MES solutions replace traditional paper-based manufacturing procedures and implements a proactive approach to manufacturing execution. Sometimes manufacturers implement reporting functionalities that fall within the scope of MES and sometimes a full-scale MES solution is integrated across the entire plant. Regardless of the size of the solution, the results of implementing MES include decreased costs and increased support for continuous improvement and lean initiatives. MES is used in conjunction with ERP and SCADA systems, bridging the daily plant operations to the rest of the business.
Manufacturing Execution Systems can tie into existing batch management systems, such as BatchLOGIX®, and use the existing inventory and production information to give further insight into yield and production metrics. MES connects existing ERP systems, PLCs, and databases. The combined data from those sources can create unique metrics, reports and dashboards that streamline operations, improve productivity, and ensure quality. Using a versatile platform like Ignition Perspective, the capability exists to connect all those data sources, create flexible dashboards, custom reports, custom modules, and Ignition's platform is designed for mobile access.
REAL-TIME DATA
MES platforms provide real-time production information. This valuable information opens the door for quick production snapshots. Dashboards combine real time operating rates and statuses with features like historical run information and production goals. Doing this provides an efficient way for a user to quickly see production status and identify areas that need attention.
HISTORICAL DATA
With comprehensive access to plant-wide data, MES offers extensive reporting capabilities. This is another area where the Ignition platform is helpful. Leveraging Ignition's Reporting module, information can be gathered from all the different data sources (ERP, Control System, and SCADA) allowing for the creation of tailored reports that effectively convey data for analysis. Through Ignition's broad array of device drivers, information from data from all parts of the plant can be logged and displayed in a central location. Additionally, the Ad Hoc trending tool proves to be a valuable asset, facilitating easy trend analysis of data points from all sources and saving those trends for later analysis.
Marketplace
PERFORMANCE ANALYSIS
Centerlining includes adjustable thresholds for each device set the acceptability and alert levels for each indicator. Selected KPIs (key performance indicators) such as Right first time (RFT), Rework, Scrap, Process capability (Cpk), and Overall equipment effectiveness (OEE). With one click, the dashboard can provide a detailed analysis of causes of shutdowns and rejects, batch quality rates, and other production indicators.
COMMON MES FEATURES
With all this data, both real-time and historical, there are many different modules that can be implemented. The goals and priorities of each plant and workstation guide which modules should be implemented or if a custom module needs to be developed. Below is a list of common modules.
Scheduling
Provides a global view of the planned production orders. This module can include changeover information, anticipated production time, equipment and materials needed with specific job details to complete the order.
Work In Progress (WIP) Inventory Management
Track and manage inventory through the different stages of production. MES accomplishes this by helping management fine-tune forecasting by providing real-time inventory audits. With the connection to the ERP system and the control system, validating the inventory levels between the two systems is now automatic. This eliminates the need to manually verify inventory levels on the production floor with what is on the books. The system can also verify materials will arrive in time to complete orders by looking at the delivery data on purchase orders and running it against the upcoming production schedule.
Recipe Management
A recipe consists of a list of ingredients, ingredient amounts and sequence for combining those ingredients, and the amount to be made (batch size). Create consistency from product to product and run to run as well as make the best use of resources to minimize waste and streamline the manufacturing process.
Production Tracking and Dispatch
Manage the bidirectional flow of production data in real time between the ERP and the plant floor.
Lot Tracking and Tracing
From raw material receiving through final product, lot numbers are traced throughout the entire production facility. MES allows for quick recording of batches of raw material, semi-finished products, and finished products, utilizing product genealogy which tracks raw materials, equipment used, dates, quantities, lot, and serial numbers.
Quality management and Control
Manage the quality of manufacturing processes and units including quality deviations and exceptions. Integrate quality check reminders and recordings for QA. These can be as automatic as implementing density and moisture sensors or more manual with an alarm signaling the operator to complete quality assurance (QA) checks and record them in the system. Each records the information to the MES system for the QA team.
Preventive Maintenance
Optimize the planning of preventive maintenance operations to reduce the impact on manufacturing.
OVERCOMING COMMON CHALLENGES TO IMPLEMENTING MES
Implementing a Manufacturing Execution System is a large undertaking and to provide the best solution, collaboration between the integrator and the manufacturer must be frequent.
A common challenge is providing the right information and tools to the right audience. When developing dashboards and reports, it is very important to remember who is using the feature and what the goals and priorities are. An operator will want to see different metrics and widgets than someone in a management role. When developing dashboards and reports it is very important to remember who will be using the feature. Separate dashboards for different groups can be created, or widgets can be dynamically hidden/shown depending on the log in permissions and who is viewing the application.
Often facilities have used multiple integrators and software systems throughout the plant. This poses a challenge to gathering data in an accurate and efficient way, as there are a variety of sources. NorthWind maintains consistency wherever possible and keeps documentation on where metrics are pulled in from. Documentation is available straight from the MES project. The user can see a description of how a widget works and where the information is being pulled from, whether it is from BatchLOGIX database, a customer's existing ERP system, or a PLC Program.
A key to overcoming these challenges is to have open and effective communication with plant personnel to ensure there is clarity on what information is needed. This starts with setting a detailed scope for each area of the system to avoid unnecessary and potentially costly distractions. NorthWind provides a detailed design/development/deployment process and holds meetings with the customer throughout each stage to discuss the project progress and steps to be taken to reach the next stage.
Manufacturing execution systems identify inefficiencies and optimize production. This powerful system can be everything from Overall Equipment Efficiency (OEE) for one area of a plant to a fully integrated solution with a paperless plant floor and everything in between. Implementing these features takes deep process and control system knowledge and because every plant has different processes, machinery, KPIs, and process targets the best solution is going to be a tailored fit. At NorthWind we utilize production and process data for plant optimization with a manufacturing execution system developed for you, with you.
Learn more about NorthWind's MES Solution.
By: Sydney Bosworth
Source: NorthWind Technical Services
You could be interested: RBS Baked Pet Food Systems: Optimized, Automated Solutions for Baked Pet Treats and Baked Kibble (Part 2)
About company
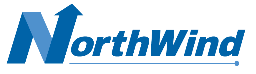
About company
NorthWind’s skilled team of engineers, programmers, and technicians have extensive process experience in addition to programming and design expertise in a wide range of industries.
NorthWind provides automation solutions for manufacturing facilities throughout the world. We also offer industrial electrical installation services in the USA.
Our headquarters is located in Sabetha, KS. The majority of employees and all panel fabrication activities are located at this facility. A second location was established in San Jose, Costa Rica in June of 2019 in order to better serve customers in Latin America. The Costa Rica office houses four employees that work in Service, Sales, and R&D.
Our skilled team of engineers, programmers, and technicians have extensive process experience in addition to programming and design expertise in a wide range of industries. The NorthWind PlantLOGIX™ software suite streamlines and simplifies programming, management, and maintenance of industrial processes while increasing visibility into what’s happening on the factory floor. State-of-the-art office technology and expertise allows NorthWind to provide programming and support services to clients anywhere in the world in a multitude of industries.
Our U.L. Listed control panel shop is located in a 10,000 sq. ft. climate-controlled facility that is fully-equipped to fabricate, test, and ship control panels of any size. High standards and advanced manufacturing technologies used by NorthWind ensure that control panels are delivered onsite on time and ready to be installed.
NorthWind strives to achieve high standards that meet customer needs and company stability. The company has been Control Systems Integrators Association (CSIA) certified since 2010 and continues to employ CSIA’s Best Practices and Benchmarks in order to provide the best value to its customers, combining technical proficiency with sound business practices.
NorthWind is also an accomplished Rockwell Automation Solution Partner, providing proven services and solutions that meet our customers’ automation needs. Finally, NorthWind was named CSIA Integrator of the Year in 2019, a prestigious national award given to controls system integrators that demonstrate cutting-edge technology and cost effective solutions for manufacturers