The complexity of processing, from ingredient handling to packaging, introduces multiple stages where foreign metal fragments can enter the production line. Although many processors understand the importance of magnetic separators in enhancing food safety, uncertainty often arises about the most effective equipment placement for optimal product security and machinery protection.
Effective Placement of Magnetic Separators
Strategically placed magnetic separators is critical for ensuring pet food safety and quality. There are a few locations where installing magnets is most beneficial:
1. Product intakes: Magnetic separators at the product intake stage —for both dry and wet ingredients applications— are essential for removing metal fragments, such as magnetic stones and work-hardened stainless steel, safeguarding machinery, and ensuring incoming materials meet quality standards. This is an important magnet to ensure that the product coming into your process meets your requirements.
2. Post-first stage mixing/wet ingredients processing: After the initial mixing phase, magnetic separators help extract contaminants introduced during processing. This stage reduces the strain on final-stage magnets, especially in cases with high contamination levels.
3. Wet line before canning/packing: In wet pet food production, magnetic separators play a vital role in the canning stage. Proper consideration of flow rate, particle size, and viscosity ensures effective contaminant removal, protecting expensive equipment like twin-screw pumps while safeguarding the final product before packing and metal detection.
4. Dry ingredients processing: Magnet placement during dry ingredient processing depends on factors like flow rate and protection level. Installing separators before extrusion prevents contaminants from being embedded in kibble, streamlining quality control measures and reducing potential hits on final-stage magnets.
5. Dry line before bagging: The final magnet before bagging serves as the last defense against contaminants before products reach consumers. Certified and traceable magnets provide reliable quality assurance and help demonstrate effective preventive measures.
Choosing a magnetic separator for these applications will depend on the flow rate, density, speed, and more.
Top Magnattack® Magnetic Separators for Pet Food Applications
Robust food safety protocols are fundamental to ensuring nutritious and safe pet food while maintaining consumer trust. Product recalls are financially costly and damaging to brand reputation, making comprehensive quality control measures essential.
A single recall incident can impose a significant burden on a production plant, both in terms of product losses and the possible impact on the company's image, not to mention huge potential financial losses. It is critical for manufacturers to realize this risk and have comprehensive quality control measures in place.
The Magnattack expertise and range of magnetic separators can bolster your safety measures and give you peace of mind.
The Mag-Ram® Self-Cleaning Separator is an advanced solution that is highly effective for processing raw materials such as grain, protein meal, and meat and bone meal, as well as for dry ingredient handling and final stages before bagging. Its automatic self-cleaning functionality ensures rapid and efficient removal of ferrous metal contaminants, delivering exceptional performance, minimizing downtime, and maximizing productivity. Additionally, its dedicated contaminant chutes and pneumatic cylinders offer precise individual control, making it simpler than ever to maintain the integrity and purity of pet food products.
Marketplace
Additional innovative solutions include:
- Spherical Inline Pneumatic Transfer Magnet: Designed for pneumatically conveyed powders, grains, and premixes, this separator features an aerodynamic structure that eliminates sharp edges, ensuring smooth material flow without causing pressure fluctuations. Its unique magnetic field and strong retention capacity effectively manage high-velocity applications.
- Round Nose Plate Magnet: Typically placed before high-value processing equipment like grinders, shredders, dicers, and emulsifiers, this magnet is designed to extract and remove metal contaminants from applications involving chicken frames, whole muscle products, poultry, beef, and other materials. It is also highly effective in dry ingredient processing.
- Emulsion & Slurry Pipeline Separator: Specifically designed for viscous applications such as meat emulsions and slurries, this separator ensures the purity of slurry mixtures. Its' coned body eliminates pooling areas and air pockets, facilitating a smooth flow of liquid products. Additionally, its innovative design, including Acutex® Probes, strikes the perfect balance between magnet strength and open space, maximizing product-to-magnet contact for optimal efficiency.
- Rapidclean® Drawer Magnet: Specifically designed for dry ingredients such as meals, powders, grains, and premixes, this magnetic separator features large-diameter RE80® magnet bars to ensure maximum retention of even the tiniest, weakly magnetic fragments. It effectively collects and retains metallic particles from dry ingredients with precision. The Rapidclean cleaning feature allows for easy removal of contaminants without the need for direct magnet handling.
Mag-Ram Self-Cleaning Separator
Rapidclean Drawer Magnet
Magnattack®: A Trusted Partner in Pet Food Safety
With over 50 years of experience in the food processing industry, Magnattack® offers an innovative way to approach foreign metal control. Thanks to our cutting-edge technology and commitment to excellence, we've built a reputation as a trusted provider for pet food facilities worldwide. Don't compromise on the safety of your production process —explore our listing of metal separators for pet food applications today!
We are exhibiting at the Pet Food Forum in Kansas City, MO, USA. April 28-30, 2025 —visit us in booth #1602!
By Magnattack
Source: All Pet Food Magazine
You could be interested: RBS Baked Pet Food Systems: Optimized, Automated Solutions for Baked Pet Treats and Baked Kibble (Part 1)
About company
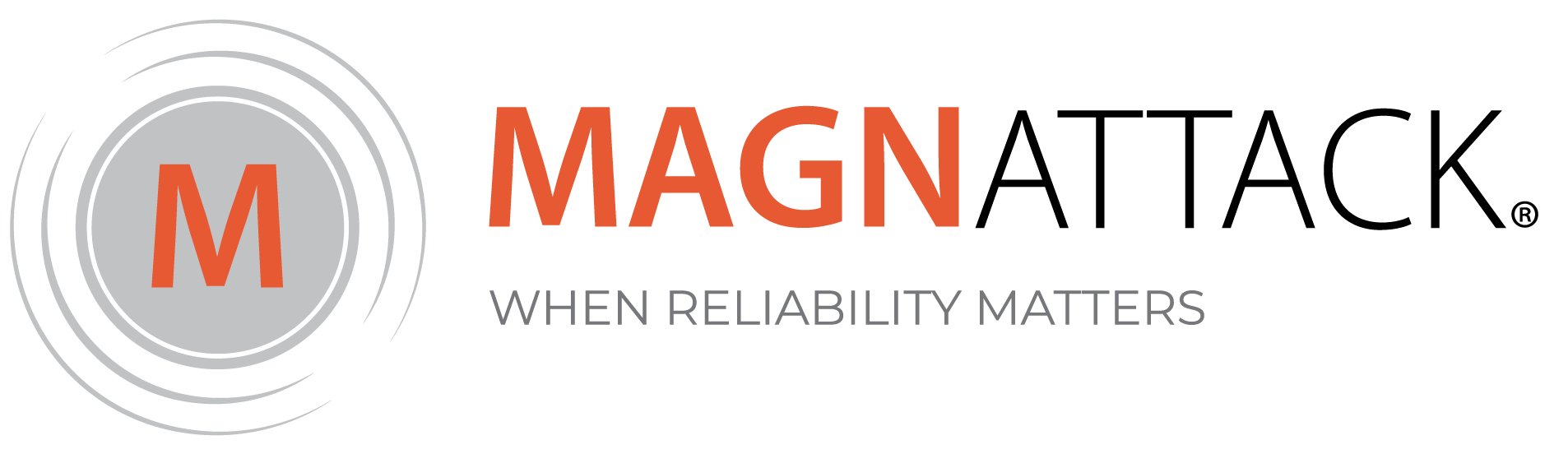
About company
About us
Magnattack Global is a family owned company founded in 1969. The main factory and headquarters are in NSW Australia, with offices in Minnesota USA and Bahia Blanca Argentina.
Our Job
Magnattack ® Global specializes in metal fragment control and magnetic separation solutions for the food processing industry worldwide. Our products fulfill the HACCP principles and help our clients to meet international standards, obtaining its certification and validation.
We offer solutions that allow our clients to achieve the following results:
- Reduce metal contamination risks.
- Cut equipment damage.
- Improve product purity and safety.
- Protect brand reputation.