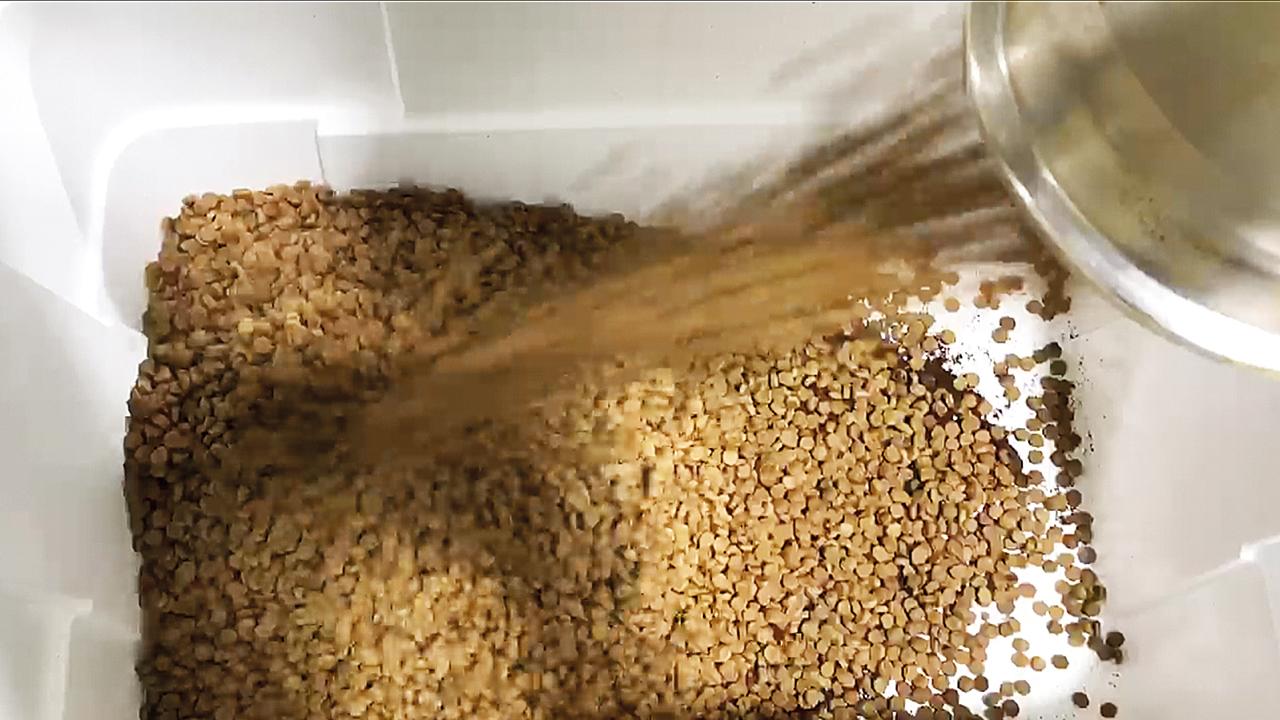
6+ MIN
03/02/2022
Cablevey Conveyors debunking misconceptions about tubular drag conveyors
In the pet food processing industry, walking onto the production floor with conveyor tubes winding this way and that, in and out of machinery can seem to visitors like they have stepped into a Dr. Seuss book or Willy Wonka and the Chocolate Factory movie. For example, at a glance even industry veterans can be challenged to distinguish whether the conveyor tubes they see are screw (augur), pneumatic, vacuum, aeromechanical, tubular drag chain and disc or tubular drag cable and disc, unless they are the plant engineer or maintenance crew. In fact, many specifiers, architects, engineers, and other professionals lack substantial technical or hands-on experience with such conveyors. This knowledge gap can result in extreme consequences when delicate pet food or precise blends must be reliably conveyed but instead, costly product destruction or inaccurate blends occur. Misconceptions about tubular drag cable and disc conveyors will be the focus of this assessment, addressing six widely held viewpoints in the industry. Tubular drag cable conveyors gently move product through a sealed tube using a coated, flexible stainless-steel drag cable pulled through on a loop. Solid circular discs (flights) are attached to the cable, which push the product through the tube without the use of air. These conveyors excel in transporting delicate, precise blends for a wide variety of pet food types in versatile layouts and configurations. Misconception #1: These Conveyors are the Same as a Screw System 'One of the most common misconceptions is that tubular drag cable and screw conveyors are identical, which is far from the case,' says Karl Seidel, marketing director of Cablevey Conveyors, a mechanical conveyor manufacturer that serves the pet food, specialty food, coffee, powder, and nut markets. Screw systems, also known as auger conveyors, typically utilize a helical blade that moves granular materials within a tube. However, augurs can cause product damage and compromise blends. So, the units tend to be an option when material integrity is not critical, such as when conveying food waste. Seidel notes, 'The key difference to look for is that augurs convey material with a helical screw. The transfer speed is directly proportional to the rotation speed of the screw. On the other hand, tubular drag cable conveyors transfer material between two discs pulled by a sealed cable and are designed to protect delicate products and blends.' Misconception #2: Conveyors Are Not Designed to Protect Blends and Mixes When transporting a blend of pet food product or supplement with a conveyor system, maintaining a consistent mix ratio is essential, whether a coarse mix, fine powder, or larger variable-sized amalgams of different weights and shapes. However, conventional conveyor systems are not specifically designed to precisely transport pet food blends without changing the mix ratio. Various product material weights, sizes, and shapes can shift and disperse in open systems like bucket conveyors, and vibration can cause the blended product to shift throughout transport. Vacuum and pneumatic systems can cause smaller lightweight particles in a blend to move at different speeds than heavier or larger particulates, resulting in significant blend restructuring when the product reaches its discharge point. In contrast, tubular drag cable conveyors are engineered to maintain precise blend ratios, which can be important to pet food industry professionals such as nutritionists and quality control experts. As an example, according to Seidel, the company's engineers have resolved the issue with a completely enclosed, compartmentalized tubular conveyor system. 'Not unlike an endless succession of train cars, each space between solid circular discs holds a predefined volume of product. Based on the manufacturer's specifications and requirements, engineers can calculate the optimal speed of the system, the most appropriate tube angles, and the proper construction design to guarantee their blended product remains consistent from input to discharge, even at high volumes,' says Seidel. His company has designed, engineered, and serviced enclosed cable and disc tube conveyors for 50 years in over 66 countries. Misconception #3: Conveyors Cannot Carry Moist, Hot, or Frozen Material Tubular drag cable systems like Cablevey's convey pet food materials in a wide variety of forms and states including whole, powdered, pureed, chopped, moist, hot, and frozen with throughput rates up to 80,000 pounds per hour. The systems can convey material with high moisture content when some water is being conveyed along with the product. While the tubular conveyors are constructed of plastic components, the standard units are designed to operate at 180° F (82° C) with a high-temperature option up to 230° F (110° C), so can receive the product from ovens, fryers, or dryers, according to Seidel. Even frozen products can be conveyed, although it is important that the temperature is controlled along the path, so no melting occurs with water freezing later in the system. Misconception #4: Conveyor Footprint and Expansion Limitations in the pet food industry do not consider tubular conveyors because they mistakenly believe that the systems cannot fit within their facility's available space or accommodate its layout, which may include significant inclines or elevation changes. However, this is not the case. Modular systems like tubular drag cable conveyors are an excellent option for complex layouts that could require curves or changes in direction, according to Seidel. 'Tubular conveyors do not have to be installed at 90 degrees and can use angles so can go in between, around, above or below existing equipment or other obstacles. That is important for existing facilities that may not have the flexibility to move something out of the way,' says Seidel. In addition, tubular conveyors are quite space efficient. Seidel notes that to conserve space, the conveyor turnaround and its inlet can stand on end, so it is only one foot across instead of three. If conveyor discharge occurs best using gravity, tubing can be run through walls and discharge out of the building roof, which saves interior space. Misconception #5: Cleaning Requires Dismantling and Extended Downtime Between product changeovers, many traditional conveyor systems must be disassembled, cleaned, or soaked, and then reassembled – a labor and time-intensive process. However, this is not necessary for tubular conveyors. With tubular conveyors dry, wet, and in-line cleaning options are available, according to Clint Hudson, Cablevey Conveyors Engineering Manager. Among dry options, brush boxes and air-knives can clean the cable. Brushes and wipers can wash the tubes. To sanitize, a sponge soaked in sanitizer can be used without getting the system fully wet. For the most thorough cleansing, the cable conveyor's wet cleaning process internally washes the tube in several steps, starting with a water rinse followed by a foaming agent, a sanitizing rinse, and a final water rinse. Once the system is thoroughly flushed out, drying is achieved by attaching urethane wipers to the tubular conveyor's discs, which 'act like a squeegee' to remove any residual water. Misconception #6: Conveyors are Indoor Installation Only It is a misconception that tubular conveyors are only installed indoors. In fact, it is common to see portions of equipment extending outdoors. This may occur when conveying product from outside to inside such as when unloading raw material from a truck or railcar or loading finished product into similar transport. Materials may also travel from a feed mill to a production or packaging room which may be ten feet or even one hundred feet away. According to Hudson, when some of the equipment is utilized outdoors, and when the company is moving a moist product, it can be helpful to wrap the tubes in heat tape to prevent moisture from condensing or freezing in the tubes. The conveyor manufacturer can also provide a range of accommodations to account for the effects of wind, dust, rain, insects, and direct sunlight. While first impressions of tubular drag cable and disc conveyors can evoke images of Dr. Seuss or Willy Wonka's chocolate factory, the equipment has been carefully designed and engineered for industrial performance, reliably conveying delicate pet food products and blends in a variety of conditions. With an understanding of the true potential of these conveyors, industry professionals will be well-positioned to take advantage of the systems' abilities to decrease downtime and increase quality production. Source: Cablevey Conveyors
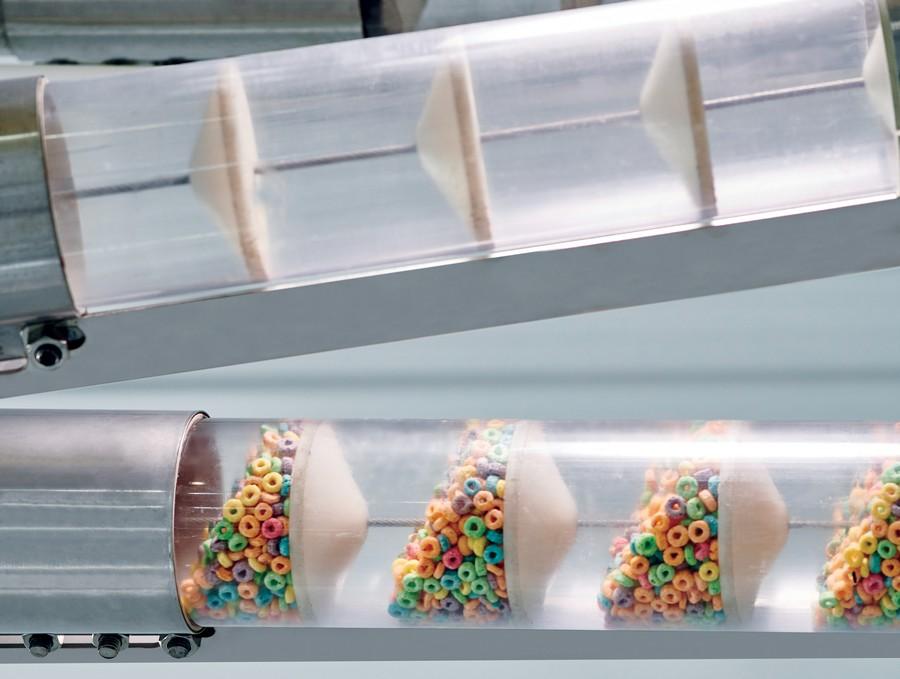
3+ MIN
11/01/2022
May River Capital Acquires Cablevey Conveyors - Market Leader in Specialty Conveyance Serving the Food and Beverage, Pharmaceutical and Chemical Markets
Chicago — January 10, 2022 – May River Capital, a Chicago-based private equity firm focused on lower middle market industrial growth companies, announced today that it has acquired Cablevey® Conveyors, a global manufacturer of tubular drag conveyor systems based in Oskaloosa, Iowa. Cablevey is a market-leader in enclosed conveyance systems, with installations in more than 65 countries. The company's technology is known for food-safe, efficient and low-energy consumption performance for some of the most demanding applications in the material handling sector.
'Cablevey's focus on solving conveyance application challenges using our proprietary cable drag technology, and the resulting dramatic growth has positioned the company as an anchor asset to build a larger conveyance platform,' said Cablevey CEO Gary Hall. 'The additional investments now possible with May River allow us to continue to increase market share with existing and top tier customers in our core food and beverage sectors, including tree nuts, coffee and pet food, as well as expand in other growth markets like pharmaceuticals.'
'Gary and I could not be happier for the employees, the Oskaloosa, Iowa, community and customers of Cablevey, and we are thrilled to partner with the May River team,' said Cablevey President Phil Hall. 'We look forward to further building upon Cablevey's 50-plus year history of developing and bringing new product innovations to market, such as our new 8' drag conveyance system that adds tremendous value to those who rely on Cablevey to deliver clean, fast and cost-effective conveying solutions.'
'It's truly a privilege and opportunity to lead a business like Cablevey and the dedicated Cablevey team,' explained Brad Sterner, who will succeed Gary Hall as Cablevey CEO. 'Gary, Phil and I are looking forward to working through the transition as we collectively turn our attention to the next phase of the company's growth.' Sterner will continue as Executive Chairman of Advanced Material Processing (AMP), a May River 'sister' platform specializing in material processing equipment for regulated end markets. This 'sister' relationship will offer potential synergies with Cablevey that include many shared customers in the food, pharmaceutical and chemical end-markets.
'We are excited about the specialty conveyance sector and attractive high growth end markets served by Cablevey and the highly complementary AMP process equipment platform,' explained May River Partner Steve Griesemer. 'As the handling and process industries continue to expand, leading end users in the food and beverage, pharmaceutical and chemical verticals seek to align with innovative partners that can be counted upon to deliver market-leading solutions. Cablevey will serve as a strong foundation within the material handling segment for delivering high-impact solutions to these global, blue-chip customers.'
Hall said the timing of the announcement is meaningful, as the acquisition closed on December 22, the exact date of the company's 50th anniversary.
'Achieving such a significant milestone serves as a reminder of our commitment to our employees, customers and community,' added Hall. 'In fact, Cablevey will continue to operate in Oskaloosa and contribute to our local Mahaska County economy as we have every day for the past 50 years.'
Winston & Strawn served as legal counsel to May River. NCP Inc. served as financial advisor and Belin McCormick served as legal counsel to Cablevey Conveyors and its shareholders.
About May River Capital
May River Capital is a Chicago-based private equity firm focused on investing in lower middle-market, industrial growth companies. May River Capital invests in high-quality industrial growth businesses, including precision manufacturing, engineered products and instrumentation, specialized industrial services, and value-added industrial distribution services. For more information, please visit mayrivercapital.com.
About Cablevey Conveyors
Cablevey Conveyors is a global specialty conveyor manufacturer that designs, engineers, assembles and services tubular drag cable and disc conveyor systems. With customers in more than 65 countries, the company specializes in moving materials for food/beverage and industrial powder processors that seek food-grade conveying performance with systems that are clean, fast, energy-efficient and cost-effective. Learn more at www.cablevey.com.
by All Pet Food
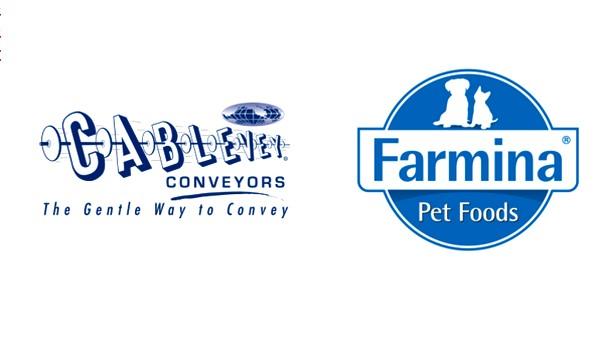
3+ MIN
07/12/2021
Farmina & Cablevey: Together, striving for excellency!
Guided by genuine care for animal well-being and by acknowledgement of the unwavering love and support they provide as pets, Farmina came to be as a result of Dr. Francesco Russo's lifelong passion and craft in 1965, in Italy. The company has since dedicated its resources and energy to developing its narrative in the way most suited to the values it embodies. Built upon extensive and meticulous research, Farmina offers a wide array of options when it comes to animal nutrition, including specifically balanced formulas meant for professional dog and cat breeders, a niche which involves the highest levels of precision and planning. Aside from that, they offer extensive customer support in the form of a consultancy service that creates specific dietary plans for different pets. Farmina's accolades really speak for themselves: from published articles in Cambridge's British Journal of Nutrition and flourishing partnerships with world-renowned animal care institutions such as Napoli's Federico II University of Animal Nutrition and Feeding, it becomes clear that Farmina is a name of high regard. With a highly-qualified group of specialists, veterinarians, zoologists and animal nutritionists, coordinated alongside the most structured research methods and highest-quality available equipment, success becomes only natural. In a process with as many variables as pet food production, what sets Farmina apart from the competition is not a single factor, but rather several different factors working together. One of these elements is the continuous improvement of technology and plant infrastructure; as the product can only be as good as the equipment allows. In their tireless striving for excellence and improvement, Farmina came upon another company regarded for their striving, but in the field of material transportation: Cablevey Conveyors The Cablevey tubular drag conveyor is an essential element to any high-standard food processing operation, as its cable and disc technology is capable of transporting any kind of material with virtually no breakage or waste. It can be specifically fitted to any product or plant layout, is highly adaptable, produces a very low amount of sound, runs on a small energy consumption, has very little downtime due to simple and sparse maintenance, is self-cleaning and completely sealed-off from foreign contaminants in the environment. With a working capacity ranging from 3,000 lbs/hour (1,361 kg/hour) to up to 80,000 lbs/hour (36,267 kg/hour), it can move material of any granularity, frozen, frosted, coated, delicate or powdered with food-grade cleanliness standards, all whilst reducing particle breakage to numbers below 1%. Located in Oskaloosa, Iowa, Cablevey has been in the business for almost five decades and works with over 900 types of products in 66 different countries. Many of the world's largest food companies have chosen Cablevey due to its high efficiency, adaptability and food grade operation. Brands such as Nestlé, Premier-Grandfoods, Affinity Special Dog, Royal Canin, Unilever, Purina, Starbucks, Hercosul, JDE and many others all use Cablevey Conveyors. All these companies have high standing among their respective fields, and this is a trait they share with Farmina. The levels of excellence achieved could only be reached through the careful selection of materials and equipment. A globally-renowned brand name is born when a company takes it upon themselves to create the best product they possibly can, sparing no resource or effort. The search for quality should be tireless, and that is both the most essential component and greatest challenge of the process. Farmina's sheer dedication to their craft is what really makes them unique, placing them among some ot the greatest brands of all time. by Cablevey Conveyor Source: All Pet food
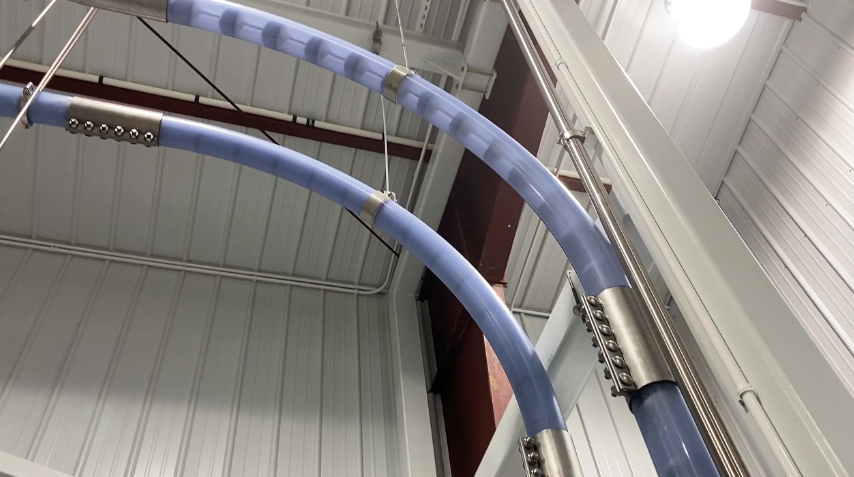
3+ MIN
15/11/2021
Pet Food processing requires thorough Conveyor "Wet Cleaning" to ensure food safety
To meet strict compliance standards, such as the Federal Food, Drug, and Cosmetic Act, pet food processors now utilize ATP testing to monitor equipment surfaces for microbial growth. Add to this the need to minimize cross contamination of products or ingredients with allergens after production changeovers, and more processors are realizing that the traditional means of cleaning conveying equipment may not be sufficient to meet today's rigorous compliance requirements. In the pet food processing industry, when conventional conveyors need to be disassembled, cleaned, and reassembled to reach all exposed internal surfaces, potential downtime can extend to days. If this proves too onerous, some processors dedicate separate conveyor lines to specific products, which increases capital equipment costs, labor, and the production space required. As an alternative to speed the process, pet food processors are turning to tubular drag conveyor systems, which gently move product through a sealed, enclosed tube using a drag cable and circular discs pulled through on a loop -- ideal for delicate items. Because tubular cable conveyors are enclosed, these systems can be quickly and effectively flooded with water, flushed, rinsed, cleansed, and thoroughly sanitized without disassembly – a process called 'wet cleaning.' For pet food processors, this 'wet clean' approach significantly improves food safety compliance and system reliability. The technique, in fact, thoroughly flushes out any potential trace allergens from conveying equipment that could be used for multiple products. Since a complete and thorough cleaning can be accomplished without disassembly of the system, the entire process only takes 20-90 minutes. This can substantially reduce downtime during production changeovers and eliminate the need for unnecessary additional dedicated conveyor lines. For pet food processors conveying a specific product, regular cleaning can be set to run on an automated basis. To resolve potential food safety and downtime issues, a growing number of pet food processors are replacing pneumatic conveyor systems with tubular cable conveyor systems with automated wet cleaning capability, such as those from Cablevey Conveyors. The Oskaloosa, Iowa-based conveyor manufacturer has designed, engineered, and serviced enclosed cable and disc tube conveyors for 50 years and is in more than 66 countries. The system can convey up to 2000 cubic feet per hour of materials with numerous layouts using multiple inlets and outlets. The cable conveyor's wet cleaning process internally cleans the tube in several steps starting with a water rinse followed by foaming agent, a sanitizing rinse, and a final water rinse. Once the system is thoroughly flushed out, drying is achieved by attaching urethane wipers to the tubular conveyor's discs, which 'act like a squeegee' to remove any residual water. To automate the cleaning process, Cablevey can help to integrate the conveyor with pet food processors' distributed control systems (DCS). By automating the cleaning, the system is essentially self-cleaning, so it is convenient to let it run through the cleaning process as employees take care of other tasks. Clear tubes can be chosen as an option for the conveyor system to provide greater visibility into the cleanliness of the equipment and the cleaning process as it occurs. For added food safety, processors can choose to add a unique inspection option that enables the running of a small, lighted camera system internally through the tubes, with video viewable on a smartphone via an app. Usually, this level of inspection is performed on an as-needed basis to further verify or document cleanliness. This clear tube system is transparent except where the clamps are, so pet food processors food packagers and processors can visually check at any time, and the internal camera system enables seeing 'every nook and cranny from the inside'. This, along with regular ATP testing, provides processors with the confidence that they are reliably meeting all necessary QA and food safety standards. Compared to air conveyor systems, the approach can also run significantly more product an hour with less downtime and less potential breakage. For the pet food processing industry, the wet cleaning capability is advantageous when dealing with a wide variety of products. As processors respond to the need for greater safety, flexibility, and efficiency, tubular conveyors with the ability to wet clean are an important tool to consider. Author: Del Williams, technical writer based in Torrance, California. Source: Cablevey
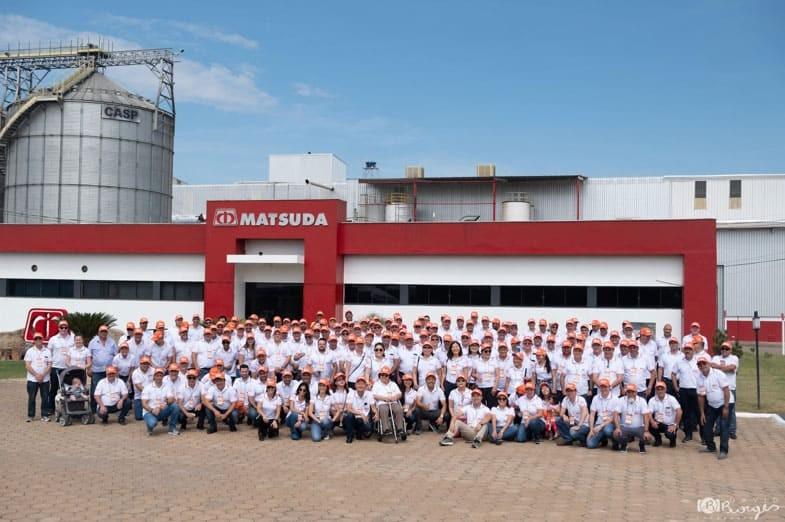
2+ MIN
28/10/2021
Matsuda & Cablevey Conveyors: Dedication and Reliability
With three production plants located in different Brazilian states, Matsuda Pet's dedication is its unifying quality common to each of its undertakings, from its several specialized pet food lines to the detailed entries in its weekly blog regarding animal health, pet nutrition and the pet food industry. Matsuda Pet moves forward with great regard for the legacy of the late Jorge Matsuda, a great businessman and philanthropist responsible for decades of steering the company in the direction of its prosperous growth. The Matsuda Group's decades of practical experience in the production of agricultural supplies were made evident by Matsuda Pet's rapid growth, whose high-quality products speak for themselves. Even though they are thoroughly dedicated to product quality, Matsuda Group still pays great attention to social aspects, sharing returns with the local community through actions such as donating to Casa Transitória Irmã Dulce, an institution in which recovering cancer patients receive care, and also through donations of tons of dog food to several non-profit animal shelters In the year 2020, Matsuda Pet inaugurated a new production line which doubled the company's pet food yield, a process in which Cablevey was a fortunate collaborator, furnishing the project with state-of-the-art conveying solutions. In 2021 Matsuda Pet has once again chosen Cablevey, this time incorporating cable and tube technology to overhaul and perfect the existing production lines. Cablevey offers a customizable, versatile, economical, clean, silent and compact alternative to machinery such as bucket elevators, screw conveyors, vibratory conveyors and many others. Without a shadow of a doubt, Matsuda Pet has chosen the best possible solution, a result of their great care in assembling the most advanced possible production process. When selecting the finest technology for your plant is a concern, one can't help but notice Cablevey is always present. Just as the Matsuda Group's 70 years of experience have been paramount to Matsuda Pet's development of extremely refined nutrition options for dogs and cats, Cablevey's 50 years of experience are the driving force behind our continuous improvement of the conveyor system which serves over 1,000 products in 66 countries. From Nestlé to Unilever to Mondelez to Cargill, Cablevey is a common factor among great names in the industry, and Matsuda Pet was able to pick up on this fact. With profound respect and commitment to its clients, Matsuda Pet has continually invested its effort in optimizing production, maximizing quality and prioritizing customer satisfaction. by Cablevey Conveyor
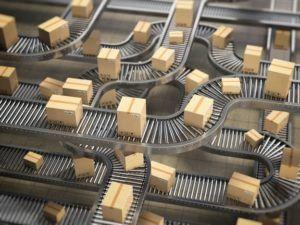
10+ MIN
14/06/2021
The Complete Guide To Industrial Conveyors
In 2020, the global conveyor market was estimated at $7.73 billion. By 2026, this value is expected to increase up to $10.07 billion. Short production cycles, advancements in e-commerce (especially due to the global health pandemic), and an improved international flow of goods all contribute to the growth of the conveyor market. The globalization of the economy is a direct result of the automation that conveyors bring. If your business needs a new, faster, and more reliable way of transporting items (raw materials, goods, or products) within the same facility or area, industrial conveyor systems are the right solution. The complete guide to industrial conveyors will present you with the basics of what you need to know about these systems, how they work and how they are used, and how you can select the best type of conveyor for your organization. Conveyor Systems: Definition Intralogistics is the process of managing the flow of information and material goods inside a production or distribution facility. Conveyor systems are an important segment of intralogistics. They serve to transport bulk products, raw materials, goods, or any other type of materials from point A to point B that are usually located in the same area or even building. The industries that benefit the most from conveyors include: Mining industry Warehouse and logistics Agricultural industry Aerospace industry Chemical and pharmaceutical industries Food processing industry Packaging industry Beverage industry Automotive industry Bottling and canning industry, and more The main reason why industries have almost completely switched to automated material handling and transport is that this enables them to move vast amounts of material and continuously operate. Compared to workers who need rest, conveyor systems don't need much downtime due to maintenance and cleaning. They can run almost non-stop, which means the production numbers of your facility will skyrocket. The System Breakdown How does an industrial conveyor system work, anyway? Depending on the type of material it is handling and its purpose, different conveyors, work differently. Nevertheless, all of them have a few basic components they cannot function without Drive There are three most common drivers (power sources) for conveyor technology: Motors Gravity Manual drive Industrial systems are typically powered by motors. The most prevalent motors for conveyors are three-phase AC motors, perfect for systems that continuously run in one direction. Single-phase comes with starting windings and capacitor delays, which are not suited for conveyor systems. Most facilities utilize 440V motors because, with high voltage, there are lower transmission losses over the grid. However, not all conveyors need to be powered by electricity. Manual and gravity-based systems are usually centered around rollers. Rollers inside a frame allow workers to push an item from one point to another if the frame is horizontal or slide it down an angle if the frame is tilted. These conveyors do not require any energy to function and are a good fit for packaging processes, where large, non-fragile items are moved around. Mode of Transfer The main difference between conveyor types is the way they move materials. This can be done in any number of ways or combinations determined by the production facility's goals. You will often run into the following methods of transporting goods: Belts – made from various materials that rest on a steel frame that supports them and the items they're moving. Chains – endless chains move thanks to sprockets at each end of the trough. Buckets – containers attached to belts, cables, or chains that move the material along. Cables – moving materials with the help of a coated, flexible, stainless steel drag cable with discs attached to it. Pneumatic – moving materials thanks to compressed air (positive conditions) or a vacuum (negative conditions). Screw or auger – a helical blade called an auger, typically placed inside a tube, that rotates and moves the material. Aero-mechanical – the material is driven at high speeds on evenly spaced discs. These are just some of the examples of how conveyors transport materials. Which one is most suitable for your business depends on a series of factors we will cover in a bit. Support An industrial conveyor system would not be able to operate without many of its support mechanisms. It needs the proper frames to hold the belts, chains, sprockets, buckets, and similar components. It also requires cleaning or maintenance features. Controls Lastly, industrial conveyors are controlled in various ways. Some operate only in one direction, while others can reverse direction if needed. All conveyors should be outfitted with emergency stop buttons and safeguards in case of an accident. Conveyor Applications What are industrial conveyor systems used for? We already mentioned that their primary purpose is to move products or materials. These systems can also store and buffer materials if the process requires it. Here are the main applications of an industrial conveyor system: Moving Materials Standard transport. If there is a need to move the same type of material from the same starting point to the same endpoint over and over again, there is no point in forcing workers into these repetitive motions that might damage their health. The movements of forklifts can also be reduced by installing a conveyor that will cover this distance and take over the transport. Heavy load transport. Some items cannot be moved due to their size and/or weight. Special conveyor systems are built for materials that are too large or too heavy for a worker or forklift. Assembly conveyor. Working on an assembly line requires a conveyor to move an item as workers perform their tasks. These conveyors are frequently used in a wide range of industries, especially in the automotive sector. Protection from damage or injury. Some items are not too heavy or too difficult to move. However, performing repetitive movements, such as transporting a product from one location to another, represents a danger to workers' health. Conveyors can achieve the same in less time and with much less muscle strain involved. Also, some products or materials are too fragile to be moved by hand or forklift. Human error is a significant factor in why businesses suffer losses in the manufacturing process. To reduce this risk, it is good to introduce conveyors as a safe way to transport easily damaged products. Bulk material transport. Gravel, sand, iron ore, coal, and similar are not easy to transport no matter what your options are. The right type of conveyor can prevent many headaches when it comes to moving materials in bulk. Complete automation. In the end, perhaps you are aiming to automate your business from head to toe. If there are no workers involved in some segments of your production, conveyors and robots, go hand in hand. If robots deliver products to the conveyor or receive them from the conveyor, it is easy to control the production and adjust it for just the right output you need. Storing and Buffering Product storage. If there is a demand for product storage before the next production step, specific conveyors can accommodate this. Accumulation bank. An accumulation bank is also called a buffer. This is a flexible type of storage that manages the flow of production. A buffer can either be increased or decreased depending on the demands of the process. Conveyors can also allow workers to sequence and resequence products between processes. Organizing products into batches and prioritizing them increases productivity. Types of Conveyor Systems Based on this outline of conveyor basics, it is rightful to assume that there are various systems. So, what are the different types of industrial conveyors? Let's explore the seven most common conveyor types. Aero-Mechanical Conveyors Aero-mechanical systems are made from a steel tube with a circulating rope running through it. Evenly spaced discs along the rope carry material, creating an airstream by moving at high speeds inside the tube. These speeds generate a centrifugal force that ejects the material once it reaches its destination. These conveyors can operate vertically or horizontally and are quite flexible. They convey materials at high velocities, depending on their application, and are easy to clean. At the same time, these velocities lead to compromised material integrity. If the goal is to reduce material breakage in such a system, the speed should be slow and steady. Aero-mechanical conveyors also require rope-tensioning, making them difficult for maintenance. Auger (Screw) Conveyors Auger is a helical blade (a screw) that moves granular or liquid materials by rotating, usually inside a tube. The rate at which the material is transferred is directly related to the rotation speed of the auger. It is one of the first conveyors to be invented since ancient Greeks used it to transport irrigation water. Screw conveyors are good at transporting semi-solid materials, like food waste, municipal solid waste, animal feed, meat, boiler ash, aggregates, and similar. They are also easy to clean and maintain because they don't have many moving conveyor components. Unfortunately, auger conveyors can compromise blends and lead to material breakage. Their efficiency isn't as high in steep inclines, and it cannot be used in spaces that require multiple planes. Belt Conveyors Belt conveyors are arguably the most common type of conveyor, found in practically every sector. They have two or more pulleys and a closed loop of material (the belt) that rotates around them. A motor can power these pulleys to move the belt and its materials in the right direction. There are two main types of belt conveyors: For bulk materials, such as coal, salt, grain, ore, and sand For general materials, such as boxes, solid items, and packages Belt conveyors are not used only in industrial settings. They also transport luggage at airports, food at restaurants (such as sushi conveyor belts), and even skiers at mountain resorts. Belt conveyors can also be enclosed to prevent loss of material and contamination. Bucket Elevators Bucket conveyors move flowable bulk materials (grain, fertilizer) upwards in multi-sided containers. The most significant downside of bucket elevators is that they have a lot of moving parts which are difficult to maintain. Aside from the buckets, this system also includes a belt to carry the buckets and a power source to drive the belt. It can also come with accessories for loading the buckets, receiving the discharged material, and similar. These conveyor systems have low driving power and are therefore quite efficient. However, bucket elevator components require high maintenance expenses, and the equipment is challenging to clean. Cable Conveyors Cable material handling systems include a cable, usually one made of stainless steel. If they are enclosed, tubular cable conveyors minimize contact with food materials and preserve material integrity. To transport the material, solid discs are attached to the cable. They push the material through the tube. Cablevey tubular cable systems have low energy consumption because their motors are typically 5 HP (up to 7.5 HP). They can move material at angles, vertically, horizontally, or in tight sweeps. They have removable parts, making them easy to maintain. The main advantage of tubular cable systems is that they eliminate the factor of material degradation. They provide a dust-free environment and allow for consistent blending. They are ideal for the following materials: Nuts Snack foods Pet food Breakfast cereal Coffee Frozen food Specialty seeds Beans Powders Biomass Fluff plastic Industrial hemp, and more Chain Conveyors These conveyors are made from an endless chain supported by sprockets. Chains can have special attachments to them for carrying specialty loads. Transporting heavy loads is the main use of chain conveyors (very wide or very long items such as pallets, industrial containers, and grid boxes). In the automotive industry, chain conveyors transport vehicle parts through paint plants. They can also be found in the pharmaceutical industry. The difficulty with chain conveyors is that the sprockets need frequent replacement, which leads to prolonged downtime. Chains themselves are easy to maintain since individual links can easily be replaced. However, they are not easy to clean. They are not suitable for fine, powdered materials because they can accumulate in the links and lead to the breeding of bacteria. These systems also require a lot of power consumption. Pneumatic Conveyors There are four basic components to a pneumatic system: An air source A material feeding device A conveyor line An air-material separator Pneumatic conveyors are great for moving dry bulk materials through a vacuum (negative conditions) or air pressure (positive conditions). They transfer material through a tube (fully enclosed line) that reduces the chances of material loss. Fine, dry powders that are fluidizable are the best materials for pneumatic conveyors. Granular or pelletized materials are also acceptable. Here is what you can transfer via these systems: Sugar Coal fines Starch Wheat flour Sands Food products Metal powders, and more The advantages of air pressure or vacuum conveyors are that they require low maintenance and are flexible. Unfortunately, they are not the most energy-efficient. They also significantly damage delicate material – up to 10% of the conveyed product can be damaged by this system. Conclusion An industrial facility would not be able to function efficiently without material handling equipment. Conveyor systems can be found everywhere: in the chemical, pharmaceutical, automotive, aerospace, mining, bottling and canning, printing, packaging, and many other industries. A reliable system for transporting products and materials inside a distribution center or production facility is crucial for industrial processes. An industrial conveyor needs a power source to drive it. This can be electricity, gravity, or it can be manually driven. It can have a range of different modes of material handling, such as belts, rollers, buckets, cables, chains, etc. An industrial conveyor system also needs a support framework and controls for turning it on and off, adjusting its options, and potentially stopping it entirely in an emergency. Conveyors are not only beneficial for moving materials but also for storing and buffering them. Special types can also sort items. The most prevalent conveyor types are: Aero-Mechanical Auger (Screw) Belt Bucket Cable Chain Pneumatic To choose the right one for your company, you need to take into account several factors: what materials you're transporting, the floor space available, how much money you're willing to spend on power consumption, whether your conveyor will be a part of any assembly lines, how vital material integrity is to you, and so on. Designing the right conveyor layout can be an arduous task. If you'd like some help and are interested in tubular cable conveyors, why not reach out to Cablevey, a conveyor system manufacturer. Our experts will be glad to meet your business needs and help you lead your organization into the future of conveying technology! Source: Cablevey Conveyors
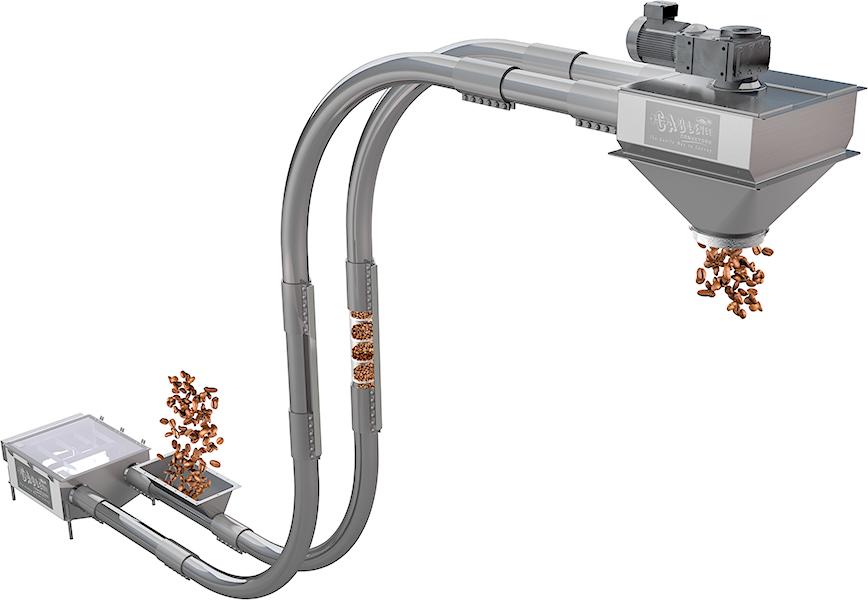
6+ MIN
28/04/2021
Boost Pet Food Value and Profit with Gentle Conveying Without Using Air
Tubular Cable Conveyors can significantly reduce product damage, energy use, noise, and maintenance. Pet Owners pampering their Dogs, Cats, and animal friends more than ever today, quality and presentation are being scrutinized. As a result, only tasteful whole product is desired--not crumbs, bits or powder. In today's competitive marketplace, unpresentable, broken Pet Food will be taken as a cue for low quality product, unsuitable for cherished pets, who are often treated like family members.To avoid turning off customers, product that is excessively broken or powdery must often be reduced, removed or filtered out, since this may be missed or rejected by the animals. Dealing with broken Pet Food product after production only adds to processing costs and reduces profit. 'Many high-value products can be fragile and need very gentle handling. Otherwise, whole forms can be broken, crushed to bits, and even turned to powder. This significantly lowers the value of the product, and damaged portions may need to be removed or disposed of to prevent perceived quality issues that could prompt customers to turn to other brands,' says Gary Schliebs, a Process Engineer and Director of Plus One Percent. Engineered Solutions, a consulting firm that works in the Food Industry and Markets Food Industry Conveyor equipment globally. 'In some cases, more than 10% of delicate product can be damaged by high velocity air-power systems. The cost to the industry is compounded because the damage often comes at the end of the process, after considerable value has been added, only to have it degraded by a poor choice in the selection of transfer conveying equipment,' adds Schliebs, who frequently consults on food engineering equipment design, plant layouts, and process flows. The Limitations of Air Conveyors In the Pet Food Industry, a wide range of fragile, high dollar value food products can be prone to excess breakage when conveyed at high velocity by air-power, such as in pneumatic and aeromechanical systems. Pneumatic Conveyor Systems utilize air by creating air pressure above or below the atmospheric level. These systems use filters that require regular replacement. The two main types of pneumatic conveyors – dilute phase and dense phase – differ by speed and pressure, and both can be configured as a pressure or vacuum system. In dilute phase conveying, pet food product is suspended in the air as it is transported through the conveying pipe at extremely high velocities of typically 3,400-5,000ft/min. While the product usually has minimal breakage during straight pathways, most systems have bends and sweeps where it can be forced through constricted areas, quickly change direction and be damaged. In such cases, valuable feed often can be too fragile. Dense phase Pneumatic Conveyor Systems, where the product is not suspended in air since it is heavy or abrasive, function at lower velocity than dilute phase. However, with air speeds of about 700-1,500ft/min., delicate food items are still susceptible to breakage at bends and sweeps. While aeromechanical conveyors have a different method of conveyance, these enclosed, high-capacity mechanical systems can also degrade delicate product. With these systems, a wire rope with evenly spaced discs within a tube travels at high speed, running in sprockets at each end of the conveyor. This generates an internal air stream traveling at the same high velocity as the discs that carry product along in the tube. However, these conveyors may also force vulnerable materials through stressful phases during transport, which could impair their integrity. 'Any fragile or friable food product conveyed at high velocity is prone to damage, particularly if it changes direction or exits with impact. This can be the case with both pneumatic or aeromechanical conveyors,' says Schliebs. A Gentler Approach Boosts Profitability According to Schliebs, a gentler alternative to protect sensitive, high-value pet food products is to utilize tubular cable conveyors. These systems move product through a sealed tube using a coated, flexible stainless-steel drag cable pulled through on a loop. Solid circular discs (flights) are attached to the cable, which push the product at low speed through the tube without the use of air, preserving product integrity and minimizing waste. 'Food Industry manufacturers can decrease product damage down to 1-2% with a slower process like a Cablevey Conveyors tubular cable system. With it, product is gently transferred at low speed, so there is minimal to no damage,' says Schliebs. Cablevey Conveyors is an Oskaloosa, Lowa based premium, specialty material moving, mechanical conveyor company that has designed, engineered, and serviced enclosed cable and disc tube conveyors for almost 50 years, and is in more than 66 countries. In the Food Industry, the conveyors are utilized for products such as pet food, nuts, cereal, coffee, snacks, beans, and seeds. The systems can convey up to 2000 cubic feet per hour (56m3/hr.) of flakes, pellets, shavings, crumbles, granules, regrind, chunks, parts, prills, and powders with numerous layouts using multiple inlets and outlets. Since the material is carried between the flights, it is also much easier to safely convey some sticky or easily compacted materials in a tubular cable conveyor than in air-powered conveying systems, where such materials can form plugs. 'With pneumatic or aero-mechanical conveying systems, any soft or sticky material can smear and adhere to surfaces, particularly at bends and sweeps that change direction, which is not an issue with tubular cable conveyors,' says Schliebs. According to Schliebs, the tubular cable conveyor's modular construction can also help reduce product damage by enabling it to slide out on a gentler gradient, rather than simply drop out, as is more typical with conveyors utilizing air. 'To minimize product damage, it is important for food industry manufacturers to not only transfer gently, but also get product in and out of the conveyor safely and gently as well. That is more achievable with a conveyor like Cablevey that allows product to slide down rather than drop out the end,' says Schliebs. In fact, most tubular cable conveyors have interchangeable components that allow the conveyor to be easily expanded or reconfigured to change the length, conveying path and the number of inlets and outlets. These modifications are more complex and time-consuming with a pneumatic conveying system because it has more components and electrical connections. Also, another bonus of the Cablevey systems is that the 'footprint' can be quite small compared to other conveyor systems, and that really helps with tight and compact manufacturing areas. 'Because of the 'bespoke' design of each Cablevey system for customer specific requirements, we can tailor the design to be very 'non-intrusive' in the work area and not hinder access for people and maintenance, as other systems can. This is a real bonus for safety, access and saving floor space, which is another cost to manufacturing,' said Schliebs. Less energy use, less noise Since pneumatic systems convey product at high velocity, this typically requires larger, power-hungry motors that run fans, blowers and rotary valves. In a dense phase system, a pressure tank requiring compressed air consumes additional power. In terms of noise level, pneumatic conveying systems also generate considerable noise. Aero-mechanical systems, running at high speed, generate considerable motor and disc noise as well. Given that smaller motors are used, tubular cable systems are quieter overall and utilize much less energy.'A low speed tubular cable system is quiet enough to easily have a conversation around it while it is running,' says Schliebs. 'In regards to energy, it utilizes about one-tenth that of pneumatic systems. For dense phase models, the electricity savings by using a tubular conveyor can be sizeable, with 1-year ROI in some cases.' For more info visit Source: Cablevey Conveyors
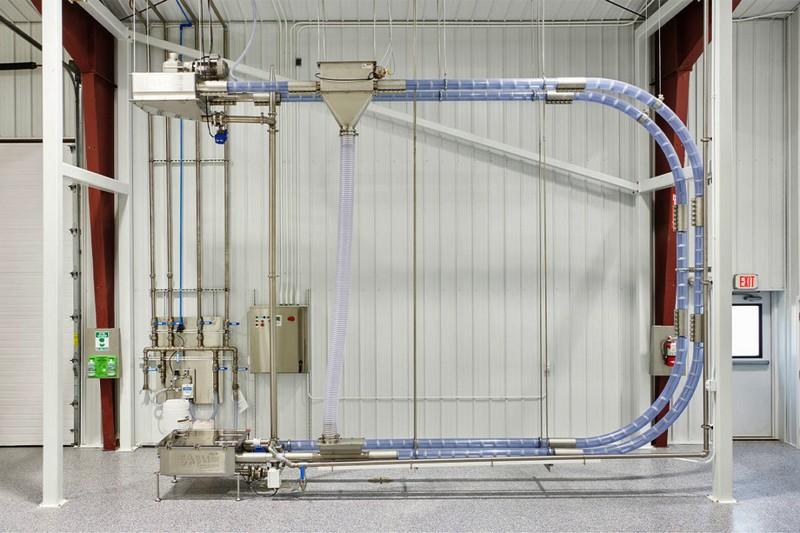
2+ MIN
17/12/2020
Interested on moving materials in a safe clean and efficient manner? Cablevey Tubular Drag Conveyor has the right Solution
Pet food manufacturers can maintain product quality and enhance processing by utilizing gentle tubular cable conveyors to transfer products throughout a processing plant. According to Cablevey Conveyors, tubular cable conveying helps maintain product integrity and minimizes fines, which reduces waste and helps keep the processing environment clean. Additionally, tubular conveying uses smaller motors and less energy.
'In the pet food industry, a wide range of fragile, high dollar value food products can be prone to excess breakage when conveyed at high velocity by air-power, such as in pneumatic and aeromechanical systems,' said Karl Seidel, marketing director. 'A more profitable alternative to protect sensitive, high-value pet food products is to utilize tubular cable conveyors, which move product through a sealed tube using a coated, flexible stainless-steel drag cable pulled through on a loop. Solid circular discs (flights) are attached to the cable, which push the product at low speed through the tube without the use of air, preserving product integrity and minimizing waste.'
According to the company, pet food industry manufacturers can decrease product damage down to 1-2% with a slower process such as a tubular cable system. Cablevey is a specialty material moving, mechanical conveyor company that has designed, engineered, and serviced enclosed cable and disc tube conveyors for almost 50 years, and is in more than 66 countries.
Cablevey systems can convey up to 2000 cubic feet per hour (56.6 meters per hour) of product with numerous layouts using multiple inlets and outlets. These systems can also significantly reduce energy use and noise. Pneumatic systems convey product at high velocity that typically requires larger motors that control fans, blowers and rotary valves. Aero-mechanical systems, running at high speed, can generate considerable motor and disc noise.
The smaller motors utilized by tubular cable systems require less energy and are typically quieter overall. According to Cablevey, a tubular cable system utilizes about one-tenth the energy used by pneumatic systems. In terms of noise, a low-speed tubular cable system is quiet enough to easily have a conversation around it while it is running, the company reports.
The enclosed tube conveyors help keep both materials and plant sanitary. Wet, dry and in-place cleaning options are available to reduce cleaning time, labor and required resources.
by Pet Food Processing