More 'humanised' pet foods have become available on the market and are becoming increasingly popular among pet owners, who want the very best, healthy meal options for their beloved pets.
We have seen a change in quality control in the pet food and meat rendering industries, with a heightened focus on product purity, including metal fragment control.
These industries tend to have high levels of metal contamination in their product, as the meat and bone meal product can be very abrasive to process and tends to wear down machinery more quickly than some other product types. The contamination can originate from various stages of processing, as well as from the product itself, so it is important to install metal fragment controls such as magnetic separators or metal detectors in various locations, and in particular, the most final stage in a processing line prior to packing.
How to know where to install magnetic separators?
Choosing a location for food magnets will depend on multiple factors. For example, the amount of metal contamination within the product can play a significant role, as this can affect any existing magnets in the processing line and their ability to collect and retain the contaminants. With a high level of metal contamination, a magnet that requires manual cleaning can get overloaded and 'short out', meaning that it cannot collect and retain more contamination. Any additional metal contamination can then flow past the overloaded magnet and remain in the product.
This highlights the importance of having upstream magnetic separators to offload the final magnets in food processing lines, especially ones that have a high level of metal contamination. The importance of cleaning magnets frequently also shouldn't be overlooked and should be a crucial step in manufacturing procedures.
Another example of a reason to install magnetic separators can be to protect machinery from damage caused by certain non-ferrous or ferrous metal contamination. Depending on the product and processing line, as well as the type of contamination, there are a number of magnetic separation solutions suited for the job.
The Magnattack® Magnetic Separation range for pet food has proven to be very effective in both dry and wet product applications. Let's have a look at each magnetic separation solution and the type of product each magnet is designed for:
Magnetic Separation Examples for Dry Pet Food Products
Magnattack® manufactures a number of magnetic separators for dry pet food processing applications.
Mag-Ram® Self-Cleaning Magnet
Marketplace
The Mag-Ram® Self-Cleaning Magnet has proven to be an amazing self-cleaning permanent magnet and metal fragment control solution for dry products and incoming raw materials such as MBM, protein meal, grain, final kibble, and more.
With the ability to configure the cleaning cycle to suit tonnage rates and contamination levels, the Mag-Ram® gives operators the ability to have the magnet frequently cleaned, and automatically.
This self-cleaning magnet requires zero downtime, with no need to stop production, which is a huge benefit for processors with products high in metal contamination that cannot stop production for frequent cleaning. The rotating magnetic rams ensure minimal product build-up and blockage, and the magnet design provides excellent product stream coverage.
Not only this, but the magnetic rams can be configured to be cleaned one at a time, meaning that your product stream remains covered by the other magnetic rams! You are truly going to want to add this self-cleaning magnetic separator to your materials handling equipment wish list!
Rapidclean® Grate Magnet in Housing
The Rapidclean® Grate Magnet overcomes issues associated with conventional magnetic grates, such as stainless steel sleeves, cleaning difficulties, jamming, safety issues, and more. This permanent magnet consists of open-ended magnetic bars, and once the magnetic drawer is opened, the cleaning is completed away from the product stream, using the Rapidclean® Cleaning Tool.
This grate magnet is designed for dry products, such as meals, powders, grain, and premixes.
Dual Round Nose Plate Magnet System
The Dual Round Nose Plate Magnet System is another industrial magnet design suited for pet food applications. This magnetic separator can be installed in applications processing chicken frames, whole muscle products, poultry, beef, lamb, venison, final meal products and more, prior to expensive processing machinery such as grinders, shredders, dicers, and emulsifiers.
In some applications, especially those with high tonnage and fast-flowing products, fragments can be brushed off plate magnets by the oncoming product and back into the product stream. To reduce this risk, Magnattack® has developed the RE80® Round Nose Plate Magnet. This system features a High-Intensity RE80® Bar Magnet at the end of a standard magnetic plate. The Separation Bar Magnet offers protection against dislodged fragments and prevents them from re-contaminating the food product. When metal fragments are collected by the Separation Bar, they are washed safely to the underside of the magnet and out of the path of oncoming product.
With the deep field capability of the magnetic plate added to the intensive coercive force of the Separation Bar, you gain far superior control over foreign metal pieces and increased protection against contamination.
Spherical Pneumatic Transfer Magnet
The Spherical Pneumatic Transfer Magnet is a powerful magnet designed for high-velocity blow, vacuum, gravity, and pneumatic transfer lines. This magnetic separator suits pneumatically conveyed powders, grains, premixes, and palatant products. The aerodynamic design of this Magnattack® system enables efficient extraction and retention of metal from high-velocity powder lines, without experiencing bulk density problems.
The Spherical Magnet is considered a more hygienic, powerful and superior alternative to traditional bullet-style and cartridge-style magnets.
Magnetic Separator for Wet Pet Food Products
Emulsion & Slurry Pipeline Separator
The Emulsion & Slurry Pipeline Separator is an inline liquid magnet that is ideal for viscous liquid applications including meat emulsions, meat slurries, and more.
It is often difficult to extract weakly magnetic fragments from viscous meat emulsions, slurries, and liquids. In answer to this problem, Magnattack® has developed a special hydro-dynamic magnet system specifically for this purpose. The units are an efficient and sanitary alternative to Liquid Trap/Finger Pot Magnets, which can also be heavy and difficult to clean properly.
This mince separator excels in these applications as it features our patented RE80®HT Acutex® Probe Magnets, which provide superior product-to-magnet contact and more efficient magnetic separation.
The lachrymiform (or 'tear drop') shape of the Acutex® Probe Magnets allow for very smooth transition of viscous products to move around the magnet with minimum resistance to flow. Maximum product to magnet coverage is achieved without causing leaks, blockages, and pressure problems.
The peak (or V-section) of the probe is faced towards the oncoming product stream, ensuring that collected magnetic fragments are washed to the back of the probe and safely retained until cleaning operations are underway. This feature greatly reduces the risk of recontamination caused by the impact of the product flow dislodging the collected fragments and reintroducing them back into the product stream.
We're here to help! Contact Magnattack® for a consultation, or book in a risk assessment to determine potential gaps in your foreign metal controls.
By: Magnattack
Source: All Pet Food Magazine
You could be interested: RBS Baked Pet Food Systems: Optimized, Automated Solutions for Baked Pet Treats and Baked Kibble (Part 2)
About company
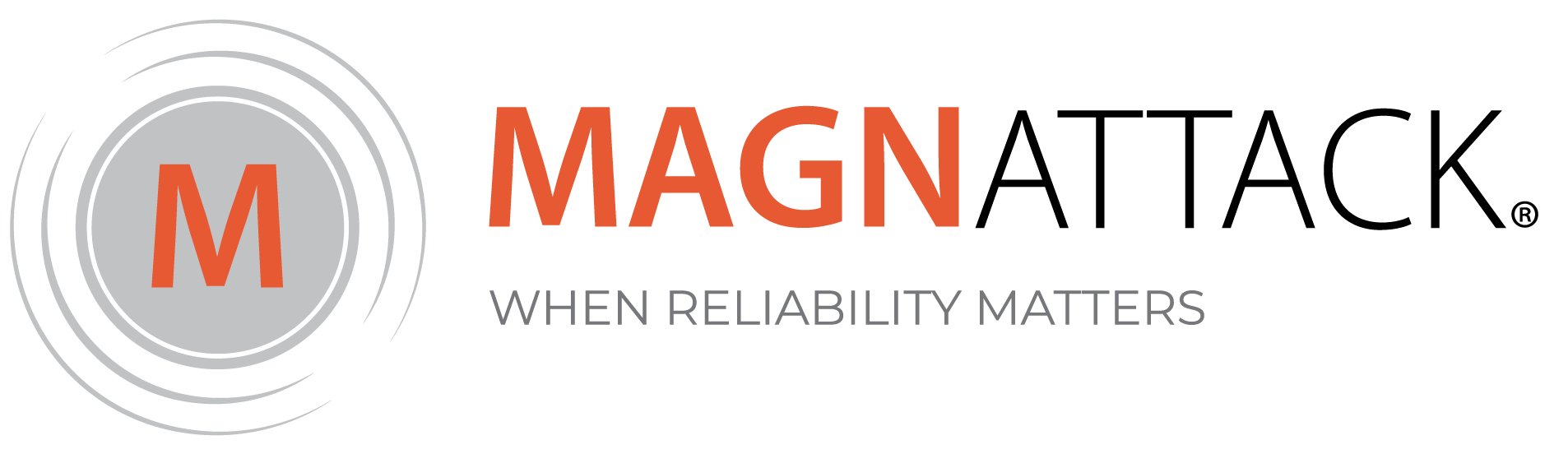
About company
About us
Magnattack Global is a family owned company founded in 1969. The main factory and headquarters are in NSW Australia, with offices in Minnesota USA and Bahia Blanca Argentina.
Our Job
Magnattack ® Global specializes in metal fragment control and magnetic separation solutions for the food processing industry worldwide. Our products fulfill the HACCP principles and help our clients to meet international standards, obtaining its certification and validation.
We offer solutions that allow our clients to achieve the following results:
- Reduce metal contamination risks.
- Cut equipment damage.
- Improve product purity and safety.
- Protect brand reputation.