This tool is particularly helpful in servicing control systems through a network connection. By connecting to the system's programmable logic controllers (PLC), Human Machine Interface (HMI), and other Ethernet compatible devices, integrators can efficiently monitor, troubleshoot, and fix an issue without physically traveling to the site.
Employers can control many quality services via remote access, such as: troubleshooting, remote startup, remote monitoring, software upgrades or additions, proportional-integral-derivative (PID) tuning (adjust the PID controller), User Interface (UI) additions, and other improvements to the customer's automated system. Service technicians have access to tools and software solutions that many manufacturing plants may not have, and these can be utilized remotely to enhance the service experience.
This article discusses best practices for establishing remote access, services provided using a remote connection, and help determine if remote access is correct for your plant.
Best practices for establishing Remote Access
When establishing remote access to a plant's control system for the first time, there are several guidelines to follow from both the integrator and the plant's side.
The first step to connecting remotely is to obtain permission from the plant's IT department to access the virtual private network (VPN). The integrator provides the plant's IT department with a list of authorized technicians who will provide service and support for the plant. The plant's IT department will set up user accounts for those authorized technicians. If applicable, non-disclosure agreements will be signed.
Safeguards for a secure connection
- Integrators use a VPN for connecting to the plant's control system
- Plant IT has an isolated network for the VPN
- Routine system backups
- Utilize virtual machines (VM)
- Remote Access – Technical Service and Support
A major benefit for establishing remote access to a plant's control system is the ability to quickly be connected for service and support. In the event there is a problem with the control system, such as a production sequence is out of order, a burner is not reaching a high enough temperature, or a conveyor is not moving fast enough, plant maintenance personnel can contact an integrator for technical support. A service technician is speaking directly with the plant personnel. By working together, problems are solved faster, immediate feedback is provided, questions or concerns are addressed, and this is an opportune time to provide plant personnel some system training.
With remote access available, service technicians are able to support plants quickly and efficiently. With prior remote access established, a technician can be connected to a plant within 15 minutes of calling about an issue. This quick connection time allows for troubleshooting to begin immediately, while reducing plant down-time.
Marketplace
Remote access allows the service technician to monitor the system live to catch any intermittent problems. Control Systems can be remotely accessed and watched for a specific problem or issue over a number of hours or days. Then when the problem occurs, the service technician can isolate what caused the problem, what conditions were present when the issue occurred and provide a solution.
Another benefit to remote access is being flexible within the time frame of system maintenance. Service can be provided around rigid time and production schedules, as remote access can occur at any time during the day. This eliminates waiting until regular business hours to contact support and then having to make travel arrangement to get a technician on site. Remote access can also serve as an extension of the customer's maintenance and continual improvement departments.
Remote Access – Control System Startup
Some Control System modification and addition projects can be started up remotely. The benefits to a remote startup are similar to remote access service.
- Time (travel and onsite)
- Money (costs of travel, rental, accommodations, etc.)
- Resources
Help can be offered immediately, the customer only has to pay for labor time to fix an issue, fixes can be provided around rigid production schedules, and additional resources can be utilized.
Remote Access can also be used in conjunction with onsite startups to provide additional training and which helps build on more complex ideas and unique operating situations. And lastly, with the restrictions of travel and health concerns surrounding Covid 19, quarantine restrictions and safety protocols can be eliminated if remote access is used.
Remote Access can provide a quick, affordable solution for control system maintenance. Remote Access saves travel time, accommodation costs, and costs associated with down-time. Remote access provides the customer with immediate help and resources any time day or night and remote access can also be used to monitor intermittent problems. Remote Access can be utilized not only for start-ups, service, and maintenance, but operational training as well.
NorthWind's Service Team provides remote service and support for all control system issues.
Form more information about NorthWind click HERE.
Author: Jake Taylor - Service Manager
Source: NorthWind's Technical Services
You could be interested: RBS Baked Pet Food Systems: Optimized, Automated Solutions for Baked Pet Treats and Baked Kibble (Part 2)
About company
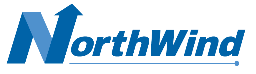
About company
NorthWind’s skilled team of engineers, programmers, and technicians have extensive process experience in addition to programming and design expertise in a wide range of industries.
NorthWind provides automation solutions for manufacturing facilities throughout the world. We also offer industrial electrical installation services in the USA.
Our headquarters is located in Sabetha, KS. The majority of employees and all panel fabrication activities are located at this facility. A second location was established in San Jose, Costa Rica in June of 2019 in order to better serve customers in Latin America. The Costa Rica office houses four employees that work in Service, Sales, and R&D.
Our skilled team of engineers, programmers, and technicians have extensive process experience in addition to programming and design expertise in a wide range of industries. The NorthWind PlantLOGIX™ software suite streamlines and simplifies programming, management, and maintenance of industrial processes while increasing visibility into what’s happening on the factory floor. State-of-the-art office technology and expertise allows NorthWind to provide programming and support services to clients anywhere in the world in a multitude of industries.
Our U.L. Listed control panel shop is located in a 10,000 sq. ft. climate-controlled facility that is fully-equipped to fabricate, test, and ship control panels of any size. High standards and advanced manufacturing technologies used by NorthWind ensure that control panels are delivered onsite on time and ready to be installed.
NorthWind strives to achieve high standards that meet customer needs and company stability. The company has been Control Systems Integrators Association (CSIA) certified since 2010 and continues to employ CSIA’s Best Practices and Benchmarks in order to provide the best value to its customers, combining technical proficiency with sound business practices.
NorthWind is also an accomplished Rockwell Automation Solution Partner, providing proven services and solutions that meet our customers’ automation needs. Finally, NorthWind was named CSIA Integrator of the Year in 2019, a prestigious national award given to controls system integrators that demonstrate cutting-edge technology and cost effective solutions for manufacturers