We are talking with Dennis van Lankeren, Business Unit Manager ALFRA, and Bas Versluis , Head of Sales at KSE. Bas: ''The ALFRA Automatic Container Transfer (ACT) consists of a modular portfolio based on containers that provides process flexibility and minimal contamination. The system uses container shuttles (CS) to transfer products and components without contamination. The WP addition clarifies that in addition to internal transfer, the system has also integrated dosing and weighing.''
Lower building height and higher silos
Transfer by way of containers is not new for ALFRA, but combining this with dosing and weighing is. Dennis adds: ''Until recently, when silos were located at the top of the plant with a dosing installation, it was necessary to place a scale underneath to dump the correct amount into the movable container. With the CS-WP system, ''moving'', ''dosing'' and ''weighing'' have been added to its functionalities. This means an extra weighing system, that would require extra height, can be eliminated. In other words: the plant can be constructed with a lower building height or the new available height can be used to build higher and larger silos."
Carriers and macros
In the premix production process, the CS-WP system is suitable for larger components, such as carriers and macros. Because of the drop height between the silo outlets and the scale, it is not possible with this solution to dose small quantities, such as micro components, with sufficient accuracy. These can be prepared compactly on another dosing unit that works in parallel to be picked up by the container and transferred along with the large components to, for example, the mixer. This means the full batch remains in the same container during the entire process.
The customer's choice for choosing the CS-WP solution
The customer in the U.S. opted for the CS-WP solution because of their urgent requirement to optimally utilize the available space in their existing facility. Integrating the system in their plant allowed them to save valuable height that would otherwise be taken up by a conventional weighing system. This resulted in height savings of approximately 4-5 meters. The fact that the CS-WP system guarantees a low contamination value was also a reason for the customer to buy this system.
The other customer in Spain, who is in the feed additives industry, installed the CS-WP solution also because of the specific requirements regarding contamination control. By using the CS-WP, macro ingredients can now be safely transferred to three different mixing lines.
Marketplace
Alternative solutions in the market
Dennis explains that several alternatives were considered by both customers. One alternative involved a traditional pneumatic transfer system, but this solution turned out to be disadvantageous because of hygiene issues and high energy consumption. The second alternative involved a container concept based on AGVs (Automated Guided Vehicle), which however, is complex to pair with several parallel production lines within a plant. In the end, KSE's CS-WP concept proved to be the most suitable and integratable, and resulted in maintaining the desired compact building height.
Intensive development process
The development process of the CS-WP involved some challenging design issues, including balancing the setup. With a footprint of approximately 1.5 meters x 1.5 meters and a height of 5.0 to 6.0 meters, this resulted in a column four times as tall as it is wide. This created a potential toppling hazard, especially when the system moved with weight on top. To prevent this, rollover safeguards were installed.
The system's dust extraction proved to be another puzzle. Customers who purchase an ACT system usually do so because of the need for a clean work environment with minimal contamination hazard. However, when dust escapes at the open joints during movement, this requirement is not met. In addition, because of accuracy, the extraction must not affect the weighing signal during the dosing process.
After extensive consultation and advice with suppliers, several concepts have been worked out, hereby coordinating mechanics, electrical and software. There are not two available variants: one where the dust collected from the filters goes back into the product, which can result in minor contamination, but ensures that all the product is moved along during the process. There is also a variant in which the dust extraction is taken as waste to an external discharge location without contamination, but thus resulting in waste. The choice between these two variants depends on the customer's requirements.
Application
Bas concludes, ''This KSE concept finds its application mainly in the premix and pet food industry. For application in the compound feed industry, the system is generally too small and relatively expensive.'' Bas adds that the customers mentioned in this article wish to remain anonymous for the time being, but that field results will be available soon.
Source: KSE Process Technology.
You could be interested: RBS Baked Pet Food Systems: Optimized, Automated Solutions for Baked Pet Treats and Baked Kibble (Part 2)
About company
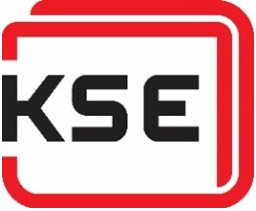
About company
Partner in optimizing production processes
Increasing complexity forms the biggest challenge for animal nutrition manufacturers; more recipes, a growing number of ingredients, additions that are difficult to dose and higher quality standards contribute to this trend.
For over 50 years, KSE has been supplying future proof solutions to stay ahead of the trend in the form of modular machinery and smart software that fit together perfectly. We create flexible processing solutions that enable a responsive production process. Automation, accuracy and contamination control are at the basis of our future-proof innovations. Our aim is to not only improve the production process, but also to make a significant contribution to increasing margins and achieving targets.
Together we create the solutions with the best results!