
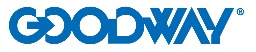
Goodway Tech
https://www.goodway.com/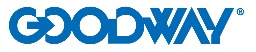
Goodway Tech
About the company
Goodway Technologies is a leading manufacturer and marketer of maintenance, cleaning, and sanitation products for the confectionary, food and beverage industry, HVAC, Energy, Maritime, Manufacturing, and more. Incorporated in 1966, with headquarters in Stamford, CT, and regional offices in Germany and Dubai.
Professional cleaning, sanitation, and maintenance personnel rely on our innovative products to clean and maintain production facilities, HVAC systems, plant machinery, hazardous material cleanup, surface cleaning and sanitation, and other critical industrial needs.
Our products are designed to help our customers overcome the cleaning, sanitation, and maintenance challenges they handle every day and deliver the benefits of immediate time and labour savings. We manufacture and ship from a 5,574 square-meter plant in Stamford, CT, USA, with additional regional support as needed.
Our solutions include ultra-low moisture dry steam cleaning systems and PureBelt® conveyor belt cleaners for food and beverage cleaning and sanitation professionals. These products remove soils, bacteria, allergens, and more in seconds for conveyor belt cleaning, production and packaging equipment, and more. Additionally, our speciality industrial vacuums are designed to pick up various materials from liquids to fine powders, and our BIOSPRAY® alcohol delivers system solutions deliver D2 rates sanitation liquids faster and safer than ever before.
For maintenance professionals, our products include tube cleaning systems, speciality industrial vacuums, cooling tower maintenance systems, descaling systems, coil cleaning products, hose & pipe cleaning systems, and more.