
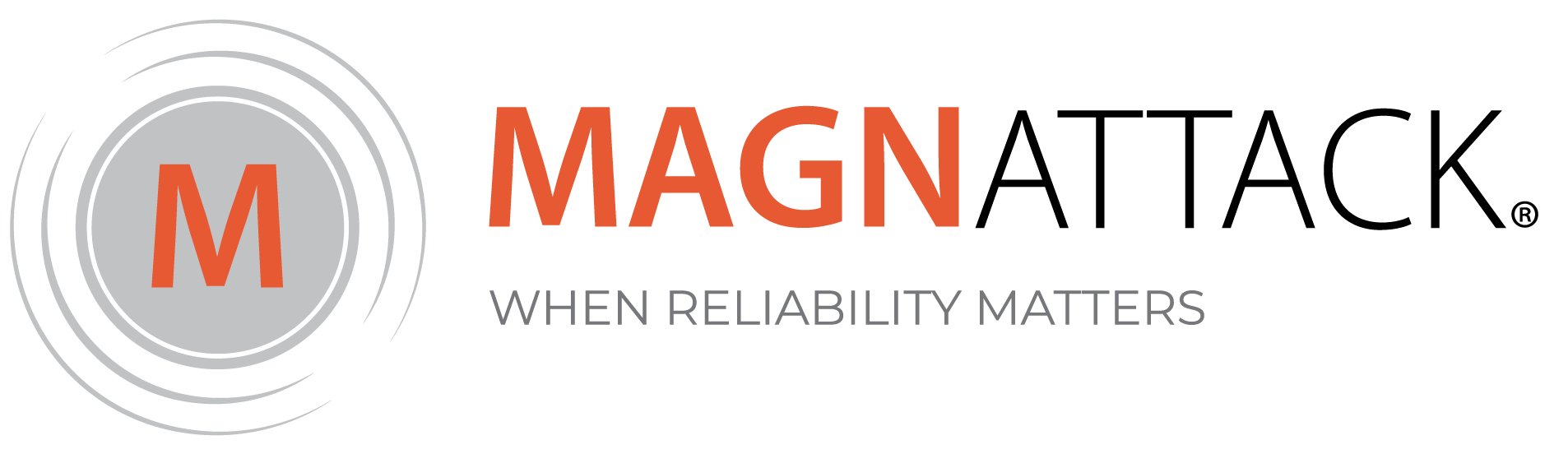
Magnattack Global
https://www.magnattackglobal.com/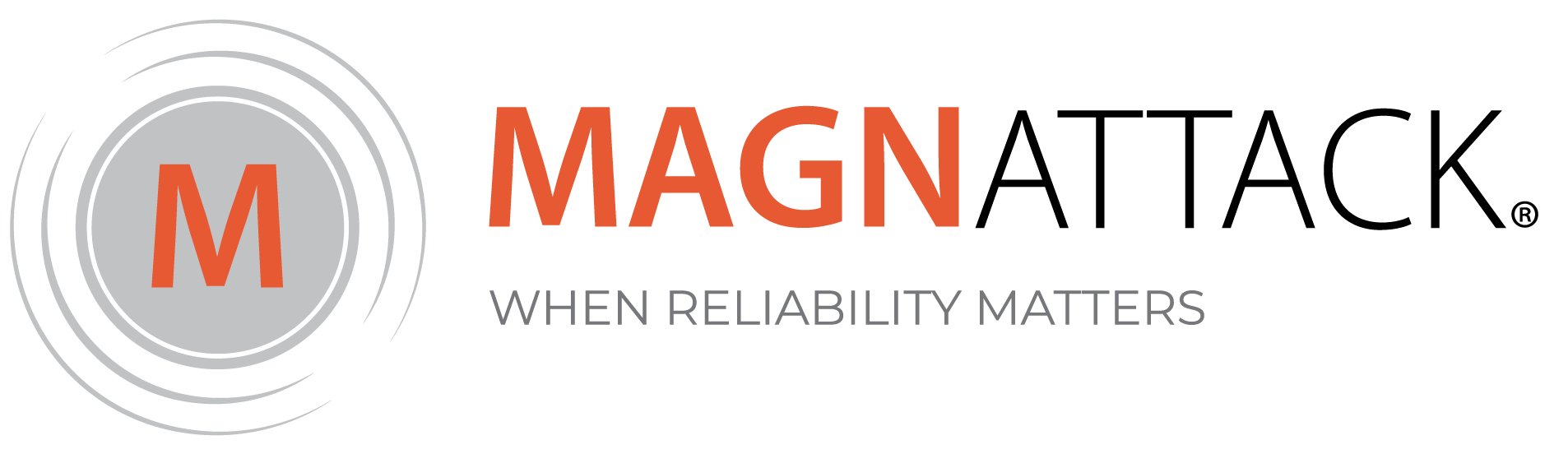
Magnattack Global
About the company
About us
Magnattack Global is a family owned company founded in 1969. The main factory and headquarters are in NSW Australia, with offices in Minnesota USA and Bahia Blanca Argentina.
Our Job
Magnattack ® Global specializes in metal fragment control and magnetic separation solutions for the food processing industry worldwide. Our products fulfill the HACCP principles and help our clients to meet international standards, obtaining its certification and validation.
We offer solutions that allow our clients to achieve the following results:
- Reduce metal contamination risks.
- Cut equipment damage.
- Improve product purity and safety.
- Protect brand reputation.
Products
Company News
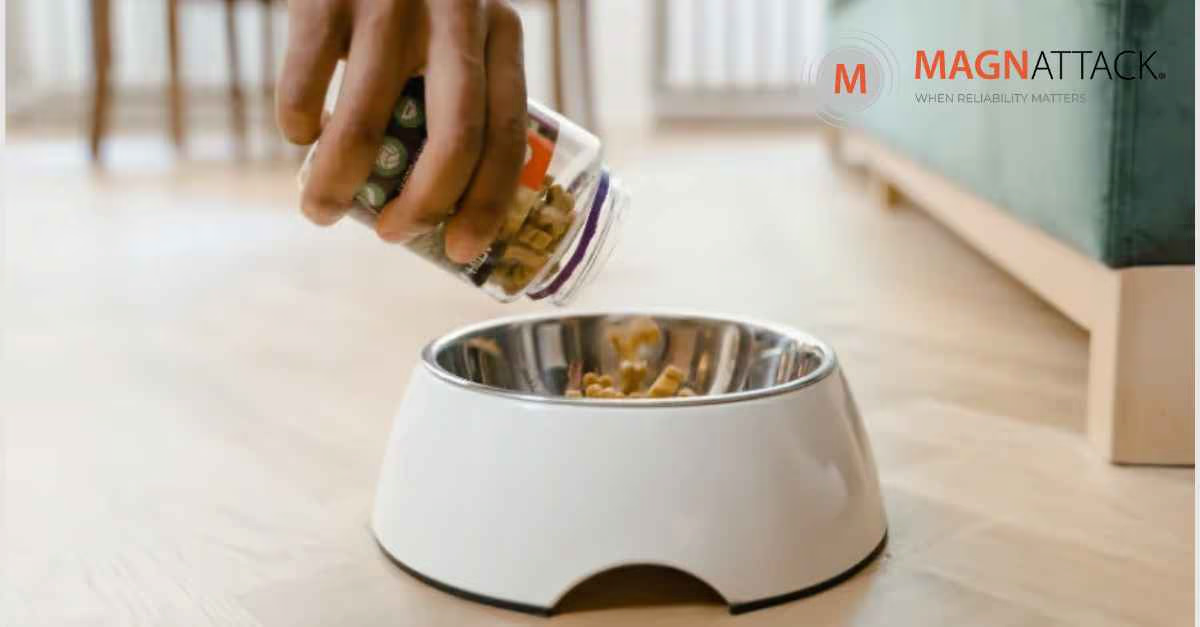
5+ MIN
12/08/2025
The Hidden Costs of Metal Contamination in Pet Food Processing (And How to Prevent It)
While the dangers of metal fragments in food products are well known, the true financial consequences of contamination are not always apparent until it's too late. From massive product recalls and reputational damage to regulatory fines and equipment failure, the hidden costs of metal contamination can cripple a pet food business. Fortunately, there are proven, cost-effective solutions to mitigate these risks—magnetic separation being one of the most powerful.
Let's explore the full scope of metal contamination in pet food processing, why it matters more than ever, and how preventive strategies can safeguard your operations and reputation in the long term.
Why Metal Contamination Is a Major Issue in Pet Food Processing
Pet food manufacturers operate in highly regulated environments with strict standards for hygiene, ingredient integrity, and traceability. Even minor lapses in contamination control can have serious repercussions.
Metal contamination typically occurs from three sources:
Processing Equipment Wear and Tear: As machinery components degrade over time, they can release tiny metal shards into the product stream, often going unnoticed until damage or contamination is discovered further downstream.
Raw Material Contamination: Ingredients may already be compromised before they enter your facility. If these materials are not adequately tested and filtered, they pose a direct contamination risk.
Operator Error or Maintenance Failures: Human oversight and inadequate maintenance can contribute significantly to contamination events, especially when production is scaled or rushed to meet deadlines.
In pet food production, metal contaminants are not only a physical hazard—they're also a financial and regulatory liability. Detection of even trace amounts of metal can trigger a cascade of consequences that reach far beyond the immediate scope of product loss.
Additionally, the risk of contamination extends beyond just the batch in question. It can affect adjacent product lines, raise questions about facility-wide hygiene standards, and lead to extensive investigations that can shut down operations for days or weeks.
The Hidden Costs of Contamination Incidents
Contamination incidents are far more than isolated quality control failures—they're events that can shake the foundation of a business.
Here's a breakdown of the most significant hidden costs:
Product Recalls and Brand Damage
A recall not only incurs direct costs like logistics, product disposal, and communication efforts—it also significantly damages brand trust. In a crowded market, pet owners are highly sensitive to safety issues, and negative press can lead to permanent customer loss.
The effects of a recall often ripple outward. Retailers may pull other products from shelves. Distributors may hesitate to place new orders. And consumer trust, once lost, is extremely difficult to rebuild. The long-term revenue losses from a single incident can exceed the immediate costs of recall logistics.
Lawsuits and Liability Risks
Contaminated pet food can cause serious harm to animals, potentially resulting in legal action from pet owners. Lawsuits may lead to costly settlements and additional regulatory scrutiny. Beyond financial penalties, the damage to your company's public image can be immeasurable.
Class action lawsuits, especially those amplified by media coverage, can linger for years. The legal fees alone can cripple smaller manufacturers, and settlements or judgments can force businesses to restructure or even shutter completely.
Equipment Damage and Downtime
Undetected metal fragments can harm processing machinery, leading to expensive repairs, unplanned downtime, and lost productivity. In high-output environments, even a few hours offline can result in massive financial setbacks.
Additionally, damaged machinery might not be caught immediately, which means ongoing inefficiencies, potential product quality issues, and cascading maintenance problems that compound over time. Predictive maintenance is critical, but so is source-level prevention.
Regulatory Fines and Compliance Penalties
Government and industry regulators take contamination incidents seriously. Failing inspections or breaching compliance can result in fines, suspension of licenses, or mandatory facility upgrades.
Compliance failures often lead to increased scrutiny, with agencies requiring regular audits, additional certifications, and costly infrastructure changes. In some markets, repeated non-compliance can even result in a ban on selling products.
Together, these hidden costs can snowball, creating long-term financial stress that compromises competitiveness and sustainability.
How Magnetic Separation Reduces Contamination Risks and Costs
Preventing contamination is always more cost-effective than managing the aftermath. One of the most efficient and scalable methods of protection is magnetic separation.
Magnetic separators work by removing ferrous and work-hardened stainless steel particles from the product stream before they reach downstream equipment or packaging. These systems are designed to capture even the smallest metal contaminants, reducing the likelihood of product recalls and equipment failure.
For pet food manufacturers, implementing magnetic separation offers several key benefits:
Increased Product Purity: Fewer contaminants mean higher product quality and consistency.
Compliance Assurance: Meet or exceed industry safety standards with minimal manual oversight.
Operational Efficiency: Minimize unplanned downtime due to equipment damage or by utilizing self-cleaning or easy-clean magnet designs.
Brand Protection: Proactively significantly reduce risks that could lead to recalls and customer backlash and complaints.
Furthermore, advanced magnetic separation technology is now available with features such as automated cleaning, data logging for compliance, and customizable designs to fit unique processing lines. This adaptability makes it easier than ever to implement without sacrificing throughput.
Best Practices for Contamination Prevention in Pet Food Processing
Beyond magnetic separation, pet food manufacturers should embrace a comprehensive contamination prevention strategy. Here are some best practices to consider:
Supplier Quality Control: Partner with trusted suppliers who provide certification and regular testing for raw materials. Implement incoming goods inspection protocols to catch contaminants early.
Routine Equipment Maintenance: Schedule regular inspections and servicing to prevent metal wear and fragment release. Include predictive maintenance tools to anticipate component failures.
Employee Training: Educate staff on contamination risks and procedures to ensure consistent handling and processing. Regular refreshers can ensure that safety practices remain at the forefront of people's minds.
Integrated Detection Systems: Use metal detectors and X-ray systems alongside magnetic separators for layered defense. Ensure these systems are calibrated and tested frequently.
Audit and Review: Conduct regular audits of your contamination control systems and processes to identify gaps and improvements. Use data to refine and optimize protocols over time.
Documentation and Traceability: Maintain detailed records of inspection, testing, and maintenance activities. Good documentation supports compliance and helps quickly identify root causes in the event of contamination.
Proactive contamination management strengthens food safety protocols, enhances brand integrity, and increases customer confidence.
Magnattack® Magnetic Separators for Pet Food Safety
At Magnattack, we specialize in magnetic separation systems engineered specifically for the demands of pet food processing. Our solutions are designed to help manufacturers control risks of potentially serious metal contamination events before they become costly problems.
With over 50 years of experience, our range of sanitary-grade magnetic separators includes:
Rapidclean® Drawer Magnets for dry ingredient and powder applications
Spherical Inline Pneumatic Transfer Magnets for pneumatic transfer lines
Mag-Ram® Self-Cleaning Magnets for continuous production environments and dry ingredients
Emulsion & Slurry Pipeline Separators and Pressure Pipeline Separators for wet emulsion, slurry and liquid products
Each unit is crafted to meet strict food safety standards, minimize risk, and support efficient operations without compromising throughput. Our team of experts provides full technical support, including site assessments, system customization, and ongoing compliance documentation.
Source: Magnattack
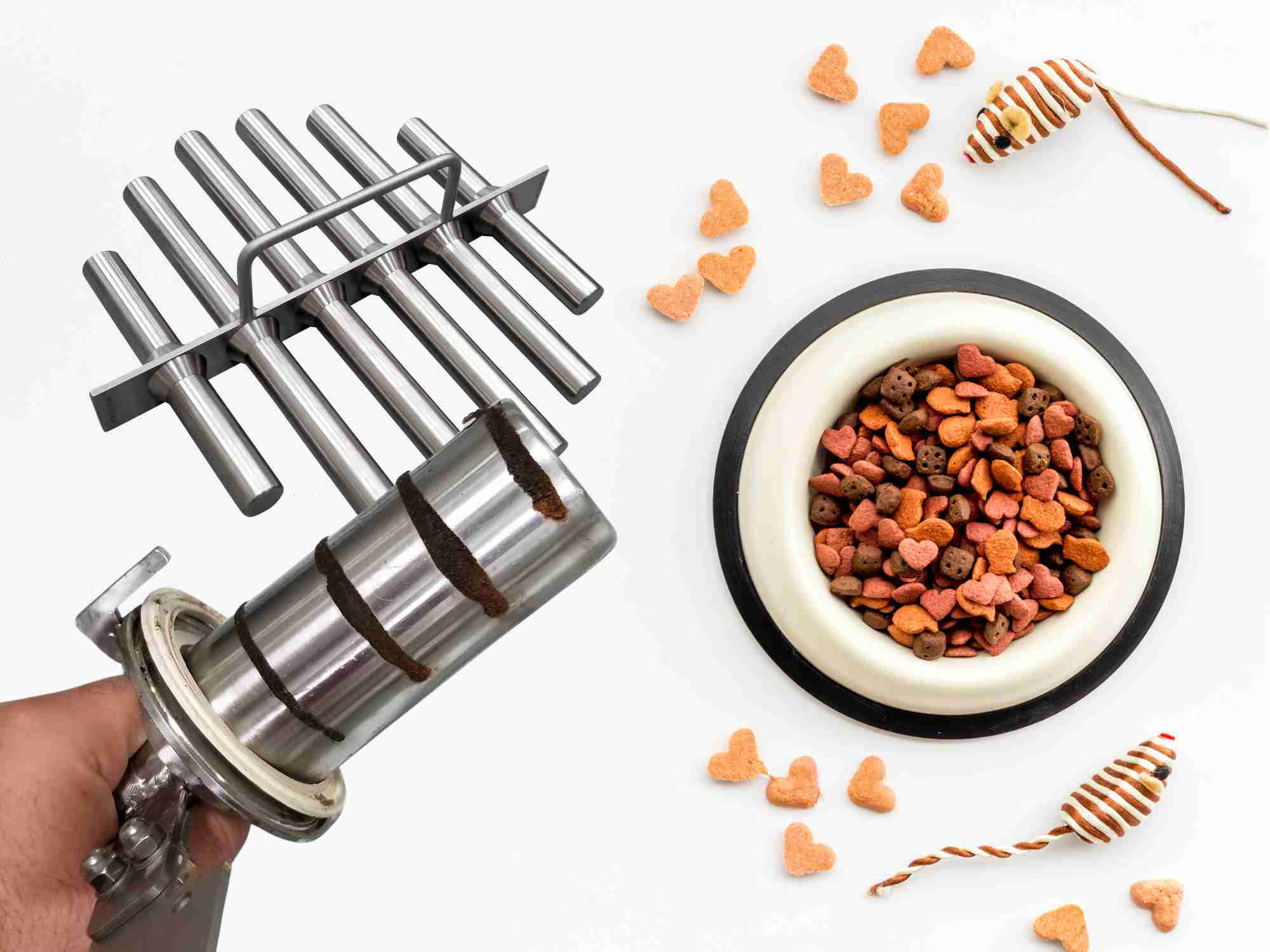
4+ MIN
11/06/2025
Where to Install Magnetic Separators in Pet Food Processing
The complexity of processing, from ingredient handling to packaging, introduces multiple stages where foreign metal fragments can enter the production line. Although many processors understand the importance of magnetic separators in enhancing food safety, uncertainty often arises about the most effective equipment placement for optimal product security and machinery protection.
Effective Placement of Magnetic Separators
Strategically placed magnetic separators is critical for ensuring pet food safety and quality. There are a few locations where installing magnets is most beneficial:
1. Product intakes: Magnetic separators at the product intake stage —for both dry and wet ingredients applications— are essential for removing metal fragments, such as magnetic stones and work-hardened stainless steel, safeguarding machinery, and ensuring incoming materials meet quality standards. This is an important magnet to ensure that the product coming into your process meets your requirements.
2. Post-first stage mixing/wet ingredients processing: After the initial mixing phase, magnetic separators help extract contaminants introduced during processing. This stage reduces the strain on final-stage magnets, especially in cases with high contamination levels.
3. Wet line before canning/packing: In wet pet food production, magnetic separators play a vital role in the canning stage. Proper consideration of flow rate, particle size, and viscosity ensures effective contaminant removal, protecting expensive equipment like twin-screw pumps while safeguarding the final product before packing and metal detection.
4. Dry ingredients processing: Magnet placement during dry ingredient processing depends on factors like flow rate and protection level. Installing separators before extrusion prevents contaminants from being embedded in kibble, streamlining quality control measures and reducing potential hits on final-stage magnets.
5. Dry line before bagging: The final magnet before bagging serves as the last defense against contaminants before products reach consumers. Certified and traceable magnets provide reliable quality assurance and help demonstrate effective preventive measures.
Choosing a magnetic separator for these applications will depend on the flow rate, density, speed, and more.
Top Magnattack® Magnetic Separators for Pet Food Applications
Robust food safety protocols are fundamental to ensuring nutritious and safe pet food while maintaining consumer trust. Product recalls are financially costly and damaging to brand reputation, making comprehensive quality control measures essential.
A single recall incident can impose a significant burden on a production plant, both in terms of product losses and the possible impact on the company's image, not to mention huge potential financial losses. It is critical for manufacturers to realize this risk and have comprehensive quality control measures in place.
The Magnattack expertise and range of magnetic separators can bolster your safety measures and give you peace of mind.
The Mag-Ram® Self-Cleaning Separator is an advanced solution that is highly effective for processing raw materials such as grain, protein meal, and meat and bone meal, as well as for dry ingredient handling and final stages before bagging. Its automatic self-cleaning functionality ensures rapid and efficient removal of ferrous metal contaminants, delivering exceptional performance, minimizing downtime, and maximizing productivity. Additionally, its dedicated contaminant chutes and pneumatic cylinders offer precise individual control, making it simpler than ever to maintain the integrity and purity of pet food products.
Additional innovative solutions include:
Spherical Inline Pneumatic Transfer Magnet: Designed for pneumatically conveyed powders, grains, and premixes, this separator features an aerodynamic structure that eliminates sharp edges, ensuring smooth material flow without causing pressure fluctuations. Its unique magnetic field and strong retention capacity effectively manage high-velocity applications.
Round Nose Plate Magnet: Typically placed before high-value processing equipment like grinders, shredders, dicers, and emulsifiers, this magnet is designed to extract and remove metal contaminants from applications involving chicken frames, whole muscle products, poultry, beef, and other materials. It is also highly effective in dry ingredient processing.
Emulsion & Slurry Pipeline Separator: Specifically designed for viscous applications such as meat emulsions and slurries, this separator ensures the purity of slurry mixtures. Its' coned body eliminates pooling areas and air pockets, facilitating a smooth flow of liquid products. Additionally, its innovative design, including Acutex® Probes, strikes the perfect balance between magnet strength and open space, maximizing product-to-magnet contact for optimal efficiency.
Rapidclean® Drawer Magnet: Specifically designed for dry ingredients such as meals, powders, grains, and premixes, this magnetic separator features large-diameter RE80® magnet bars to ensure maximum retention of even the tiniest, weakly magnetic fragments. It effectively collects and retains metallic particles from dry ingredients with precision. The Rapidclean cleaning feature allows for easy removal of contaminants without the need for direct magnet handling.
Mag-Ram Self-Cleaning Separator
Rapidclean Drawer Magnet
Magnattack®: A Trusted Partner in Pet Food Safety
With over 50 years of experience in the food processing industry, Magnattack® offers an innovative way to approach foreign metal control. Thanks to our cutting-edge technology and commitment to excellence, we've built a reputation as a trusted provider for pet food facilities worldwide. Don't compromise on the safety of your production process —explore our listing of metal separators for pet food applications today!
We are exhibiting at the Pet Food Forum in Kansas City, MO, USA. April 28-30, 2025 —visit us in booth #1602!
By Magnattack
Source: All Pet Food Magazine
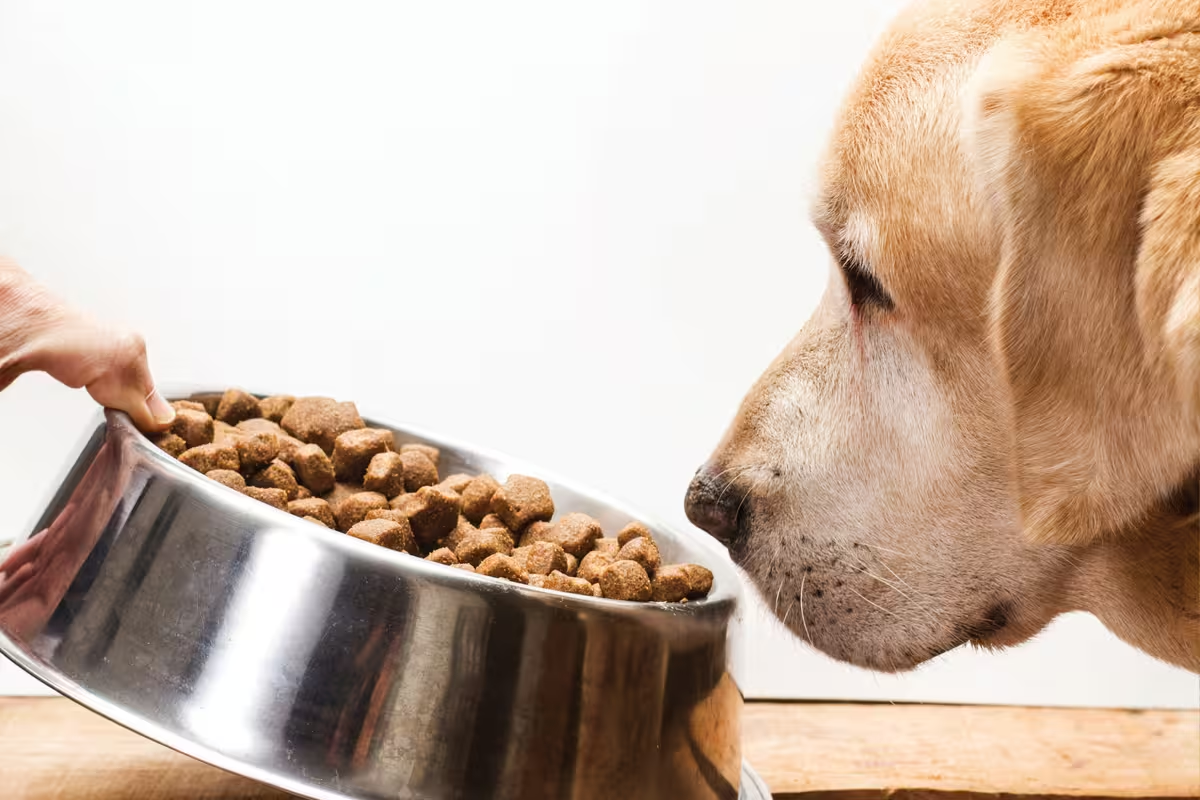
5+ MIN
25/02/2025
Improving Product Purity in Meat Rendering and Pet Food Processing
Sources of Metal Contamination in Meat Rendering
In the meat rendering industry, the sources of metal contamination vary depending on the part of the process and type of product. The objective of a magnetic separator is to prevent an unacceptable amount of contamination generated in a milling process being transferred to the client to deal with.
For example, many ovine meal processors face a challenge with removing slow-release capsule springs from rendered meat, which get ground-up within the product. Having a magnetic separator to extract these fine metals is an excellent way to increase the quality controls and solve this issue.
A common source of contamination found in poultry processing are magnetic stones, which originate from the gut of the poultry and are ingested from the ground while feeding. The magnetic stones can be removed by utilising powerful magnetic separation equipment.
Another very common source of metal contamination in meat rendering is the hammer mill. As the hammer mill materials slowly wear away, these metal fragments (coarse and fines) are introduced into the product. Effectively extracting these fragments can only be done with a strategically positioned, high-intensity magnetic separator.
To reduce machine protection issues in the meat rendering industry, these types of magnetic contamination need to be removed from the process. Factors such as screen breakage, downtime, loss of production, and tramp iron contamination causing fires/explosions in the hammer mill can all be drastically reduced by placing correct metal fragment controls in place. This means less downgraded products, reduced quarantined shipments, prevention of brand name damage, and satisfied clients!
Many rendering industry professionals state that they were not aware of the levels of fine metal fragments within their meat and bone meal until installing a magnetic separator and seeing the vast amount of magnetic fines extracted. A great way to discover the levels of metal contamination in your finished meat meal is through utilising a certified Lab Test Magnet Probe. The magnetic probe is placed into the bag of finished meal and swirled around to collect magnetic fragments and provide an indication of the metal contamination levels.
Sources of Metal Contamination in Pet Food Processing
Predominantly, metal contamination comes from bulk ingredients and is then distributed throughout the product lines. The remainder of contamination is generated in the process and varies greatly depending on the type of impact machinery that is used for sizing and screening ingredients and the longevity and wear of conveying systems.
The objective of magnets in pet food is to control contamination on bulk intakes and to also act as a final control prior to packing areas and metal detection. Magnetic separators play a crucial role in retaining the magnetic fines contaminants that are below sensitivity threshold of metal detection before they reach the CCP. An efficient magnet will drastically reduce waste from metal detectors and improve product purity from magnetic fines contamination.
Magnetic Separation Solutions for Meat Rendering & Pet Food Processing:
Mag-Ram® Automatic Self-Cleaning Magnet
The Mag-Ram® Automatic Self-Cleaning Magnet has proven to be one of the best performing and successful magnets as it can be programmed to automatically clean itself and therefore save operator time, as well as reduce safety risks. Typically installed at incoming dry materials locations (such as MBM or grain) and final dry product/bulk out-loading locations.
Mag-Ram® Self-Cleaning Magnet in meat rendering
In some applications, the contamination is so high that manually cleaning conventional grate magnets is neither practical nor convenient. Once contamination builds up over the magnetic bars, the magnet's strength is 'cancelled out', meaning that further contaminants passing over the magnet just keep flowing down the product stream and remain in the finished product.
The modular design of the Mag-Ram® allows it to handle anywhere between 3T to 90T per hour! This self-cleaning magnet can clean one ram at a time or all at once, and a wear equalization feature is incorporated to prevent flat spots on the magnet and uneven wear on the seals. This means more reliability for a longer period of time.
The Mag-Ram® magnetic bars/rams are engineered to rotate with each cleaning cycle, and short bursts of air are directed at the magnets also help remove the pyramid of excess material from being carried over to the reject side. This means a lean contaminant sample is achieved, easy to analyse for more accurate traceability of risks and less product wastage.
Spherical Inline Pneumatic Transfer Magnet
Where a gravity-feed magnet, such as the Mag-Ram®, is not feasible and the product is pneumatically conveyed via blow, vacuum, or pneumatic transfer line, a Spherical Inline Pneumatic Transfer Magnet is a very effective solution. These aerodynamic magnetic separators are very resilient in high-flow and abrasive applications and enable efficient extraction and retention of metal from high-velocity powder lines without experiencing bulk density problems.
Spherical Inline Pneumatic Transfer Magnet
Dual Round Nose Plate Magnet
For difficult-to-flow applications with products such as cakes (or crax), or applications processing chicken frames, whole muscle products, poultry, beef, lamb, venison, etc, a Dual Round Nose Plate Magnet is an efficient solution. For pet food processing applications, these units can be installed prior to expensive processing machineries, such as grinders, shredders, dicers, and emulsifiers, to remove metal fragments to avoid costly damage, downtime for repair/maintenance, and loss of production. Dual Round Nose Plate Magnets easily pick up chunky contaminants such as nails and bolts from the product and protect machinery without an unacceptable restriction to the product flow.
Dual Round Nose Plate Magnet in a rendering application
Rapidclean® Grate Magnet
The Rapidclean® Grate Magnet is an effective grate-in-housing system designed for dry ingredients such as meals and powders. With easy-cleaning operations conducted wholly outside of the product zone and the absence of stainless steel sleeves, the Rapidclean® is a hygienic alternative to conventional sleeved grate magnets and pull-through wiper-style magnets. Plant operators can also fully inspect magnet bars before they are returned to the product flow.
Contamination collected on Rapidclean® Bars
Emulsion & Slurry Pipeline Separator
For viscous meat emulsions, slurries, and liquids, from which it is often difficult to extract weakly magnetic fragments, a hydro-dynamic Emulsion & Slurry Pipeline Separator provides superior product-to-magnet contact and more efficient magnetic separation.
The Emulsion & Pipeline Separator features powerful, high-intensity +11,000 gauss Acutex® Probe Magnets. These patented magnets intercept the flow of product and extract physical metal fragments including work hardened stainless steel (originating from equipment wear) and magnetic stone particles.
Emulsion & Slurry Pipeline Separator installed in a pet food application
Improve your foreign metal fragment controls, product purity and value, and reduce risks with powerful magnetic separation equipment. Contact Magnattack® and talk to experienced metal fragment control specialists about the right solution to integrate into your process.
By Magnattack
Source: All Pet Food Magazine
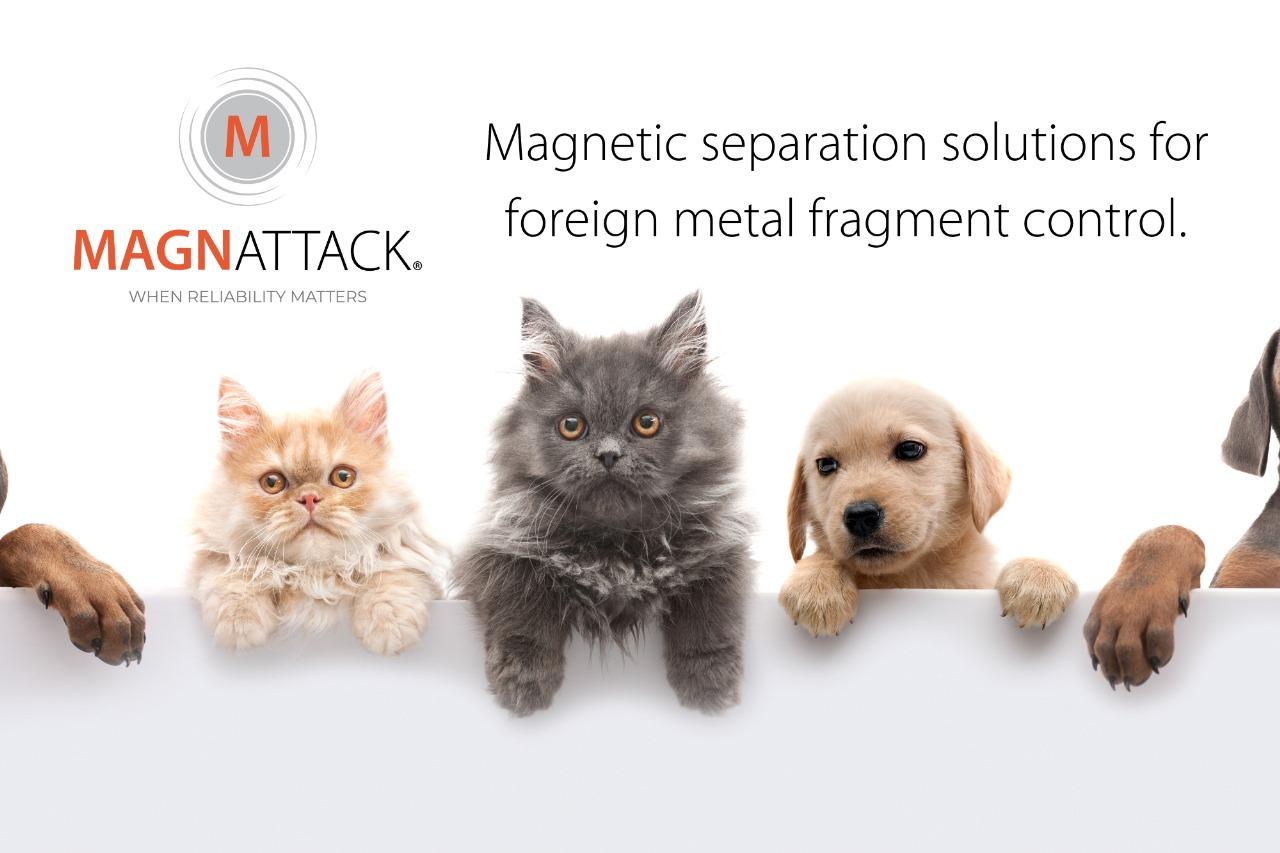
5+ MIN
13/11/2024
Improving product purity in pet food with magnetic separators
More 'humanised' pet foods have become available on the market and are becoming increasingly popular among pet owners, who want the very best, healthy meal options for their beloved pets.
We have seen a change in quality control in the pet food and meat rendering industries, with a heightened focus on product purity, including metal fragment control.
These industries tend to have high levels of metal contamination in their product, as the meat and bone meal product can be very abrasive to process and tends to wear down machinery more quickly than some other product types. The contamination can originate from various stages of processing, as well as from the product itself, so it is important to install metal fragment controls such as magnetic separators or metal detectors in various locations, and in particular, the most final stage in a processing line prior to packing.
How to know where to install magnetic separators?
Choosing a location for food magnets will depend on multiple factors. For example, the amount of metal contamination within the product can play a significant role, as this can affect any existing magnets in the processing line and their ability to collect and retain the contaminants. With a high level of metal contamination, a magnet that requires manual cleaning can get overloaded and 'short out', meaning that it cannot collect and retain more contamination. Any additional metal contamination can then flow past the overloaded magnet and remain in the product.
This highlights the importance of having upstream magnetic separators to offload the final magnets in food processing lines, especially ones that have a high level of metal contamination. The importance of cleaning magnets frequently also shouldn't be overlooked and should be a crucial step in manufacturing procedures.
Another example of a reason to install magnetic separators can be to protect machinery from damage caused by certain non-ferrous or ferrous metal contamination. Depending on the product and processing line, as well as the type of contamination, there are a number of magnetic separation solutions suited for the job.
The Magnattack® Magnetic Separation range for pet food has proven to be very effective in both dry and wet product applications. Let's have a look at each magnetic separation solution and the type of product each magnet is designed for:
Magnetic Separation Examples for Dry Pet Food Products
Magnattack® manufactures a number of magnetic separators for dry pet food processing applications.
Mag-Ram® Self-Cleaning Magnet
The Mag-Ram® Self-Cleaning Magnet has proven to be an amazing self-cleaning permanent magnet and metal fragment control solution for dry products and incoming raw materials such as MBM, protein meal, grain, final kibble, and more.
With the ability to configure the cleaning cycle to suit tonnage rates and contamination levels, the Mag-Ram® gives operators the ability to have the magnet frequently cleaned, and automatically.
This self-cleaning magnet requires zero downtime, with no need to stop production, which is a huge benefit for processors with products high in metal contamination that cannot stop production for frequent cleaning. The rotating magnetic rams ensure minimal product build-up and blockage, and the magnet design provides excellent product stream coverage.
Not only this, but the magnetic rams can be configured to be cleaned one at a time, meaning that your product stream remains covered by the other magnetic rams! You are truly going to want to add this self-cleaning magnetic separator to your materials handling equipment wish list!
Rapidclean® Grate Magnet in Housing
The Rapidclean® Grate Magnet overcomes issues associated with conventional magnetic grates, such as stainless steel sleeves, cleaning difficulties, jamming, safety issues, and more. This permanent magnet consists of open-ended magnetic bars, and once the magnetic drawer is opened, the cleaning is completed away from the product stream, using the Rapidclean® Cleaning Tool.
This grate magnet is designed for dry products, such as meals, powders, grain, and premixes.
Dual Round Nose Plate Magnet System
The Dual Round Nose Plate Magnet System is another industrial magnet design suited for pet food applications. This magnetic separator can be installed in applications processing chicken frames, whole muscle products, poultry, beef, lamb, venison, final meal products and more, prior to expensive processing machinery such as grinders, shredders, dicers, and emulsifiers.
In some applications, especially those with high tonnage and fast-flowing products, fragments can be brushed off plate magnets by the oncoming product and back into the product stream. To reduce this risk, Magnattack® has developed the RE80® Round Nose Plate Magnet. This system features a High-Intensity RE80® Bar Magnet at the end of a standard magnetic plate. The Separation Bar Magnet offers protection against dislodged fragments and prevents them from re-contaminating the food product. When metal fragments are collected by the Separation Bar, they are washed safely to the underside of the magnet and out of the path of oncoming product.
With the deep field capability of the magnetic plate added to the intensive coercive force of the Separation Bar, you gain far superior control over foreign metal pieces and increased protection against contamination.
Spherical Pneumatic Transfer Magnet
The Spherical Pneumatic Transfer Magnet is a powerful magnet designed for high-velocity blow, vacuum, gravity, and pneumatic transfer lines. This magnetic separator suits pneumatically conveyed powders, grains, premixes, and palatant products. The aerodynamic design of this Magnattack® system enables efficient extraction and retention of metal from high-velocity powder lines, without experiencing bulk density problems.
The Spherical Magnet is considered a more hygienic, powerful and superior alternative to traditional bullet-style and cartridge-style magnets.
Magnetic Separator for Wet Pet Food Products
Emulsion & Slurry Pipeline Separator
The Emulsion & Slurry Pipeline Separator is an inline liquid magnet that is ideal for viscous liquid applications including meat emulsions, meat slurries, and more.
It is often difficult to extract weakly magnetic fragments from viscous meat emulsions, slurries, and liquids. In answer to this problem, Magnattack® has developed a special hydro-dynamic magnet system specifically for this purpose. The units are an efficient and sanitary alternative to Liquid Trap/Finger Pot Magnets, which can also be heavy and difficult to clean properly.
This mince separator excels in these applications as it features our patented RE80®HT Acutex® Probe Magnets, which provide superior product-to-magnet contact and more efficient magnetic separation.
The lachrymiform (or 'tear drop') shape of the Acutex® Probe Magnets allow for very smooth transition of viscous products to move around the magnet with minimum resistance to flow. Maximum product to magnet coverage is achieved without causing leaks, blockages, and pressure problems.
The peak (or V-section) of the probe is faced towards the oncoming product stream, ensuring that collected magnetic fragments are washed to the back of the probe and safely retained until cleaning operations are underway. This feature greatly reduces the risk of recontamination caused by the impact of the product flow dislodging the collected fragments and reintroducing them back into the product stream.
We're here to help! Contact Magnattack® for a consultation, or book in a risk assessment to determine potential gaps in your foreign metal controls.
By: Magnattack
Source: All Pet Food Magazine