It is worth mentioning the options available in the market that can be interesting for companies in general.
Dumper (Intake of Raw Materials)
It is more common to use dumpers, especially in new companies, since this resource is considered when planning the execution project aiming to facilitate the unloading of bulk materials and reduce the number of employees in the raw materials intake.
There are different dumpers in the market. It is crucial to evaluate the model that fits your company's needs, considering the truck receiving the dumper, the density, and raw material fluidity, among other factors.
The intake hopper must have the same volume as the truck. Otherwise, it will produce product congestion, and the unloading process must wait for the hopper to empty.
Automatic Boilers
Many feed mills use wood or wood chip boilers to generate the steam needed to power mills of pellets, extruders, and dryers. Boilers usually need one employee per shift to power the energy and monitor its functioning.
However, automated fueling systems (commonly for wood chip boilers) already exist and require a machine operator to monitor but not to assist the process.
Micro and Macronutrient Dosing System
Most feed mills now have a macronutrient automated dosing system, which means raw materials with more inclusion volume in formulas.
On the other hand, dosing is still manual in the inclusion process of micro-ingredients (vitamins and minerals, or premix).
The automatization of this process has two main advantages: 1) reduces the labor need, since manual weighing needs at least one or two operators; 2) reduces the error percentage in the formulation (in the manual process, operators can make mistakes when dosing the amount of vitamins). If this happens, it will directly affect food efficacy, and the animal consuming it will not have appropriate nutrition and may show different zootechnical indicators than expected.
Bagging and Palletizing Automated Systems
Marketplace
Feed bagging and palletizing systems require more labor than others. There are some options to automate these processes, but many factors must be considered, e.g., package size; capacity of bags per minute/hour in each package (bagging systems often have lower capacity per hour when dealing with smaller volume packages); the type of bag, some of them are only for plastic packaging while others work with paper and raffia; pallet size, automated palletizing systems size according to pallet's measure; the ability of suppliers to provide technical assistance and spare parts, etc.
If the factors that affect the equipment size are analyzed and the hiring, installing, and maintenance procedures are well done, automation can generate high profits. It eliminates the requirement for four employees per shift (two in the bagging line and two in the palletizing). Besides, it drastically reduces mistakes, such as irregular bagging sealing and wrong distribution of bags.
By Ferraz
Source: All Pet Food Magazine
You could be interested: FAMSUN strengthens its leadership in Latin America with integrated solutions and innovation in pet food
About company
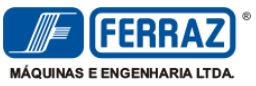
About company
FERRAZ is the Brazilian market leader in the production of equipment for the animal nutrition industry and exports its products to other countries.
Based in the city of Ribeirão Preto, São Paulo – Brazil, today occupies an area of 70,000m² in its plant, the company designs, manufactures, assembles and installs complete lines of equipment for the production of animal feed type: Bran Feed, Extruded and Pelleted.
Since the beginning of the project to the operation of the plant, Ferraz has specialized professionals to provide services, such as automation, start-up in the field, assembly, employee training, technical support, spare parts. Supplying all the needs of feed mills.