
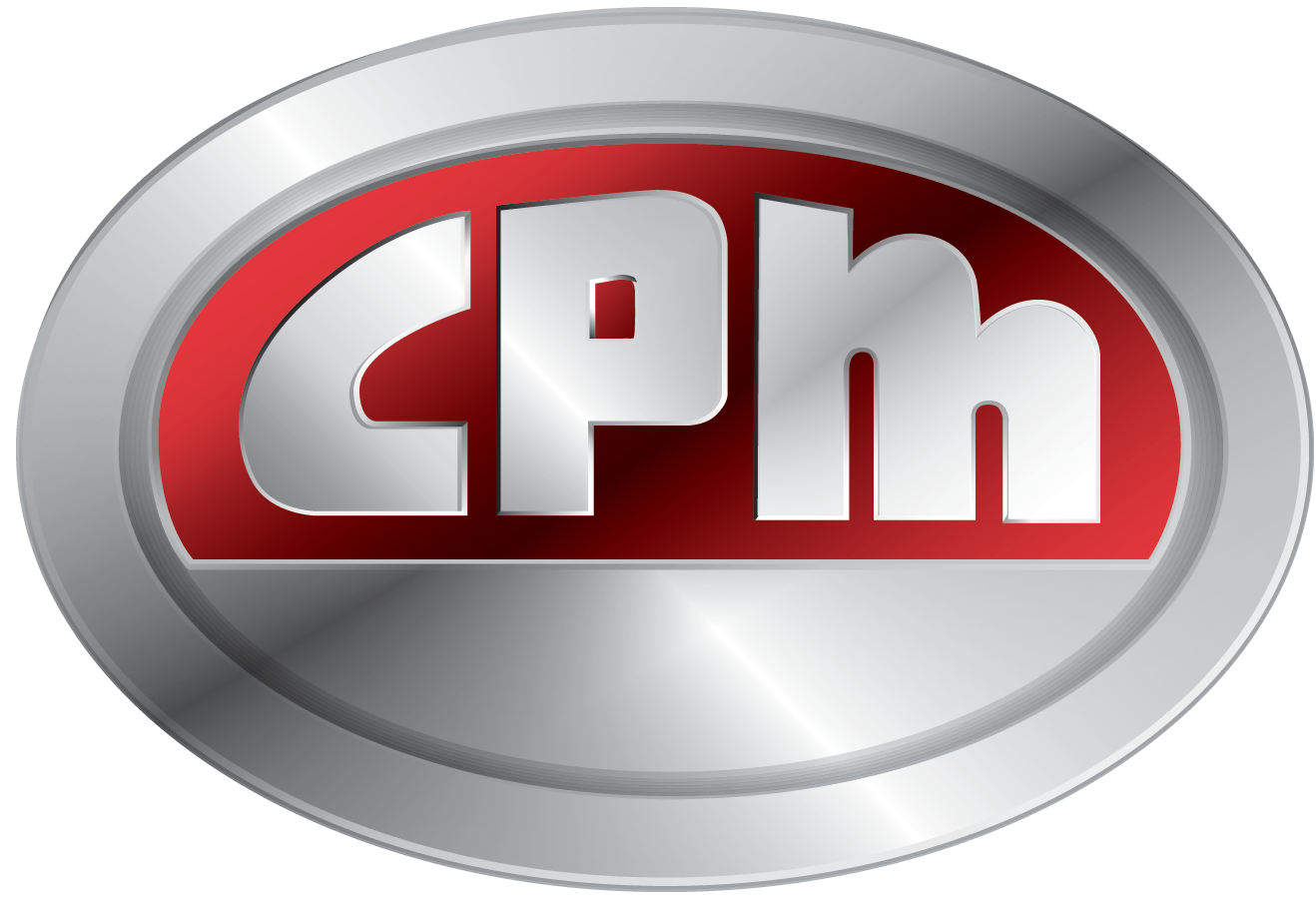
About the company
CPM is a leading industrial equipment and systems company.
Since 1883, CPM has pursued a singular focus…to deliver the very best processing solutions to help our customers succeed. Today we offer broad processing solutions and serve diverse industries including animal feed, oilseed, bioenergy, human food/snacks, engineered materials and many more.
CPM focuses on delivering customer value by serving our core industries with great products, excellent people and enviable business processes. We respect company heritage, we let leaders lead, and we align processes and resources to achieve new possibilities and growth.
How CPM delivers customer value:
- Premier operating equipment and services at the lowest total operating cost
- Industry best reliability and durability to maximize uptime
- Industry-leading product designs to optimize energy efficiency and product quality
- Superior application knowledge and global presence
- Exceptional customer service driven by engineering innovation, application support and maintenance advice
Products
Company News
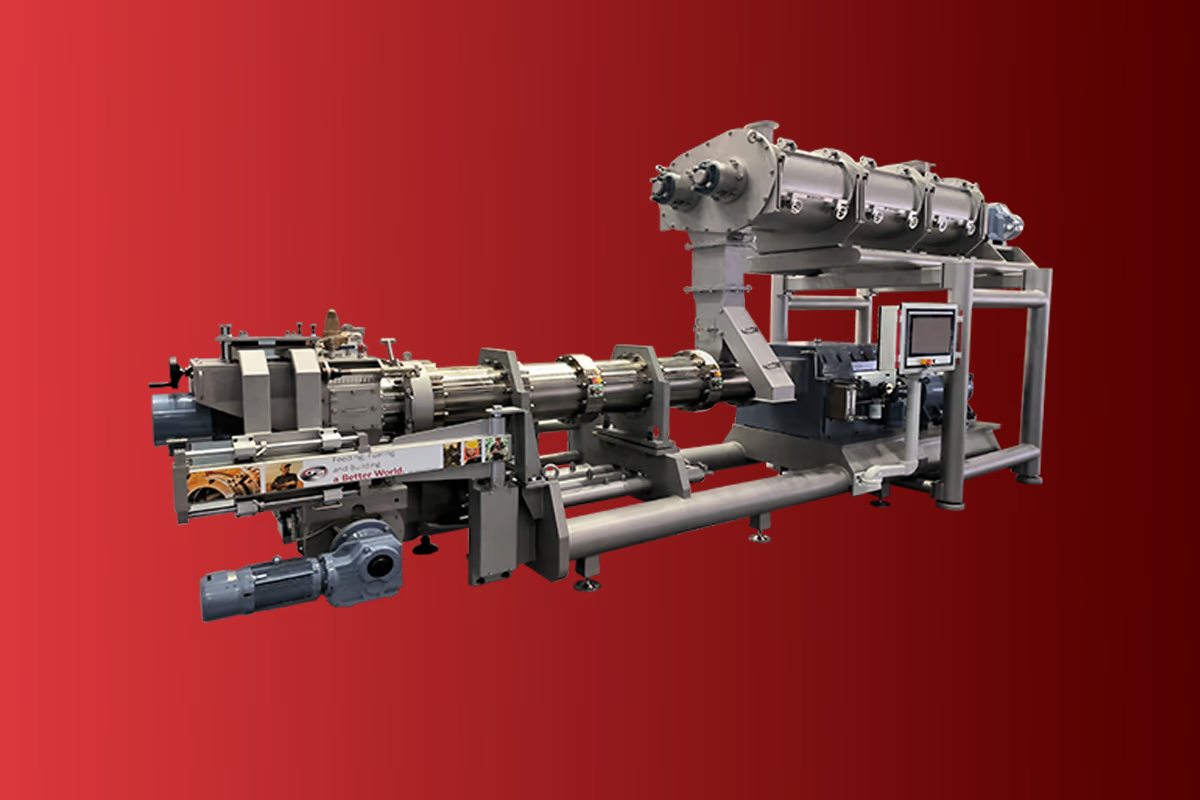
3+ MIN
11/03/2025
All in one - CPM Sees Growth in the Pet Food Industry for 2025
A Growing Market
Olivier expects the global pet food market to continue growing in 2025.
'We love our pets and owners are spending more on them than they ever have before,' Olivier said.
As the growth continues, CPM will be right there each step of the way.
'We are a one-stop shop for the customer,' he said. 'From your standalone solution to turnkey systems, that's where we're going, and it's a complete cycle with aftermarket and automation.'
Innovation at the Forefront
CPM is positioning itself as an innovative leader in the segment as well. One example is the use of a new permanent magnet synchronous motor in its extruder. Olivier said customers are already seeing the benefits from the design.
'Our motor is smaller than the typical motors out there, and has a stable torque with lower noise pollution,' he said.
The motor delivers up to 10% in energy savings, reduces noise pollution by 30% and is half the size of a typical motor in the pet food extrusion market, making it easier to transport and install.
Using Experience to Build the Future
Leveraging the years of experience from its family of brands, CPM is also in the process of developing a new dual-pass dryer and vacuum coater.
The dryer comes from Wolverine Proctor, which boasts more than 200 years of experience in the thermal industry and is a leader in the food processing sector. The vacuum coater is in production with IDAH, which is a leading shrimp feed equipment provider in Asia.
'We're really excited where this is going,' Olivier said. 'Our full lines include first dry kibble with capacities of 3, 5 and 10 tons per hour before expanding to other applications.'
CPM also offers hammermills, preconditioners and everything else on a pet food line.
Comprehensive Solutions
The equipment is designed and manufactured with the customer in mind. It's hygienically engineered and made to be durable and affordable. That includes spare parts and service for the lifetime of the equipment.
'Since we manufacture all of the parts, we control the process,' Olivier said. 'We have better control in-house; we know the equipment is durable. Plus, we're fast and flexible in making it.'
Reducing downtime, costs and errors is also a priority. CPM's automation solutions mean customers from a single location can receive, monitor, grind, batch and perform thermal control applications across their plant locations, all while backed by the industry's best applications and engineering support.
Looking Ahead
CPM has innovation centers strategically placed around the globe and expects the newest one to arrive in China in 2025.
'Our innovation centers really allow us to perfect our customers' processes so they can be confident that their product will be at its best with our equipment,' Olivier said.
For more information on what solutions CPM has for you, visit Pet Food | CPM
By CPM
Source: All Pet Food Magazine
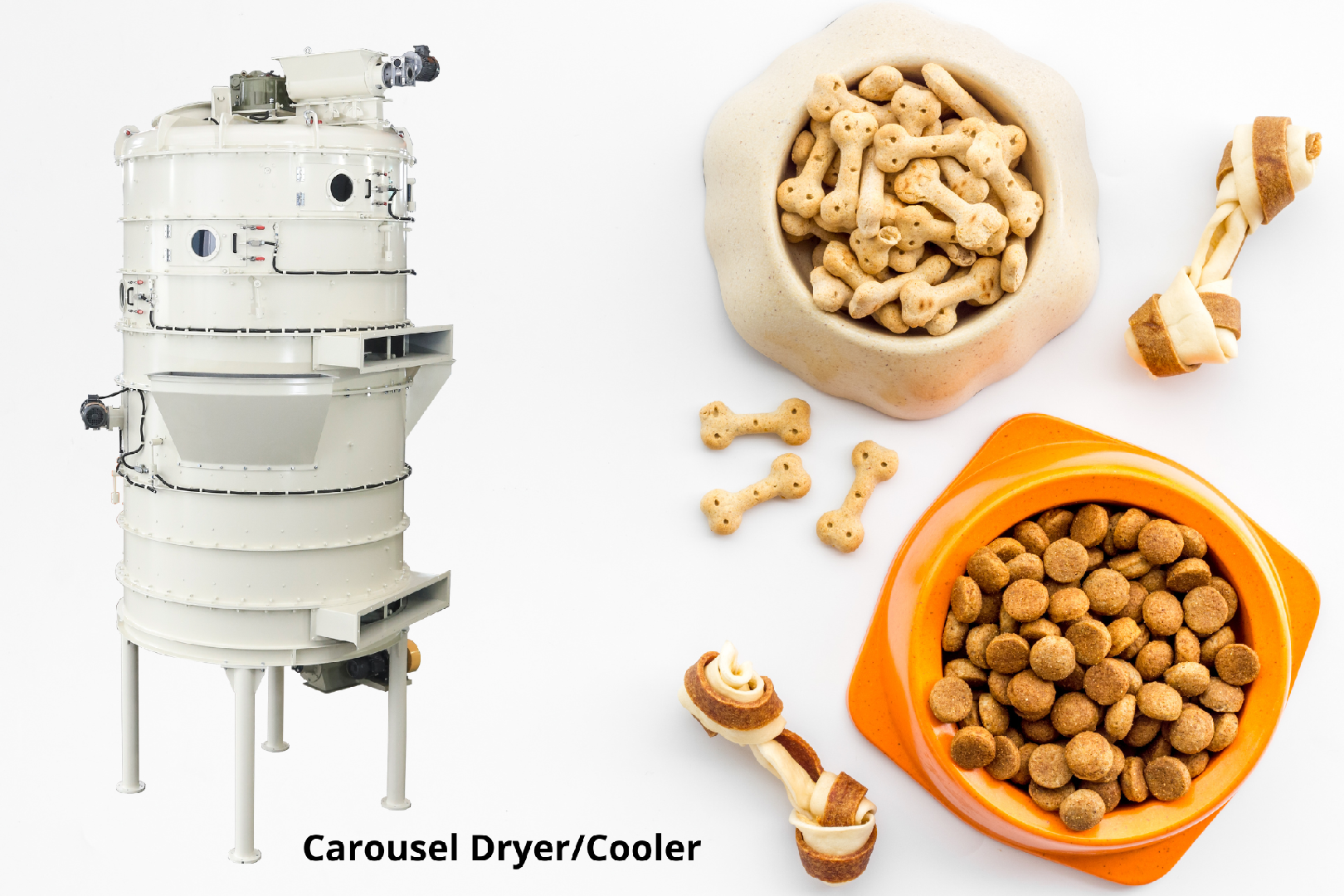
3+ MIN
21/08/2024
Carousel dryer/cooler from CPM's IDAH offers sustainability in petfood industry
The carousel working principle In the carousel dryer, the product enters through a rotary valve onto the revolving trays. The Carousel system ensures a first in, first out (FIFO) principle, after nearly one revolution, the product is gently discharged and mixed into the next lower tray. This process is repeated until the product drops from the last tray into the outlet where a rotary valve prevents air leakage. The revolution means that the product undergoes the same treatment all along the decks, ensuring that the product comes out in uniform moisture. Furthermore, the multiple tumbling action gives an efficient heat exchange with the air, resulting in a low dryer exhaust air temperature. Integrating dryer and cooler as one solution The Carousel technology is a unique solution for both energy efficiency and precise moisture control. Optimal moisture control is made easy by using carousel technology in both the dryer and cooler. Additionally, the exhaust air from the cooler can be directed as make-up air for the drying process. Therefore, an integration of the dryer and cooler into one compact machine with a FIFO discharge principle like the carousel dryer will give an outstanding moisture control performance. Ambient air cools the product and after filtered and heated it is used as drying air for the upper section. This carousel model offers many benefits and features when compared to traditional equipment. Improving product moisture control Managing the temperature and moisture content of the finished product is the main task for the drying and cooling process. However, when the feed is overdried, it causes material loss, as well as extra energy consumption. When the feed is too wet, the product will have a higher risk of quality degradation and mold growth. Due to its unique working principle, all the products in this carousel dryer will get the same heat treatment and retention time. This is combined with a unique and easy control system, along with real-time monitoring and modification of the drying parameters. The carousel dryer will give a uniform and constant moisture level that makes it easier to achieve the target average moisture, which will save energy and raw materials. Improving energy efficiency The drying and cooling process accounts for a significant part of the overall energy consumption. Rising energy costs and sustainability awareness regarding energy consumption have driven feed manufacturers to request further support to improve their drying and cooling functions. To maximize energy efficiency, we have to look into: Maximizing the use of warm product energy. Minimizing the amount of water evaporation. Minimizing energy loss with the exhaust air. By using the cooling air as makeup air into the dryer, the heat energy can be reused. Also, efficient heat exchange lowers the amount of exhaust air. Low exhaust air volumes will reduce the cost needed for odor treatment. Reducing the space required While upgrading the production capacity of a feed mill or improving the production process, the introduction of new equipment into the facility is required and space limitations may arise. The carousel dryer is already more compact than a typical dryer. Potential savings A direct result of using cooling air as makeup air for the dryer is savings. If you assume that the temperature differential between the ambient and cooler exhaust air is 25°C, you save up to 30 kg/t steam. At the same time, you will reduce the amount of exhaust air by 50%, reducing odor treatment costs significantly. Getting better moisture control, for example 0.5%, is saving not only about 10 kg/t steam consumption in the dryer but, even more importantly, saving 0.5% raw materials cost and having a 0.5% higher output capacity. For more information, contact [email protected]. Source: CPM IDAH
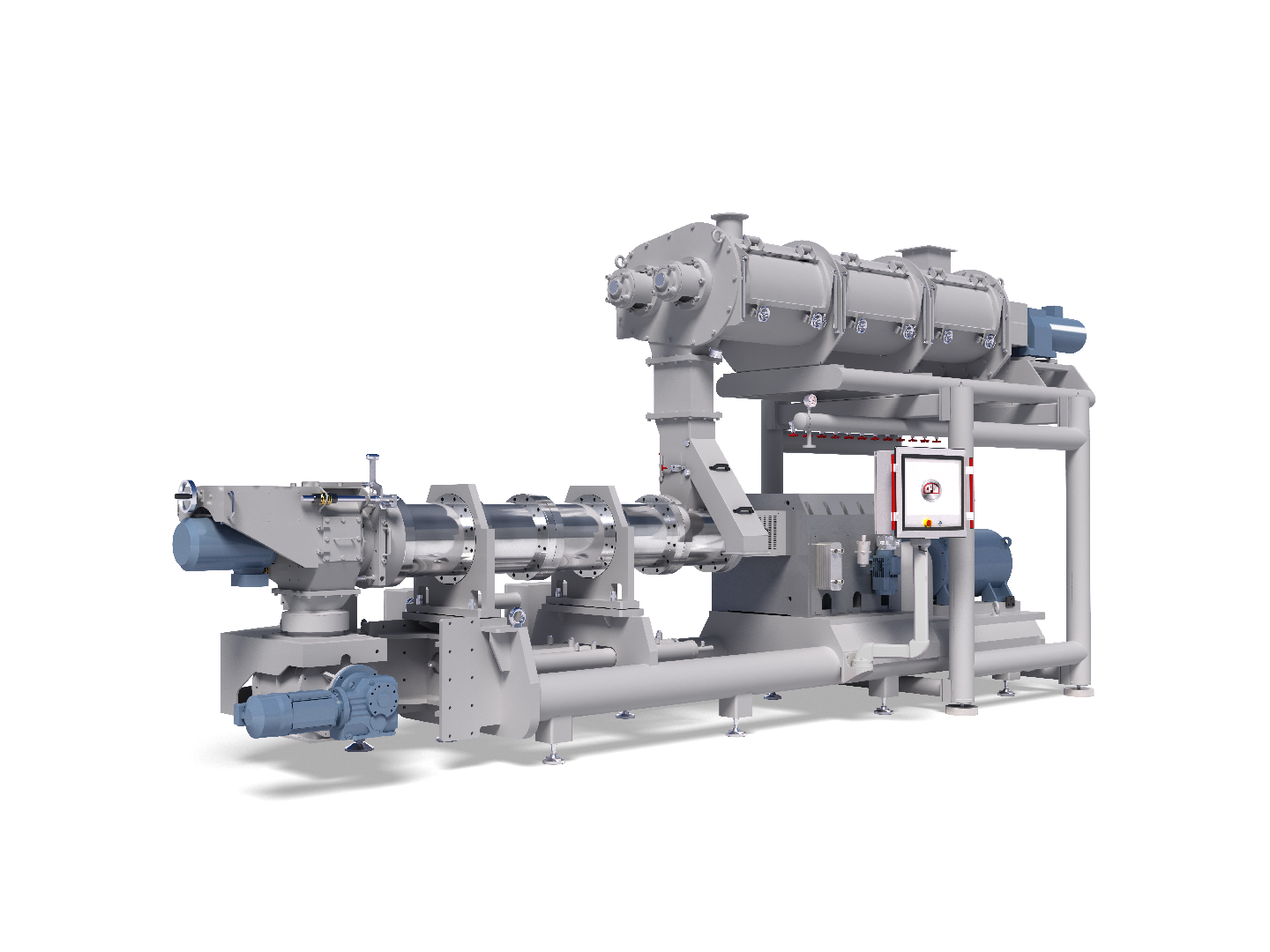
2+ MIN
18/06/2024
CPM IDAH presents the TwinTech extruder for the Pet Food and Aqua Feed market
In March, CPM IDAH presented the clearest evidence of that collaboration at the Victam Asia 2024 show: the new TwinTech twin-corotative screw extruder. This TwinTech extruder updates IDAH's well-known twin-screw extruder with innovations and design techniques from CPM Ruiya Extrusion, along with the long-lasting gearbox and energy-efficient motor from the renowned CPM equipment. Collaborative development "This extruder is the result of collaboration between the CPM brands IDAH (Taiwan) and Ruiya Extrusion (China)," says Ezequiel Villar, Business Development Manager for Latin America at CPM IDAH. "We combined their knowledge of design, robustness, and profitability with our knowledge of food production to introduce a new technology." The CPM gearbox and motor also offer real advantages in the TwinTech. 'The gearbox allows rotational speeds of up to 600 RPM, making it easier to process heavy loads and increase performance, along with a proven long service life,' says EV. TwinTech's CPM motor is a permanent magnet synchronous motor (PMSM), which offers significant advantages: "The CPM motor requires less energy," says EV. "It also reduces size and noise emission by approximately 30%." Combined, these innovations create a market-leading twin-screw extruder that delivers capacity, value, and reliability. TwinTech details The TwinTech extruder offers a range of new features developed by both IDAH and partner brands within CPM: Improved Gearbox technology: Powered by CPM's renowned and proven gearbox technology, the TwinTech extruder features a high-speed, heavy-duty gearbox capable of a rotational speed of up to 600 RPM. This allows for increased processing capacity and efficiency. Energy efficient design: The TwinTech extruder is powered by a permanent magnet synchronous motor (PMSM), which is highly efficient and approximately 50% smaller than traditional air-cooled motors. This motor design contributes to energy savings, reduced noise pollution (up to 30% less), and the option of water cooling to maintain the motor. Density control unit: An optional feature, the density control unit, allows TwinTech to produce different food types using the pressure inside the cutting chamber. This versatility allows manufacturers to produce a wide range of feeds with a single machine. Advanced preconditioning and cooking systems: These systems are designed to improve the cooking process by ensuring effective steam integration and retention, resulting in greater processing efficiency and product quality. Our CPM IDAH TwinTech extruder is a guaranteed solution to increase product quality levels with lower energy and wear costs. Regionally, we see an increase in consumption and specific growth in premium food by users, which generates the responsibility of the entire chain to have efficient solutions given the limitations that our clients face with the increase in ingredient, energy, and overhead costs. But despite these challenges, high-quality products are still expected to be supplied to a very competitive market. The TwinTech extruder is a cutting-edge solution that combines the experience of IDAH and the technology and robustness of CPM, offering the pet food industry a reliable and efficient tool. By: CPM IDAH Source: All Pet Food Magazine
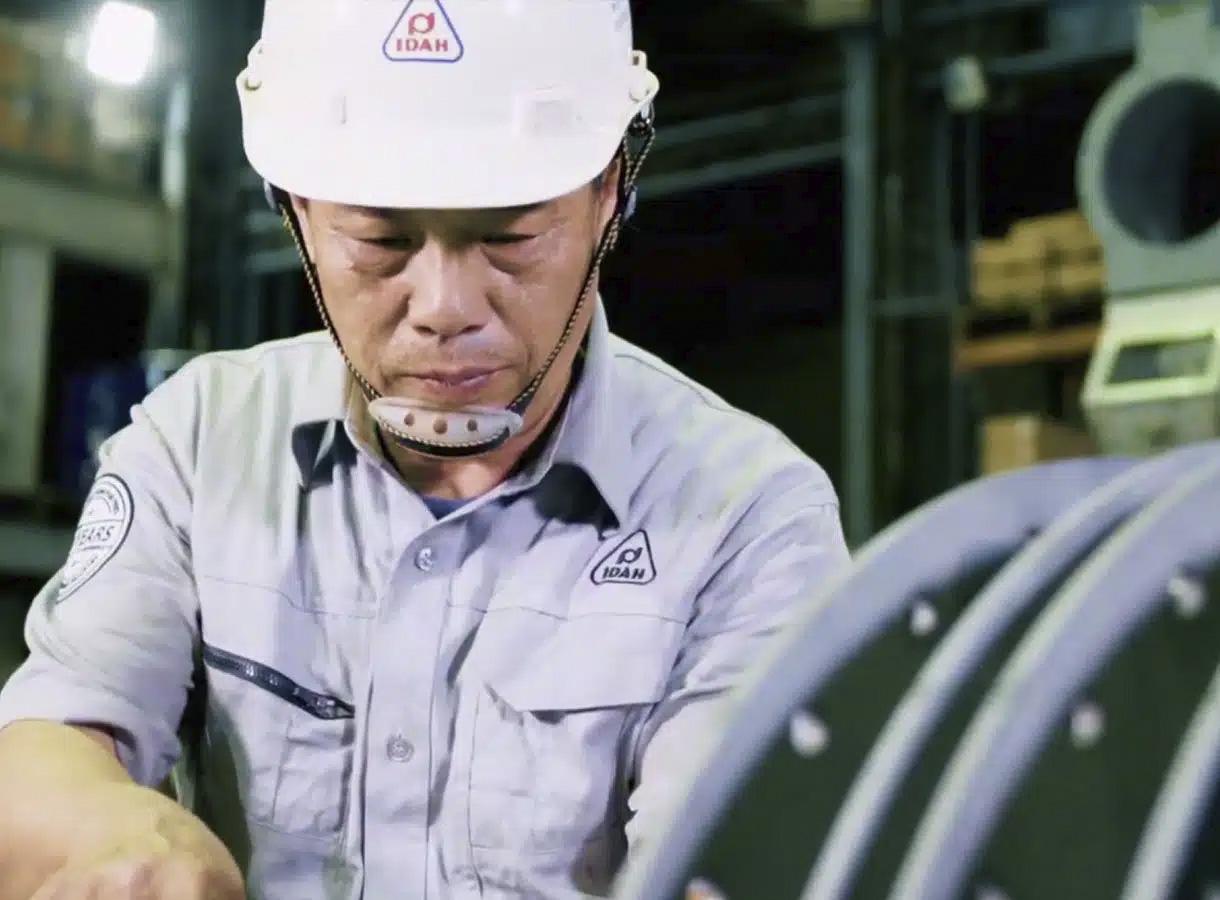
1+ MIN
10/07/2023
CPM renews its website and expands its range of solutions with the acquisition of IDAH
Regardless of the business unit or sector, all CPM brands aim to feed, promote, and build a better world for all its inhabitants. Now, thanks to a great redesign job, the company offers a space adapted to mobile devices, user-friendly, fast-loading, and easy navigation to be even closer to those who need their solutions. In addition, the acquisition of the company IDAH, which specialized in technological solutions for the food industry, has recently been announced, a movement that unites two industry leaders for the shared mission of feeding, promoting, and building a better world in a sustainable way. This movement allows CPM not only to enlarge its field of action but also to offer increasingly specific solutions to its clients and to seek growth and insertion in the Asian pet food markets, as well as to introduce this new brand in the Latin American industry. 'The joining of these two successful enterprises will bring a new dimension of solution and service offerings to our customers, thanks to the perfectly complementary nature of our product portfolios." David Webster, President & CEO at CPM. Thanks to this alliance, CPM increases its ability to adapt to the diversity of specifications that the industry currently requires. For now, it will primarily focus on the protein-based markets of aquafeed, pet food, and alternative protein. By: CPM Source: All Pet Food
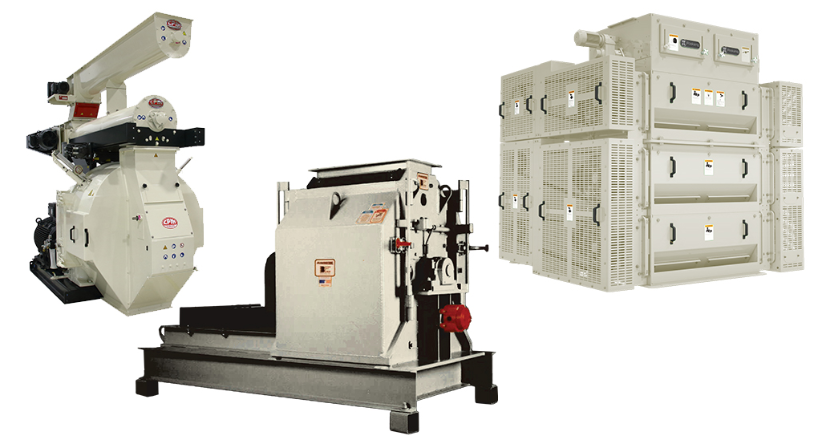
1+ MIN
23/12/2022
CPM Never Stops Evolving: New Colors Coming for CPM equipment
"The color change represents a step toward unifying our brand across the globe," said Maarten Visser, General Manager of CPM Americas/EMEA. "As CPM grows, our brand must evolve with it. We want our customers worldwide to associate the CPM name with the highest quality processing equipment available anywhere." "The new glossy white, accented with shiny black-gray, gives the equipment a sleek and modern new look. What's inside, Visser said, will not change at all". All types of CPM equipment are included in the upcoming color change, but existing orders will not be impacted. Equipment with the colors will be in the market later this year. About CPM - History The origin of CPM can be traced back to California's Napa Valley, where, in 1883, the Toulouse & Delorieux Co. manufactured presses, crushers and stemmers for winemakers. In 1931, the company created the first pellet mill, the 30 HP Flat Bed with stationary flat die, and we became California Pellet Mill (CPM). In the years that followed, we created more pellet mill models with additional features. In the 1980s, we greatly expanded our product offerings through the creation of Roskamp Champion with the acquisition of the Roskamp Roller Mill Company and Champion Hammermills. In 2002, Beta Raven, a leading supplier of feed mill automation and ingredient scaling systems, joined the team. To learn more about CPM products, click HERE. Source: CPM
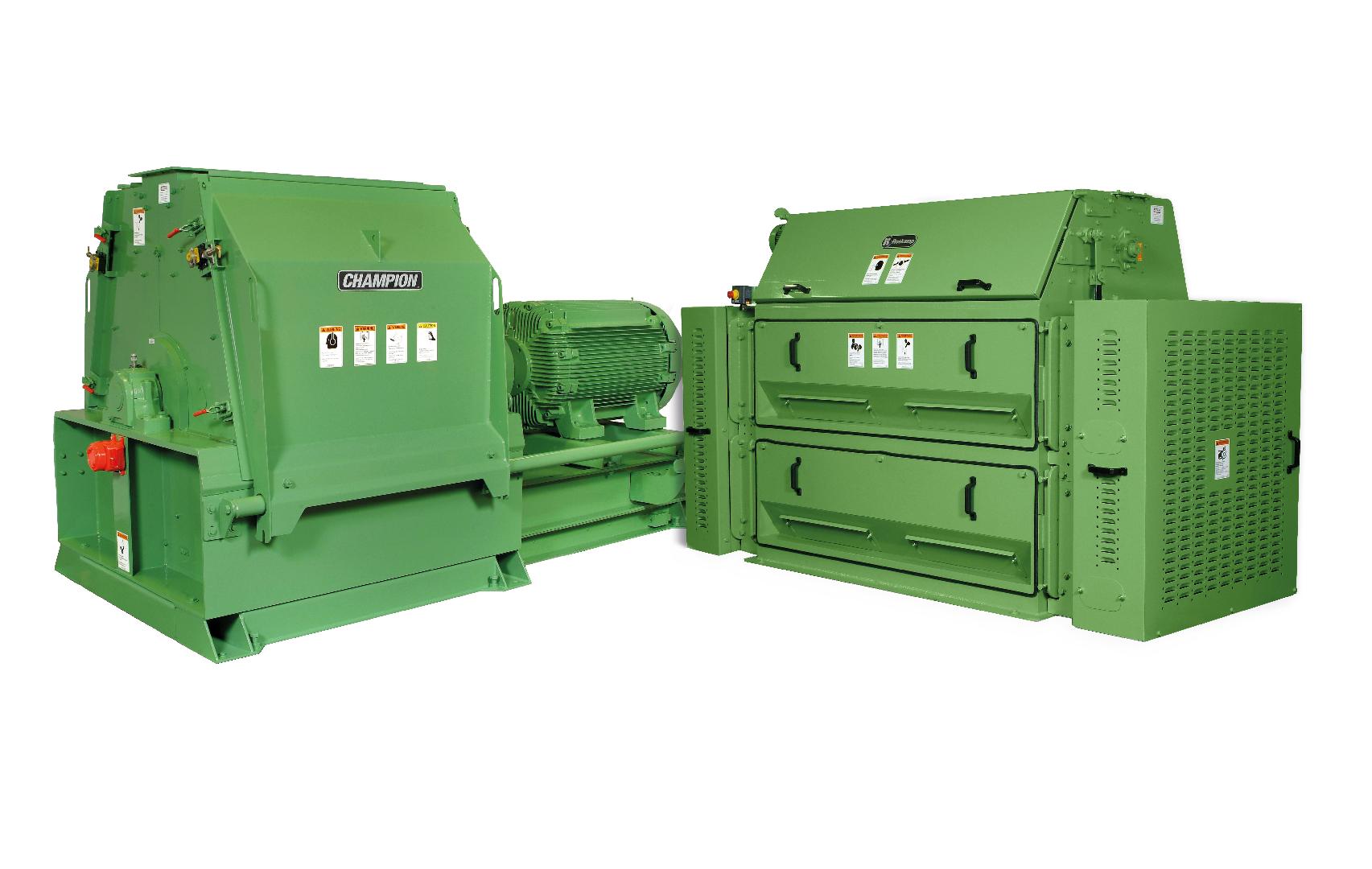
3+ MIN
13/12/2021
How can I grind more efficiently and with a smaller particle size standard deviation?
Series milling, in the simplest terms, is size reduction achieved in steps or stages. It usually incorporates two grinding machines: hammer mills and roller mills. The primary goal of step milling is to reduce the cost of producing one ton of finished ground product. Additional benefits may include better control of particle size distribution (more uniform grinding with fewer oversized and less fine particles), less heating of the product and subsequent loss of moisture, a reduction in maintenance cost per ton of ground material, potentially a finer finished product, and greater flexibility in the grinding circuit. Step milling process can employ two hammer mills, just one hammer mill and a roller mill, or two roller mills. If you want to use a single machine, your step milling circuit will involve batch processing, that is, grinding a coarse batch, resetting the machine for finer particles, and processing again. Circulation grinding can be an alternative way to stagger grinding without the use of multiple equipment. You can use multiple sets of rollers in the roller mill, or a continuous operation of a roller mill or hammer mill with a screening stage to return oversized materials for reprocessing. Circulation grinding offers the potential to reduce energy and improve particle size control, but does not add more flexibility than the traditional two-machine grinding system. Step milling or traditional series milling also allows the flexibility to continue milling product while maintenance or part replacement is performed on the other equipment. A second approach, and one that is employed in various feed mills, is the use of two "series" mills, one that performs a pre-break / break and the second that achieves the desired particle size. Advantages of this type of circuit include lower grinding costs, finer finished products, a more uniform particle size, and a greater capacity of the total grinding system. The main disadvantage of this type of system is the higher capital / investment costs required to purchase and install. In most cases, the investment in the additional equipment pays off in 6 to 12 months with the energy savings of the grinding circuit alone. Additional benefits, such as increased life of wear parts, spare parts, and equipment life, are a huge plus in addition to such energy savings. If you want to further improve your energy efficiency and reduce operating costs, the recommendation is to screen between stages: removing larger materials before secondary milling or reprocessing these large materials to the initial equipment. Using two roller mills and one screen can allow you the flexibility to remove out-of-spec product and increase throughput between machines. The step milling approach produces this energy reduction, which means that less energy is required because the materials are reduced more gradually over a slightly longer period of time. By doing the same amount of work (grinding) over a longer period of time (two or three gradual grinds instead of an instant grind), the total power requirement is reduced. The roller mill offers significant energy savings compared to a hammer mill when processing material in the coarsest particle size ranges. With these characteristics, the use of the roller mill as a pre-breaking or pre-breaking device can offer substantial savings in a typical grinding circuit. This combination of finer feed and higher hammer mill efficiency not only reduces energy cost when grinding, but also reduces other operating costs, including maintenance and parts. In some cases, existing hammermills require increased capacity; the addition of a roller mill can increase the hammer mill capacity by as much as 40 to 50%, without changing the average particle size of the grind. Source: CPM