Our Approach
To start the audit, NorthWind's Team met with plant production leads and process experts from each area of the plant, including forecasting, planning, production, maintenance, information and technology, research and development, purchasing, distribution, and accounting, with the primary goal of gathering information about current operations and flow of data throughout the organization. These meetings helped the NorthWind team understand the existing infrastructure and identify focus points.
Information Gathering Focus Points
- Evaluation of current technological infrastructure
- Diagnosis of the level of automation and current digital methodologies
- Identification in areas of opportunities for improvement
- Manufacture's capabilities to integrate industry 4.0 technologies
- Review of current metrics on operational efficiencies and quality
- Evaluation of current metrics on safety and sustainability
- Review of current key performance indicators (KPIs)
After gathering the information NorthWind developed, in collaboration with plant personnel, an on-site agenda planned around production schedule and personnel availability. While on-site NorthWind identified and analyzed the existing gaps, deficits, and areas of opportunities with respect to the adoption of Industry 4.0 standards.
At the conclusion of the site visit, NorthWind developed a comprehensive report outlining the plant's digital transformation journey. The report included the current status of the manufacturing practices, diagnosis of areas of opportunity, and proposed an actionable plan with progressive milestones to fully achieve Industry 4.0 manufacturing standards.
Digital transformation recommendations
Below is a sample of the recommendations the NorthWind Team provided or discussed with the manufacturer based in the findings in the audit.
- Discussed the importance of a Raw Material Silo Inventory System.
- Reviewed Manual Documents that would benefit from a digital format.
- Recommended a replacement and modernization of the existing control system.
- Reviewed alternatives to implement seamless upstream and downstream equipment.
- Reviewed data collection and material tracking benefits for ingredients throughout the plant.
- Reviewed automation alternatives for Setpoint management for dosing raw material.
- Established Rework Integration Protocol on Production Line.
Marketplace
- Reviewed the benefits of automation for the Extrusion Process.
- Reviewed the benefits of automation for unloading finished product silos and provide material tracking.
- Proposed a data collection system in the packaging area by communicating with robotic arms, bagging machines, and using a barcode tracking system.
- Reviewed implementation of a Warehouse Management System (WMS).
- Increase cybersecurity of the plant control system.
The recommendations can be completed in phases, and the desired Industry 4.0 goals can be achieved with modernization of the process control system, MES Dashboards (Manufacturing Execution System), Digital Solutions (network architecture and topology), Integration with their ERP System, Cloud connectivity, and redundancy.
The impact
Based on the report's findings, the customer can expect the following Customer Benefits after implementing Industry 4.0 practices:
- Increased Efficiency: Automation and connectivity lead to streamlined processes, reducing downtime and enhancing productivity.
- Improved Quality: Advanced technologies such as machine learning and AI can monitor production quality in real-time, allowing for quicker adjustments and reducing defects.
- Greater Flexibility: Smart manufacturing systems can quickly adapt to changing market demands, enabling mass customization and shorter lead times.
- Enhanced Data Analytics: Industry 4.0 collects vast amounts of data, allowing manufacturers to gain insights into operations, customer preferences, and market trends for better decision-making.
- Cost Reduction: Optimized processes and predictive maintenance can lower operational costs through efficient resource utilization and reduced waste.
- Supply Chain Optimization: Real-time data sharing enhances collaboration across the supply chain, improving inventory management and reducing bottlenecks.
- Sustainability: More efficient energy use and reduced waste contribute to more sustainable manufacturing practices, aligning with environmental goals.
- Workforce Empowerment: Digital tools can enhance worker capabilities and safety by providing real-time information and training resources, fostering a more skilled workforce.
- Remote Monitoring and Management: IoT technologies facilitate remote oversight of manufacturing processes, enabling quicker responses to issues and greater operational control.
- Innovation benefits: The integration of advanced technologies encourages continuous innovation, allowing manufacturers to develop new products and services quickly.
The pet food manufacturer gained a clear, actionable roadmap for their digital transformation journey toward Industry 4.0. The comprehensive site audit provided valuable insights into their existing infrastructure, allowing them to identify key areas for improvement. With NorthWind's guidance, they now have a strategic plan to enhance efficiency, performance, and future scalability. As they implement these recommendations, they are well-positioned to optimize operations and stay ahead in an increasingly digital and automated industry.
Learn more about NorthWind's Solutions the Pet Food Industry or reach out to schedule a walk through of a system.
By Aldo Martínez
Source: NorthWind Technical Services
You could be interested: NorthWind: Smart Automation and Forward-Looking Vision for the Pet Food Industry
About company
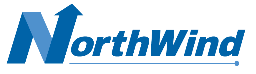
About company
NorthWind’s skilled team of engineers, programmers, and technicians have extensive process experience in addition to programming and design expertise in a wide range of industries.
NorthWind provides automation solutions for manufacturing facilities throughout the world. We also offer industrial electrical installation services in the USA.
Our headquarters is located in Sabetha, KS. The majority of employees and all panel fabrication activities are located at this facility. A second location was established in San Jose, Costa Rica in June of 2019 in order to better serve customers in Latin America. The Costa Rica office houses four employees that work in Service, Sales, and R&D.
Our skilled team of engineers, programmers, and technicians have extensive process experience in addition to programming and design expertise in a wide range of industries. The NorthWind PlantLOGIX™ software suite streamlines and simplifies programming, management, and maintenance of industrial processes while increasing visibility into what’s happening on the factory floor. State-of-the-art office technology and expertise allows NorthWind to provide programming and support services to clients anywhere in the world in a multitude of industries.
Our U.L. Listed control panel shop is located in a 10,000 sq. ft. climate-controlled facility that is fully-equipped to fabricate, test, and ship control panels of any size. High standards and advanced manufacturing technologies used by NorthWind ensure that control panels are delivered onsite on time and ready to be installed.
NorthWind strives to achieve high standards that meet customer needs and company stability. The company has been Control Systems Integrators Association (CSIA) certified since 2010 and continues to employ CSIA’s Best Practices and Benchmarks in order to provide the best value to its customers, combining technical proficiency with sound business practices.
NorthWind is also an accomplished Rockwell Automation Solution Partner, providing proven services and solutions that meet our customers’ automation needs. Finally, NorthWind was named CSIA Integrator of the Year in 2019, a prestigious national award given to controls system integrators that demonstrate cutting-edge technology and cost effective solutions for manufacturers