The customer's choice of the CS-WP solution
An American-based customer of KSE, operating in the premix industry, selected the CS-WP solution due to an urgent need to optimize space utilization in their production facility. This innovative solution enabled them to save significant vertical space, with reductions of 4 to 5 meters compared to a conventional weighing system. Additionally, the CS-WP system offers direct separation of contaminants for all raw materials, ensuring the entire facility remains free from contamination.
Another customer in Spain, a leading manufacturer in the food additive industry, has also expressed interest in the CS-WP solution because of their stringent contamination control requirements. The CS-WP system allows macro ingredients to be safely transported in dedicated containers, ensuring clean and flexible distribution to three separate mixing lines.
Exploration of market-based alternatives
The customer explored two alternative solutions. Initially, a traditional pneumatic conveying system was considered but dismissed due to hygiene issues and excessive energy consumption. The second option involved a container concept relying on AGVs (Automated Guided Vehicle). Ultimately, KSE's CS-WP concept emerged as the most fitting and seamlessly integrable solution, enabling the maintenance of the desired compact building height.
Future expansion and developments
The client positions the CS-WP project as the ''Next Generation Plant'', hinting at the possibility of establishing future plants based on the same concept. This marks the inaugural joint project for the Spanish customer and KSE, with aspirations to extend this concept to other facilities, thereby assuming a pioneering role in the Spanish food additive industry.
A breakthrough solution
The CS-WP emerged as a groundbreaking weighing solution within the ACT (Automatic Container Transfer) framework, renowned for its internal transport capabilities. Manufacturers are seeking space-saving solutions in their plants while aiming to achieve minimal contamination by dispensing products directly into containers. Tailored to accommodate a wide dosing range, this solution stands out for its versatility.
Intensive development process
The concept promptly resonated with our customers' needs and industry demands, particularly in sectors like premix and pet food. The development process of the CS-WP entailed tackling several design challenges, such as achieving optimal balance in the setup. With dimensions of approximately 1.5 meters x 1.5 meters and a height of 5 to 6 meters, this resulted in a column four times as tall as it is wide. This configuration posed potential tipping hazards, especially when the system was in motion while carrying weight at the top. To prevent this, rollover safeguards were implemented, and extensive testing was performed.
Marketplace
Another crucial aspect involved a meticulous examination of the system's extraction process. Customers typically invest in an ACT system to maintain a pristine working environment with minimal contamination. However, if dust escapes through open joints during each movement, this objective is compromised. Moreover, the extraction process must not interfere with the weighing signal during the dosing process, ensuring that accuracy is not compromised.
Following extensive consultation and collaboration with suppliers, multiple concepts were devised and executed by the mechanical, electrical, and software teams. Presently, two variants are available: one where dust from the filters returns with the product, minimizing contamination but ensuring all product accompanies it through processing, and another where dust extraction directs waste to a remote unloading point, eliminating contamination but resulting in waste. The selection between these variants depends on the customer's specific needs and requirements.
The operational phase
During the implementation phase of industrial solutions, addressing technical challenges is only part of the equation; understanding real-world usage is equally vital. Hence, KSE engages its service department from the beginning of a project to ensure that aspects, such as cleaning positions, accessibility, and installation safety are meticulously accounted for. This approach establishes a robust groundwork for a successful project, enhancing both efficiency and safety.
By: KSE Process Technology
Source: All Pet Food Magazine
You could be interested: Great News: Josera Integrates KSE’s Cutting-Edge ALFRA Technology
About company
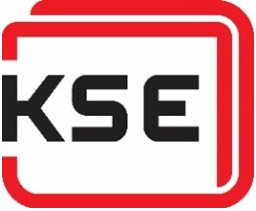
About company
Partner in optimizing production processes
Increasing complexity forms the biggest challenge for animal nutrition manufacturers; more recipes, a growing number of ingredients, additions that are difficult to dose and higher quality standards contribute to this trend.
For over 50 years, KSE has been supplying future proof solutions to stay ahead of the trend in the form of modular machinery and smart software that fit together perfectly. We create flexible processing solutions that enable a responsive production process. Automation, accuracy and contamination control are at the basis of our future-proof innovations. Our aim is to not only improve the production process, but also to make a significant contribution to increasing margins and achieving targets.
Together we create the solutions with the best results!