The most obvious illustration of this is systems that have obsolete electrical components and legacy software that is no longer actively supported by original manufactures. As we move into Industry 4.0, the old standard of each individual machine having an isolated 'island' of automation is being replaced by more integrated automation systems that communicate to each machine, sharing and creating significantly more data than even 15 years ago. With this added data is the desire to connect the plant floor data to business systems. More and more facilities want production orders to come down from ERP systems to process controls, producing real-time consumption data that is utilized to reduce inventory. To stay competitive, many facilities have made the business decision to modernize their legacy machine and controls systems. Typically, this can be done at a fraction of the cost and time of a greenfield project.
Modernizing a control system
A control system upgrade can bridge all these gaps by integrating mechanically sound process systems with a modern automation system. At a minimum these projects consist of substantial replacement of obsolete components, sometimes even retaining the original PLC logic. These projects can also be expanded to include high level integration of different machines, adding new machines to an existing system, ERP integration, and ground-up re-writes of logic and operator screens.
Modernization projects are known to be complex, especially because engineers are required to work inside an existing framework as opposed to building a system from the ground up. There may be missing documentation or drawings. Additionally, some field modifications may not be included in the drawings. Minimizing production downtime is a significant concern, so the implementation window to get the system back in production is often small.
A successful modernization project considers these factors and others during the initial phases of the control system upgrade. Key to any project is developing a deep understanding of the existing system. This is paramount to implementing the upgrade without breaking what is currently in place.
Best practices
As a Senior Project Manager at NorthWind, I have implemented many modernization projects throughout my career. In this time, I have found a few tried and true practices that lead to a successful control system upgrade.
Customer/Project Management Planning
When modernizing any system, a collaboration between customer and Project Management is a must. Through this collaborative approach, a forward-looking plan is made to include functionality, risk avoidance, down time reduction, migration solutions, project phasing, etc. to ensure the project scope is clearly outlined and understood.
Marketplace
Design Trip
There is a misconception that modernization will 'break' the current system and lead to significant downtime. Conducting an initial design trip is instrumental for designing a project that takes into consideration the existing system and its functionality and designing a system that will meet the customers scope and needs.
Before any modernization takes place a review of pre-existing equipment, electrical, design and functionality is conducted. Any existing drawings and documentation are also thoroughly reviewed. In the event there are no drawings of the existing system, a new set will be created.
Safety Considerations
There are misconceptions involving safety considerations: Many people think that safety guidelines are grandfathered in by the date of the original mechanical equipment installation. However, on any substantial electrical modernization project, safety circuits and functionality need to be reevaluated.
Electrical Installation
One of the biggest concerns with control system modernization is the amount of time it will take for installation and requalification. Working with an industrial electrician with the expertise to understand how to work within schedule constraints and provide creative, custom solutions to meet outage windows is critical. Installation can be done in phases, during production downtimes, or any other number of solutions to keep downtime at a minimum.
Benefits of modernization
Updating hardware and software with better automation control systems can improve plant performance, increase productivity, improve communication between the process information and business systems, provide useful production data, provide alerts to improve response times, increase plant system security and perform system diagnostics.
With NorthWind you can achieve an effective modernization project that manages safety, health and environmental risks, get documentation for field devices in the system, and be assured of a more efficient, consistent and optimized operation, with the support of the system for years to come. Contact us today to talk about your system.
By: Blake Bennett – Automatización
Source: Northwind Technical Services
You could be interested: RBS Baked Pet Food Systems: Optimized, Automated Solutions for Baked Pet Treats and Baked Kibble (Part 2)
About company
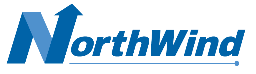
About company
NorthWind’s skilled team of engineers, programmers, and technicians have extensive process experience in addition to programming and design expertise in a wide range of industries.
NorthWind provides automation solutions for manufacturing facilities throughout the world. We also offer industrial electrical installation services in the USA.
Our headquarters is located in Sabetha, KS. The majority of employees and all panel fabrication activities are located at this facility. A second location was established in San Jose, Costa Rica in June of 2019 in order to better serve customers in Latin America. The Costa Rica office houses four employees that work in Service, Sales, and R&D.
Our skilled team of engineers, programmers, and technicians have extensive process experience in addition to programming and design expertise in a wide range of industries. The NorthWind PlantLOGIX™ software suite streamlines and simplifies programming, management, and maintenance of industrial processes while increasing visibility into what’s happening on the factory floor. State-of-the-art office technology and expertise allows NorthWind to provide programming and support services to clients anywhere in the world in a multitude of industries.
Our U.L. Listed control panel shop is located in a 10,000 sq. ft. climate-controlled facility that is fully-equipped to fabricate, test, and ship control panels of any size. High standards and advanced manufacturing technologies used by NorthWind ensure that control panels are delivered onsite on time and ready to be installed.
NorthWind strives to achieve high standards that meet customer needs and company stability. The company has been Control Systems Integrators Association (CSIA) certified since 2010 and continues to employ CSIA’s Best Practices and Benchmarks in order to provide the best value to its customers, combining technical proficiency with sound business practices.
NorthWind is also an accomplished Rockwell Automation Solution Partner, providing proven services and solutions that meet our customers’ automation needs. Finally, NorthWind was named CSIA Integrator of the Year in 2019, a prestigious national award given to controls system integrators that demonstrate cutting-edge technology and cost effective solutions for manufacturers