
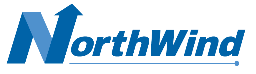
NorthWind Technical Services LLC
http://bit.ly/3YiWuTO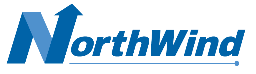
NorthWind Technical Services LLC
About the company
NorthWind’s skilled team of engineers, programmers, and technicians have extensive process experience in addition to programming and design expertise in a wide range of industries.
NorthWind provides automation solutions for manufacturing facilities throughout the world. We also offer industrial electrical installation services in the USA.
Our headquarters is located in Sabetha, KS. The majority of employees and all panel fabrication activities are located at this facility. A second location was established in San Jose, Costa Rica in June of 2019 in order to better serve customers in Latin America. The Costa Rica office houses four employees that work in Service, Sales, and R&D.
Our skilled team of engineers, programmers, and technicians have extensive process experience in addition to programming and design expertise in a wide range of industries. The NorthWind PlantLOGIX™ software suite streamlines and simplifies programming, management, and maintenance of industrial processes while increasing visibility into what’s happening on the factory floor. State-of-the-art office technology and expertise allows NorthWind to provide programming and support services to clients anywhere in the world in a multitude of industries.
Our U.L. Listed control panel shop is located in a 10,000 sq. ft. climate-controlled facility that is fully-equipped to fabricate, test, and ship control panels of any size. High standards and advanced manufacturing technologies used by NorthWind ensure that control panels are delivered onsite on time and ready to be installed.
NorthWind strives to achieve high standards that meet customer needs and company stability. The company has been Control Systems Integrators Association (CSIA) certified since 2010 and continues to employ CSIA’s Best Practices and Benchmarks in order to provide the best value to its customers, combining technical proficiency with sound business practices.
NorthWind is also an accomplished Rockwell Automation Solution Partner, providing proven services and solutions that meet our customers’ automation needs. Finally, NorthWind was named CSIA Integrator of the Year in 2019, a prestigious national award given to controls system integrators that demonstrate cutting-edge technology and cost effective solutions for manufacturers
Products
Company News

4+ MIN
23/06/2025
Digital Transformation Journey: Guiding a Pet Food Manufacturer to Industry 4.0
Our Approach To start the audit, NorthWind's Team met with plant production leads and process experts from each area of the plant, including forecasting, planning, production, maintenance, information and technology, research and development, purchasing, distribution, and accounting, with the primary goal of gathering information about current operations and flow of data throughout the organization. These meetings helped the NorthWind team understand the existing infrastructure and identify focus points. Information Gathering Focus Points Evaluation of current technological infrastructure Diagnosis of the level of automation and current digital methodologies Identification in areas of opportunities for improvement Manufacture's capabilities to integrate industry 4.0 technologies Review of current metrics on operational efficiencies and quality Evaluation of current metrics on safety and sustainability Review of current key performance indicators (KPIs) After gathering the information NorthWind developed, in collaboration with plant personnel, an on-site agenda planned around production schedule and personnel availability. While on-site NorthWind identified and analyzed the existing gaps, deficits, and areas of opportunities with respect to the adoption of Industry 4.0 standards. At the conclusion of the site visit, NorthWind developed a comprehensive report outlining the plant's digital transformation journey. The report included the current status of the manufacturing practices, diagnosis of areas of opportunity, and proposed an actionable plan with progressive milestones to fully achieve Industry 4.0 manufacturing standards. Digital transformation recommendations Below is a sample of the recommendations the NorthWind Team provided or discussed with the manufacturer based in the findings in the audit. Discussed the importance of a Raw Material Silo Inventory System. Reviewed Manual Documents that would benefit from a digital format. Recommended a replacement and modernization of the existing control system. Reviewed alternatives to implement seamless upstream and downstream equipment. Reviewed data collection and material tracking benefits for ingredients throughout the plant. Reviewed automation alternatives for Setpoint management for dosing raw material. Established Rework Integration Protocol on Production Line. Reviewed the benefits of automation for the Extrusion Process. Reviewed the benefits of automation for unloading finished product silos and provide material tracking. Proposed a data collection system in the packaging area by communicating with robotic arms, bagging machines, and using a barcode tracking system. Reviewed implementation of a Warehouse Management System (WMS). Increase cybersecurity of the plant control system. The recommendations can be completed in phases, and the desired Industry 4.0 goals can be achieved with modernization of the process control system, MES Dashboards (Manufacturing Execution System), Digital Solutions (network architecture and topology), Integration with their ERP System, Cloud connectivity, and redundancy. The impact Based on the report's findings, the customer can expect the following Customer Benefits after implementing Industry 4.0 practices: Increased Efficiency: Automation and connectivity lead to streamlined processes, reducing downtime and enhancing productivity. Improved Quality: Advanced technologies such as machine learning and AI can monitor production quality in real-time, allowing for quicker adjustments and reducing defects. Greater Flexibility: Smart manufacturing systems can quickly adapt to changing market demands, enabling mass customization and shorter lead times. Enhanced Data Analytics: Industry 4.0 collects vast amounts of data, allowing manufacturers to gain insights into operations, customer preferences, and market trends for better decision-making. Cost Reduction: Optimized processes and predictive maintenance can lower operational costs through efficient resource utilization and reduced waste. Supply Chain Optimization: Real-time data sharing enhances collaboration across the supply chain, improving inventory management and reducing bottlenecks. Sustainability: More efficient energy use and reduced waste contribute to more sustainable manufacturing practices, aligning with environmental goals. Workforce Empowerment: Digital tools can enhance worker capabilities and safety by providing real-time information and training resources, fostering a more skilled workforce. Remote Monitoring and Management: IoT technologies facilitate remote oversight of manufacturing processes, enabling quicker responses to issues and greater operational control. Innovation benefits: The integration of advanced technologies encourages continuous innovation, allowing manufacturers to develop new products and services quickly. The pet food manufacturer gained a clear, actionable roadmap for their digital transformation journey toward Industry 4.0. The comprehensive site audit provided valuable insights into their existing infrastructure, allowing them to identify key areas for improvement. With NorthWind's guidance, they now have a strategic plan to enhance efficiency, performance, and future scalability. As they implement these recommendations, they are well-positioned to optimize operations and stay ahead in an increasingly digital and automated industry. Learn more about NorthWind's Solutions the Pet Food Industry or reach out to schedule a walk through of a system. By Aldo Martínez Source: NorthWind Technical Services
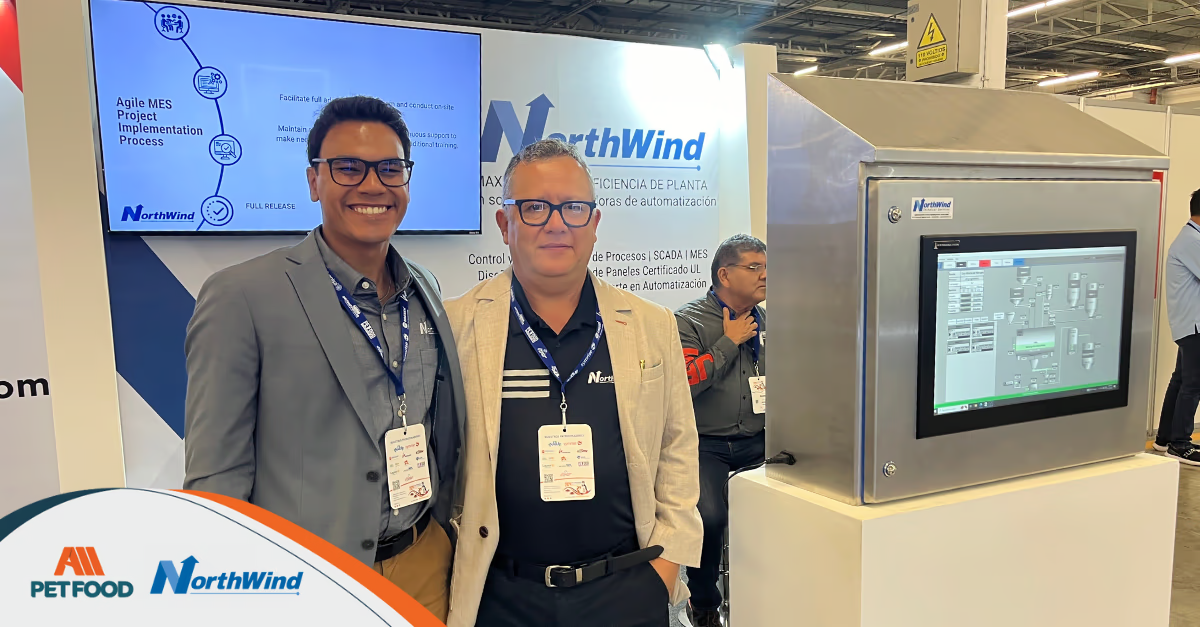
2+ MIN
29/05/2025
NorthWind: Smart Automation and Forward-Looking Vision for the Pet Food Industry
NorthWind Technical Services specializes in delivering comprehensive technological solutions for industrial automation, designed to improve control, efficiency, and quality throughout production processes. Their approach combines digital tools, data analytics, and personalized technical support, tailored to meet the specific needs of each plant. The company also develops intelligent platforms that enable strategic decision-making based on real-time information, helping optimize operations, reduce waste, and anticipate potential failures. Their commitment to innovation is reflected in their ability to integrate advanced technologies such as artificial intelligence into demanding industrial environments. NorthWind has a strong presence in industries such as pet food, food & beverage, milling, and grain handling, where they combine deep technical expertise with an innovative mindset, offering everything from process control to AI-powered tools. Key Presence at Upcoming Industry Events NorthWind will be participating in the following three major events, showcasing their solutions and sharing their vision for the future of industrial automation in the sector: Extru-Tech Extrusion Seminar Aldo Martinez, NorthWind's representative, will give the lecture 'The Future Driven by Automation and Artificial Intelligence,' where he will explore the use of AI in production environments, with a focus on tools like PlantIQ™, the company's system for applying machine learning and analytics inside a plant. EXPO PACK Guadalajara (Booth J-1736) At this event, NorthWind will showcase its automation solutions for pet food, food & beverage, milling, and grain handling industries. Aldo Martinez will also speak on June 10 at 4:00 PM on the Innovation Stage, addressing how digital transformation, powered by artificial intelligence, is reshaping operational models and driving sustainable growth in the digital era. Foro Mascotas Pet Food 2025 (Booth A9) NorthWind will have a dedicated exhibition space for their automation solutions tailored to the pet food sector, featuring demos and real-time technical guidance. With a vision focused on efficiency, traceability, and continuous innovation, NorthWind positions itself as a strategic partner for companies aiming to transform their operations from the ground up. Learn more about their solutions at: https://www.northwindts.com/products/mes-solution/ Source: All Pet Food
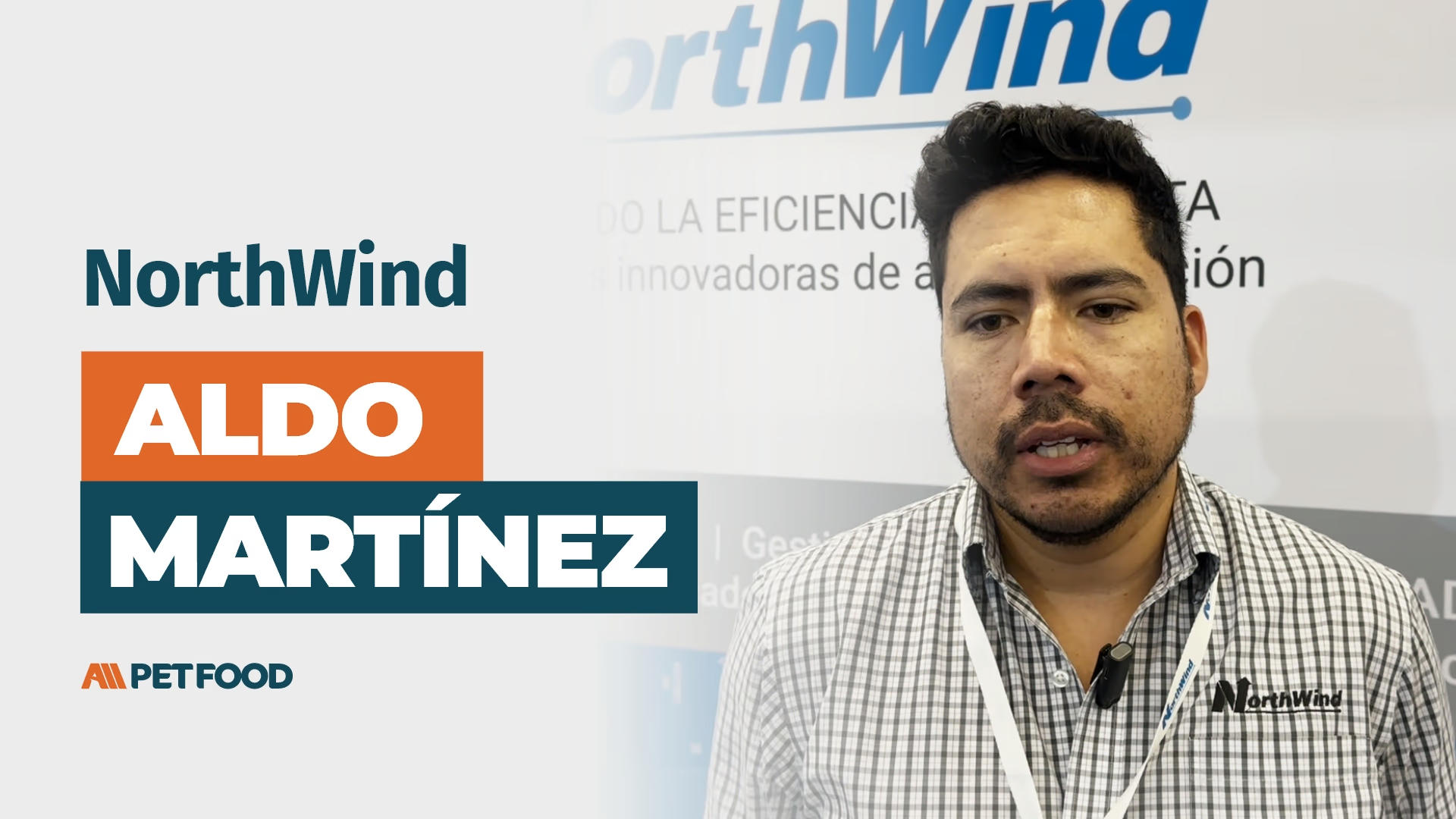
2+ MIN
29/10/2024
Automation in pet food: Interview with Aldo Martínez from NorthWind
Seeking constant efficiency, accuracy, and sustainability is the priority in the pet food sector, and NorthWind is in the middle of this transition. We invite you to know Aldo Martínez's point of view, Business Manager, who shares their solutions and their impact in this interview: - What benefits do manufacturers obtain by adopting automatized and IAbased solutions? 'One of the major benefits clients share is the analysis of general data, virtualization, and digitalization of plants. It is a way to analyze the consumption to evaluate general costs of the end-product and how to maximize consumption, energy, and production only with efficiency and performance management.' - Which areas in the production process are positively impacted by these technologies? 'What we have seen is the general analysis of consumption; we analyze the consumption of raw materials, utilities, and reduction management. We offer data visualization and a list of opportunity areas by managing it by end product, recipes, energy consumption, and sustainability, with different improvement areas in different facility sectors to maximize the general process with automation.' - Considering the future, how do you see these technologies evolving in the coming years? 'Now the trend is focused on energy analysis, sustainability, and the environmental impact accompanied by data and consumption analysis. The development of market trends, quality, and exportation are also contemplated, all of which are carried out together with artificial intelligence, market analysis, and new technological trends.' - From NorthWind, are you working on new solutions? 'Working in the technology industry implies constant innovation. We are embarking on a new goal: bringing artificial intelligence to the technology and production market. Due to the amount of information, we seek to use these mechanisms to see opportunities that perhaps the human eye or the mind cannot manage and process. With AI and production mechanisms, we identify hidden areas that are hard to find and maximize the overall efficiency of the facility.' We support NorthWind in recording its success case in PABSA, a pet food manufacturing company that uses its solutions. Source: All Pet Food
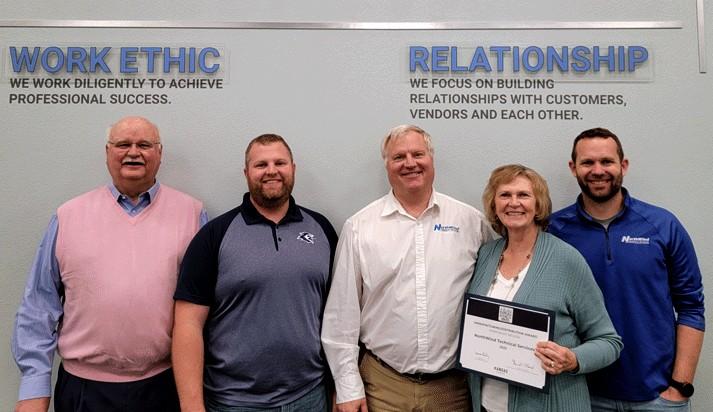
1+ MIN
21/12/2023
Northwind Receives kansas Department of Commerce award
We are delighted to announce that NorthWind Technical Services has been named a Northeast Region Award of Merit winner in the Manufacturing/Distribution category for the 2023 To the Stars: Kansas Business Awards. The recognition was presented by Ernie Beaudet, Northeast Business Development Project Manager. The To the Stars Competition, an annual event hosted by the Kansas Department of Commerce, recognizes businesses for their exceptional contributions to the Kansas economy and local communities. Ernie Beaudet highlighted NorthWind's outstanding achievement, noting, 'In the Manufacturing/Distribution category, NorthWind Technical Services stands out as one of the 37 Merit winners statewide. Out of 4,470 businesses, this places NorthWind in the top 1% of Manufacturing/Distribution enterprises in the State of Kansas.' Mike Bosworth, CEO of NorthWind, expressed appreciation for the recognition, stating, 'Being acknowledged by the Kansas Department of Commerce is a testament to our hard work and commitment. These awards reinforce that we are consistently moving in the right direction, always striving to deliver excellence.' by Northwind Source: All Pet Food
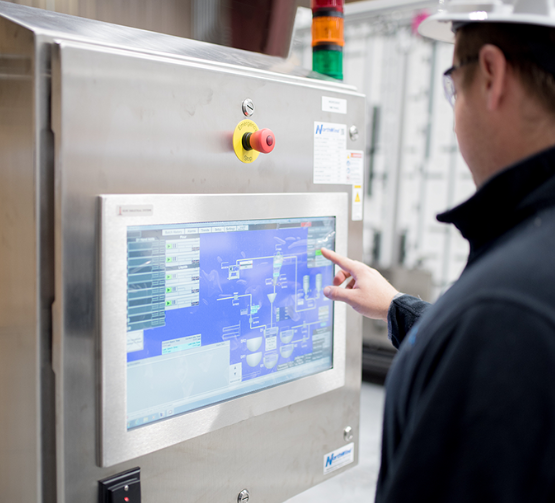
2+ MIN
24/11/2023
Northwind´s expertise in pet food automation
Producing high quality pet food is what your brand is known for. At NorthWind, they help you maintain that reputation through innovative and reliable automation solutions. Their goal with every project is to have your plant running as efficiently as possible. Plant Integration Your plant consists of many different pieces of equipment working together to produce quality pet food & treats. NorthWind specializes in tying all those pieces together to create one seamless control system.This full plant automation solution provides increased plant visibility and allows you to monitor your entire plant no matter where you are. They connect your plant floor to the rest of business by integrating to your ERP System. Formula Management NorthWind's Formula Management software has the flexibility you need with an easy to use interface. BatchLOGIX® formula management software was built to handle the dynamic processes that are common with extruded pet food and treat plants. Reach maximum product consistency with formulas that contain both process & ingredient set points and handles both batching & continuous processes. With BatchLOGIX, your recipes can be as flexible as you need them to be. Customizable set points for both ingredients and process equipment can be configured in the system. Historical data can be accessed through easily customized reports to target specific information using filters. Once created, reports can be exported to Excel, WORD, RTF, or PDF for sharing. Traceability Track ingredients from the time they enter the plant to the time they leave. Trace ingredients through your entire manufacturing process with lot tracking, storage, and reporting capabilities. Lot numbers for liquid and dry ingredients can be traced through multiple systems from source to finished product. Data Management NorthWind makes it easy to collect and use the data that is already available in your plant operation so you can make better, more informed decisions. They collect information about everything from critical control points and run parameters to ingredient usage and system alarms. With this information they provide KPI dashboards and setup equipment maintenance alerts. All information is stored and ready for analysis and comparison to real-time data. Their online web reporter tool makes this easy! About NorthWind NorthWind is an automation company in Kansas providing controls and automation solutions to manufacturing facilities around the world. Their skilled team of engineers, programmers, and technicians have extensive process experience in addition to programming and design expertise in a wide range of industries. You are invited to know more! By: All Pet Food
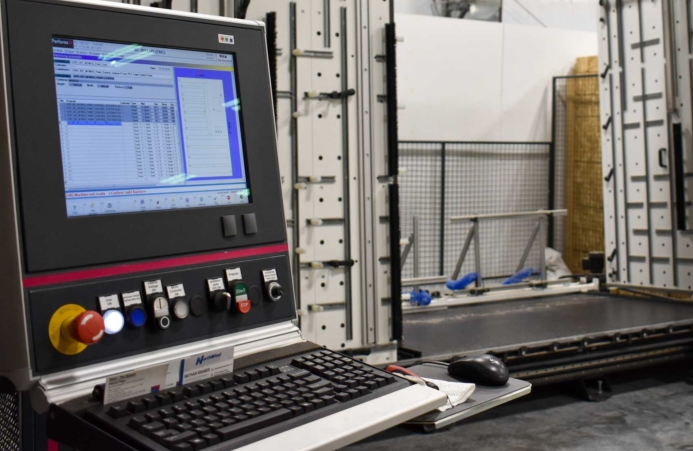
5+ MIN
06/11/2023
Manufacturing execution system capabilities
MES solutions replace traditional paper-based manufacturing procedures and implements a proactive approach to manufacturing execution. Sometimes manufacturers implement reporting functionalities that fall within the scope of MES and sometimes a full-scale MES solution is integrated across the entire plant. Regardless of the size of the solution, the results of implementing MES include decreased costs and increased support for continuous improvement and lean initiatives. MES is used in conjunction with ERP and SCADA systems, bridging the daily plant operations to the rest of the business. Manufacturing Execution Systems can tie into existing batch management systems, such as BatchLOGIX®, and use the existing inventory and production information to give further insight into yield and production metrics. MES connects existing ERP systems, PLCs, and databases. The combined data from those sources can create unique metrics, reports and dashboards that streamline operations, improve productivity, and ensure quality. Using a versatile platform like Ignition Perspective, the capability exists to connect all those data sources, create flexible dashboards, custom reports, custom modules, and Ignition's platform is designed for mobile access. REAL-TIME DATA MES platforms provide real-time production information. This valuable information opens the door for quick production snapshots. Dashboards combine real time operating rates and statuses with features like historical run information and production goals. Doing this provides an efficient way for a user to quickly see production status and identify areas that need attention. HISTORICAL DATA With comprehensive access to plant-wide data, MES offers extensive reporting capabilities. This is another area where the Ignition platform is helpful. Leveraging Ignition's Reporting module, information can be gathered from all the different data sources (ERP, Control System, and SCADA) allowing for the creation of tailored reports that effectively convey data for analysis. Through Ignition's broad array of device drivers, information from data from all parts of the plant can be logged and displayed in a central location. Additionally, the Ad Hoc trending tool proves to be a valuable asset, facilitating easy trend analysis of data points from all sources and saving those trends for later analysis. PERFORMANCE ANALYSIS Centerlining includes adjustable thresholds for each device set the acceptability and alert levels for each indicator. Selected KPIs (key performance indicators) such as Right first time (RFT), Rework, Scrap, Process capability (Cpk), and Overall equipment effectiveness (OEE). With one click, the dashboard can provide a detailed analysis of causes of shutdowns and rejects, batch quality rates, and other production indicators. COMMON MES FEATURES With all this data, both real-time and historical, there are many different modules that can be implemented. The goals and priorities of each plant and workstation guide which modules should be implemented or if a custom module needs to be developed. Below is a list of common modules. Scheduling Provides a global view of the planned production orders. This module can include changeover information, anticipated production time, equipment and materials needed with specific job details to complete the order. Work In Progress (WIP) Inventory Management Track and manage inventory through the different stages of production. MES accomplishes this by helping management fine-tune forecasting by providing real-time inventory audits. With the connection to the ERP system and the control system, validating the inventory levels between the two systems is now automatic. This eliminates the need to manually verify inventory levels on the production floor with what is on the books. The system can also verify materials will arrive in time to complete orders by looking at the delivery data on purchase orders and running it against the upcoming production schedule. Recipe Management A recipe consists of a list of ingredients, ingredient amounts and sequence for combining those ingredients, and the amount to be made (batch size). Create consistency from product to product and run to run as well as make the best use of resources to minimize waste and streamline the manufacturing process. Production Tracking and Dispatch Manage the bidirectional flow of production data in real time between the ERP and the plant floor. Lot Tracking and Tracing From raw material receiving through final product, lot numbers are traced throughout the entire production facility. MES allows for quick recording of batches of raw material, semi-finished products, and finished products, utilizing product genealogy which tracks raw materials, equipment used, dates, quantities, lot, and serial numbers. Quality management and Control Manage the quality of manufacturing processes and units including quality deviations and exceptions. Integrate quality check reminders and recordings for QA. These can be as automatic as implementing density and moisture sensors or more manual with an alarm signaling the operator to complete quality assurance (QA) checks and record them in the system. Each records the information to the MES system for the QA team. Preventive Maintenance Optimize the planning of preventive maintenance operations to reduce the impact on manufacturing. OVERCOMING COMMON CHALLENGES TO IMPLEMENTING MES Implementing a Manufacturing Execution System is a large undertaking and to provide the best solution, collaboration between the integrator and the manufacturer must be frequent. A common challenge is providing the right information and tools to the right audience. When developing dashboards and reports, it is very important to remember who is using the feature and what the goals and priorities are. An operator will want to see different metrics and widgets than someone in a management role. When developing dashboards and reports it is very important to remember who will be using the feature. Separate dashboards for different groups can be created, or widgets can be dynamically hidden/shown depending on the log in permissions and who is viewing the application. Often facilities have used multiple integrators and software systems throughout the plant. This poses a challenge to gathering data in an accurate and efficient way, as there are a variety of sources. NorthWind maintains consistency wherever possible and keeps documentation on where metrics are pulled in from. Documentation is available straight from the MES project. The user can see a description of how a widget works and where the information is being pulled from, whether it is from BatchLOGIX database, a customer's existing ERP system, or a PLC Program. A key to overcoming these challenges is to have open and effective communication with plant personnel to ensure there is clarity on what information is needed. This starts with setting a detailed scope for each area of the system to avoid unnecessary and potentially costly distractions. NorthWind provides a detailed design/development/deployment process and holds meetings with the customer throughout each stage to discuss the project progress and steps to be taken to reach the next stage. Manufacturing execution systems identify inefficiencies and optimize production. This powerful system can be everything from Overall Equipment Efficiency (OEE) for one area of a plant to a fully integrated solution with a paperless plant floor and everything in between. Implementing these features takes deep process and control system knowledge and because every plant has different processes, machinery, KPIs, and process targets the best solution is going to be a tailored fit. At NorthWind we utilize production and process data for plant optimization with a manufacturing execution system developed for you, with you. Learn more about NorthWind's MES Solution. By: Sydney Bosworth Source: NorthWind Technical Services
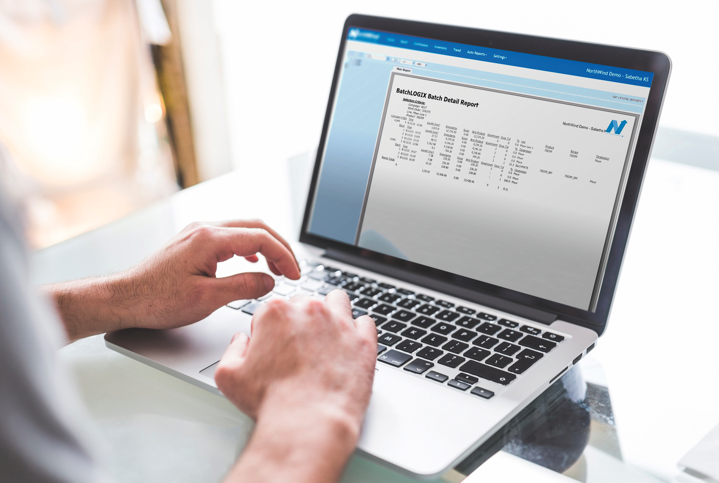
4+ MIN
29/09/2023
Formula management software for pet food production
Automation streamlines the manufacturing process and allows manufacturers to easily monitor and make modifications to the production process from anywhere. Implementing good formula management software gives manufacturers product consistency, lot tracking, and production reports, and it can be easily integrated with ERP (Enterprise Resource Planning) software for a seamless solution. Importance of formula management Implementing the right formula management software is key to maximizing plant performance. This software manages and stores all the formula information for the plant, as well as important process information for lot tracing and production analysis. This includes raw material delivery and storage, final product storage, mapping materials throughout the entire process, and important batch, campaign, and ingredient usage details. It is worth spending time researching formula management software to ensure the package implemented aligns with your business needs. Common Features • Create and store recipes • Recipe modification • Ingredient location mapping • Ingredient parameters • Lot tracking • Production records • Campaign Management Manufacturers often use several software packages to have these features and encompass all processes within the plant. When looking at a system that can fully handle all production needs, features, additional advanced features are needed. Advanced Features • Recipe modifications from the HMI • Ingredient location mapping • Process variables • Micro-ingredients and micro-batching management • Integration with ERP and MES (Manufacturing Execution System) software • Capability of handling both batching and continuous processes Formula management software, such as NorthWind's BatchLOGIX®, provides all the common and advanced features in one robust platform. With features such as material mapping, recipe creation, process variables, micro-ingredient tracking, and production reports, it's able to fulfill production demands. NorthWind offers additional integration that connects the plant floor to the rest of the business. By integrating with the plant's ERP system, data continually transfers back and forth from both systems for seamless and high-level business management. Formulas Formulas for pet food production are complex and need a robust piece of software to handle all variables and both batching and continuous processes within the plant. Often recipes only refer to the amount of each material needed, but there is a lot more that goes into establishing product consistency than simply ingredient amounts or weights. To produce a consistent product, formulas should include both ingredient and process variables and the entire production process from micro-ingredients through continuous extrusion. Ingredient Parameters Ingredient parameters include setpoints, rate tolerances, and upper and lower setpoint trim allowance. Setpoint is the target ingredient rate, tolerance is a percent of error acceptable, and trim allowance is the amount that the setpoint can be adjusted by the operator during production. For example, an ingredient has a setpoint of 100kg/hr, tolerance at 10%, and a trim allowance of 10kg/hr. The operator could adjust the ingredient rate and call for 110kg/hr. The actual rate could potentially be 121kg/hr and still be within the acceptable tolerance. Process Variables Process variables are all the mechanical setpoints on the production floor. For example, a few of the extruder's common process variables include Head Temperatures, Die Temperature, and Die Pressure. These variables are critical for complying with quality standards, making them a vital piece of the formula. Micro-ingredients Batching Hand-batched micro-ingredients are important and often high-dollar ingredients that play a significant role in the final product. This part of the process is often handled separately from the formula management software. Because this step is not included in the formula management and plant automation system, errors often occur during the weighing and lot tracking of these ingredients. BatchMATE® by NorthWind connects the hand batching step to the rest of the plant by automating the hand batching process and including the steps in the formulas. Once connected, BatchLOGIX can track the lots and produce production reports. Lot Tracking Lot Tracking is one of the most critical aspects of any Formula Management Software. The lot tracking process starts from the receipt of raw materials through the final product. By tracking lot numbers in this way, the system can pull specific lot information for each campaign and batch. This is invaluable when a non-compliant lot or a major fault is detected by the quality department. Using the information provided by the lot tracking feature, production data can be analyzed, and contaminated ingredients and products can be identified, isolated, and pulled from the batch or campaign. Production Reports Production Reports are key for any Formula Management Software. The information provided in these reports helps in scheduling production and can be helpful in identifying the cause of missed targets and other inefficiencies. Production reports can also identify when to schedule maintenance and other necessary stops for production. Ingredient usage and run reports are also available to ensure quality and production targets are being hit. Some of the key benefits of good production reporting are business insights, higher customer satisfaction, higher efficiency, and better data-driven decisions. ERP Integration Integrating the plant floor with the rest of the business allows for production data to be seamlessly used throughout the business. It is common for APIs (Application Programming Interfaces) to be written for connecting the plant floor to the ERP system. Having the ability to share data between the different systems is a huge advantage to companies, with this they can schedule production and analyze production in real-time. When all the data is readily available, business decisions are now easily backed by data. Conclusion Whether scaling recipes into a batch or metering ingredients into a continuous system, quality formula management software is key to maximizing plant performance and increasing product consistency. BatchLOGIX® has the scalability to accommodate systems of any size with the flexibility to incorporate all processes within a pet food production facility. By: Eduardo Martinez - Project Manager - NorthWind Technical Services Source: All Pet Food Magazine
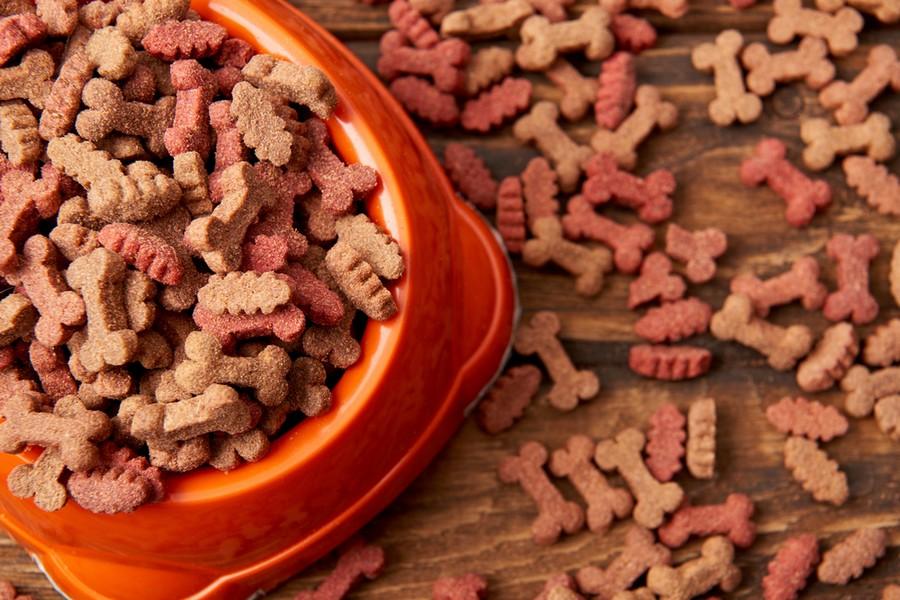
1+ MIN
05/07/2023
NorthWind Extrusion Controls
NorthWind extrusion controls ensure optimization of your system through implementation of specific sequencing during the startup and shutdown of equipment. This in combination with critical alarms and notifications, will help keep your extruders running and minimize wasted product
CRITICAL FACTORS
One of the most critical factors in any extrusion process is the consistent and accurate delivery of materials. Formulas for extrusion are typically set up based on a primary ingredient. All other ingredients in the formula are adjusted based on the level of the primary ingredient. NorthWind's Loss-In-Weight algorithm is designed to maintain consistency in primary ingredient rates even during refill. As the primary rate is increased or decreased, our system automatically adjusts the rates of all ingredients quickly, ensuring that the finished product is always within spec.
RECIPE MANAGEMENT
BatchLOGIX®, a robust recipe management tool was originally designed for batching systems is versatile enough to incorporate continuous formulas as well. BatchLOGIX offers lot tracking and tracing of ingredients which are critical features, especially in food and pet food applications. These features can also be extended into the batching and ingredient delivery systems seen in most extrusion plants.
ALEARN MORE ABOUT BATCHLOGIX
by Northwind
Source: All Pet Food
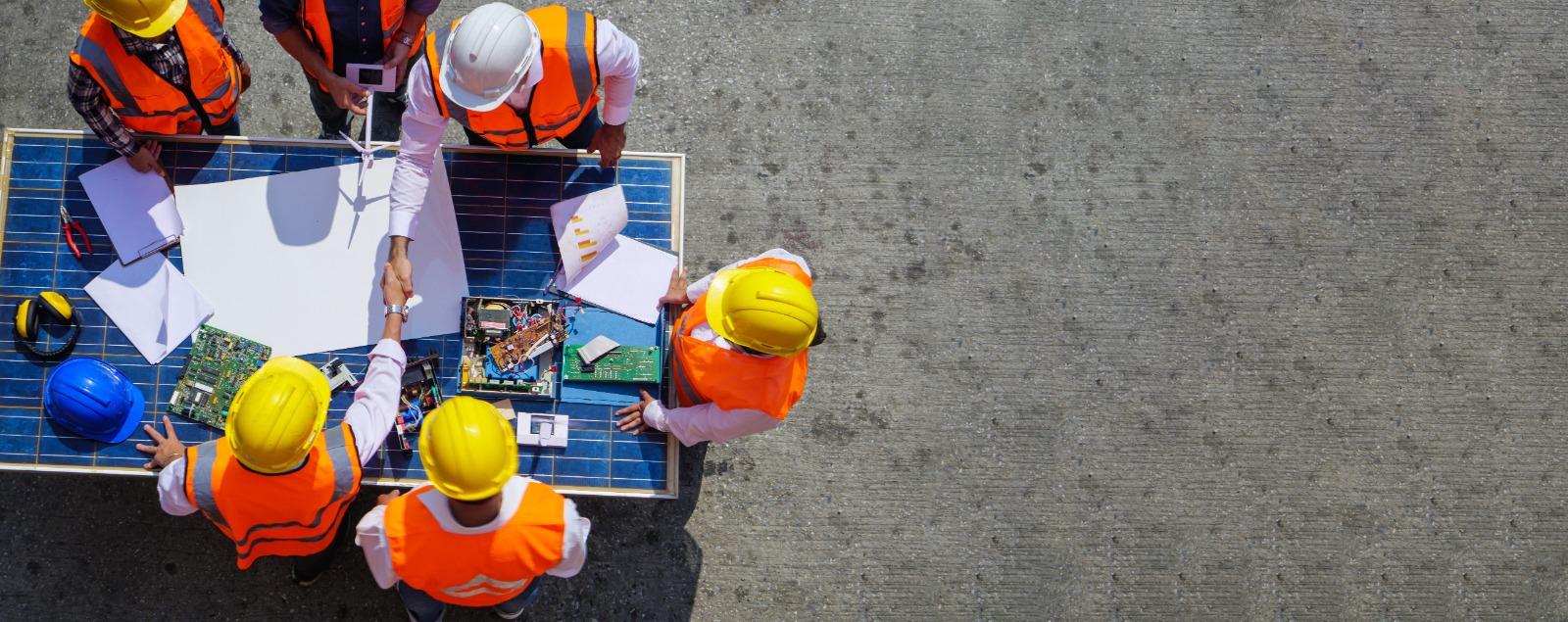
3+ MIN
06/04/2023
Successful control system modernization
The most obvious illustration of this is systems that have obsolete electrical components and legacy software that is no longer actively supported by original manufactures. As we move into Industry 4.0, the old standard of each individual machine having an isolated 'island' of automation is being replaced by more integrated automation systems that communicate to each machine, sharing and creating significantly more data than even 15 years ago. With this added data is the desire to connect the plant floor data to business systems. More and more facilities want production orders to come down from ERP systems to process controls, producing real-time consumption data that is utilized to reduce inventory. To stay competitive, many facilities have made the business decision to modernize their legacy machine and controls systems. Typically, this can be done at a fraction of the cost and time of a greenfield project. Modernizing a control system A control system upgrade can bridge all these gaps by integrating mechanically sound process systems with a modern automation system. At a minimum these projects consist of substantial replacement of obsolete components, sometimes even retaining the original PLC logic. These projects can also be expanded to include high level integration of different machines, adding new machines to an existing system, ERP integration, and ground-up re-writes of logic and operator screens. Modernization projects are known to be complex, especially because engineers are required to work inside an existing framework as opposed to building a system from the ground up. There may be missing documentation or drawings. Additionally, some field modifications may not be included in the drawings. Minimizing production downtime is a significant concern, so the implementation window to get the system back in production is often small. A successful modernization project considers these factors and others during the initial phases of the control system upgrade. Key to any project is developing a deep understanding of the existing system. This is paramount to implementing the upgrade without breaking what is currently in place. Best practices As a Senior Project Manager at NorthWind, I have implemented many modernization projects throughout my career. In this time, I have found a few tried and true practices that lead to a successful control system upgrade. Customer/Project Management Planning When modernizing any system, a collaboration between customer and Project Management is a must. Through this collaborative approach, a forward-looking plan is made to include functionality, risk avoidance, down time reduction, migration solutions, project phasing, etc. to ensure the project scope is clearly outlined and understood. Design Trip There is a misconception that modernization will 'break' the current system and lead to significant downtime. Conducting an initial design trip is instrumental for designing a project that takes into consideration the existing system and its functionality and designing a system that will meet the customers scope and needs. Before any modernization takes place a review of pre-existing equipment, electrical, design and functionality is conducted. Any existing drawings and documentation are also thoroughly reviewed. In the event there are no drawings of the existing system, a new set will be created. Safety Considerations There are misconceptions involving safety considerations: Many people think that safety guidelines are grandfathered in by the date of the original mechanical equipment installation. However, on any substantial electrical modernization project, safety circuits and functionality need to be reevaluated. Electrical Installation One of the biggest concerns with control system modernization is the amount of time it will take for installation and requalification. Working with an industrial electrician with the expertise to understand how to work within schedule constraints and provide creative, custom solutions to meet outage windows is critical. Installation can be done in phases, during production downtimes, or any other number of solutions to keep downtime at a minimum. Benefits of modernization Updating hardware and software with better automation control systems can improve plant performance, increase productivity, improve communication between the process information and business systems, provide useful production data, provide alerts to improve response times, increase plant system security and perform system diagnostics. With NorthWind you can achieve an effective modernization project that manages safety, health and environmental risks, get documentation for field devices in the system, and be assured of a more efficient, consistent and optimized operation, with the support of the system for years to come. Contact us today to talk about your system. By: Blake Bennett – Automatización Source: Northwind Technical Services
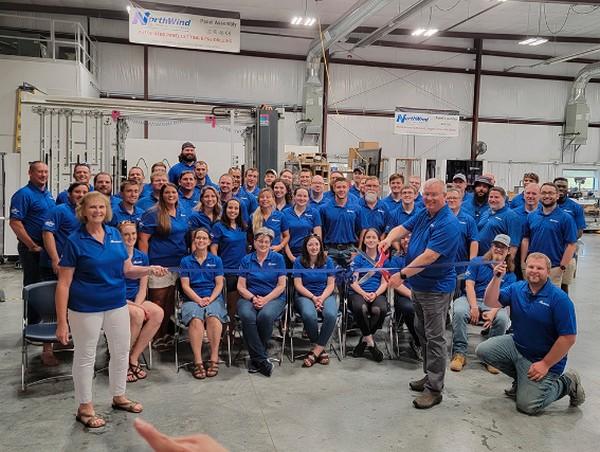
2+ MIN
27/07/2022
Northwind Celebrates 25 Years !
The celebration kicked off at 5pm with NorthWind employees, their families and guests enjoying outdoor games and activities for all ages. Before dinner Mike and Marlene said a few words and the Sabetha Chamber of Commerce had a ceremonial ribbon cutting to commemorate the 25 year milestone. The evening celebration was full of fun, friends, and family! COMPANY HISTORY 1997 NorthWind Technical Services, LLC was established by Mike and Marlene Bosworth in their home outside of Sabetha, Kansas. At that time, the company primarily offered engineering consulting services. 1999 NorthWind began offering automation system solutions and moved into a small office space in downtown Sabetha. Control panels for automation systems were constructed in the Bosworth's garage at their home. 2001 The company's first full time employee was hired. 2003 A new 5,000 sq. ft. office and panel shop were constructed in the Sabetha industrial Park for the growing business. 2010 NorthWind becomes CSIA certified. 2012 A major expansion added 2,600 sq. ft. of space that included a test lab, lunchroom, and additional office space for a growing number of employees. 2014 NorthWind expanded for a second time, adding another 3,250 sq. ft. to the facility's panel shop and warehouse area. 2017 A third expansion of approximately 10,000 sq. Ft. provides additional space for control panel fabrication and personnel. 2019 NorthWind opens the Latin America Office located in San Jose Costa Rica. NorthWind is also recognized as System Integrator of the Year by Control Engineering Magazine. 2021 NorthWind opens an office in Kansas City. NORTHWIND TODAY Our headquarters is located in Sabetha, KS. The majority of employees and all panel fabrication activities are located at this facility. A second location was established in San Jose, Costa Rica in June of 2019 to better serve customers in Latin America. The Costa Rica office houses twelve employees that work in Service, Sales, and R&D. A third office in Kansas City opened in 2021 housing a small group of employees who live in the KC area. NorthWind strives to achieve high standards that meet customer needs, promote employee wellbeing and development and to ensure company stability. The company has been Control Systems Integrators Association (CSIA) certified since 2010 and consistently employs CSIA Best Practices and Benchmarks to provide the best value to its customers, combining technical proficiency with sound business practices. NorthWind is also an accomplished Rockwell Automation Gold Partner, providing proven services and solutions that meet our customers' automation needs. by All Pet food
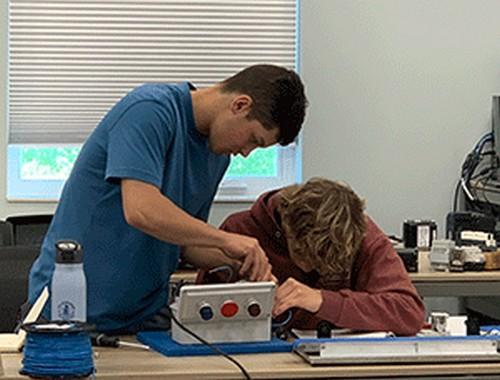
1+ MIN
14/07/2022
2022 Intro to Automation Course
May 31 – June 3. Professor Clark Shaver from the Electronics Engineering Technology Department at Pittsburg State University presented the course to twelve students. While one-half of the students were from Sabetha, students from surrounding communities including Fairview, Seneca, Wetmore, Horton, Centralia and Humbolt, NE made up the other half. The students learned basic programmable logic controller (PLC) programming and controls wiring to complete approximately 25 projects that included buzzers, strobe lights, and conveyor systems. Automation industry experts from NorthWind and other companies shared information on career paths in the rapidly expanding field of automation throughout the world as well as in our local area. Students were presented with a Certificate of Completion and have the opportunity for scholarships and course credit if they pursue an engineering degree with an automation minor at Pittsburg State University. The owners of NorthWind, Mike and Marlene Bosworth commented, 'We enjoyed hosting the course and giving these young individuals a small taste of the automation industry. We are hopeful that we can host this course again next year.' by All Pet Food
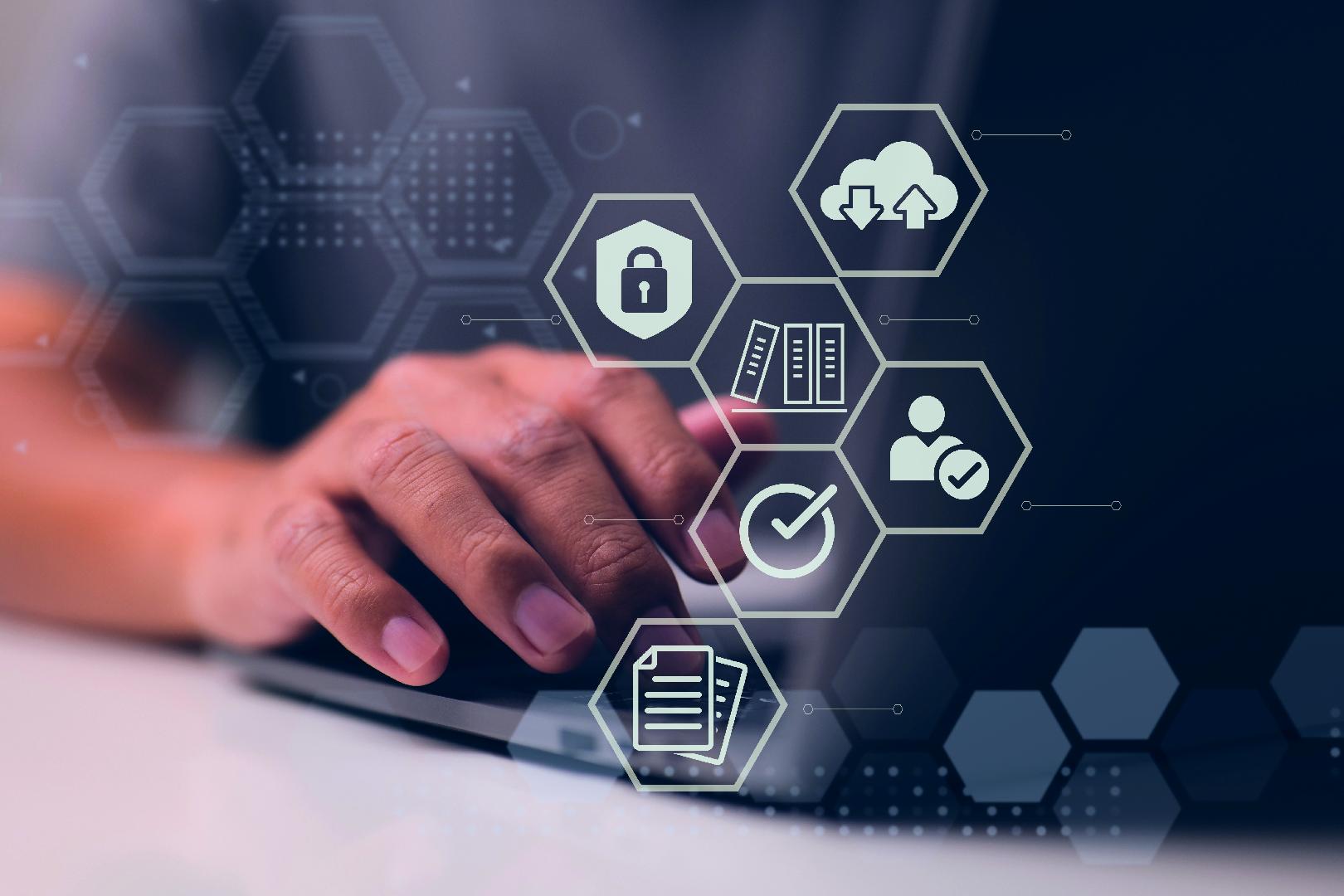
4+ MIN
02/06/2022
Remote access for industrial control systems
This tool is particularly helpful in servicing control systems through a network connection. By connecting to the system's programmable logic controllers (PLC), Human Machine Interface (HMI), and other Ethernet compatible devices, integrators can efficiently monitor, troubleshoot, and fix an issue without physically traveling to the site. Employers can control many quality services via remote access, such as: troubleshooting, remote startup, remote monitoring, software upgrades or additions, proportional-integral-derivative (PID) tuning (adjust the PID controller), User Interface (UI) additions, and other improvements to the customer's automated system. Service technicians have access to tools and software solutions that many manufacturing plants may not have, and these can be utilized remotely to enhance the service experience. This article discusses best practices for establishing remote access, services provided using a remote connection, and help determine if remote access is correct for your plant. Best practices for establishing Remote Access When establishing remote access to a plant's control system for the first time, there are several guidelines to follow from both the integrator and the plant's side. The first step to connecting remotely is to obtain permission from the plant's IT department to access the virtual private network (VPN). The integrator provides the plant's IT department with a list of authorized technicians who will provide service and support for the plant. The plant's IT department will set up user accounts for those authorized technicians. If applicable, non-disclosure agreements will be signed. Safeguards for a secure connection Integrators use a VPN for connecting to the plant's control system Plant IT has an isolated network for the VPN Routine system backups Utilize virtual machines (VM) Remote Access – Technical Service and Support A major benefit for establishing remote access to a plant's control system is the ability to quickly be connected for service and support. In the event there is a problem with the control system, such as a production sequence is out of order, a burner is not reaching a high enough temperature, or a conveyor is not moving fast enough, plant maintenance personnel can contact an integrator for technical support. A service technician is speaking directly with the plant personnel. By working together, problems are solved faster, immediate feedback is provided, questions or concerns are addressed, and this is an opportune time to provide plant personnel some system training. With remote access available, service technicians are able to support plants quickly and efficiently. With prior remote access established, a technician can be connected to a plant within 15 minutes of calling about an issue. This quick connection time allows for troubleshooting to begin immediately, while reducing plant down-time. Remote access allows the service technician to monitor the system live to catch any intermittent problems. Control Systems can be remotely accessed and watched for a specific problem or issue over a number of hours or days. Then when the problem occurs, the service technician can isolate what caused the problem, what conditions were present when the issue occurred and provide a solution. Another benefit to remote access is being flexible within the time frame of system maintenance. Service can be provided around rigid time and production schedules, as remote access can occur at any time during the day. This eliminates waiting until regular business hours to contact support and then having to make travel arrangement to get a technician on site. Remote access can also serve as an extension of the customer's maintenance and continual improvement departments. Remote Access – Control System Startup Some Control System modification and addition projects can be started up remotely. The benefits to a remote startup are similar to remote access service. Time (travel and onsite) Money (costs of travel, rental, accommodations, etc.) Resources Help can be offered immediately, the customer only has to pay for labor time to fix an issue, fixes can be provided around rigid production schedules, and additional resources can be utilized. Remote Access can also be used in conjunction with onsite startups to provide additional training and which helps build on more complex ideas and unique operating situations. And lastly, with the restrictions of travel and health concerns surrounding Covid 19, quarantine restrictions and safety protocols can be eliminated if remote access is used. Remote Access can provide a quick, affordable solution for control system maintenance. Remote Access saves travel time, accommodation costs, and costs associated with down-time. Remote access provides the customer with immediate help and resources any time day or night and remote access can also be used to monitor intermittent problems. Remote Access can be utilized not only for start-ups, service, and maintenance, but operational training as well. NorthWind's Service Team provides remote service and support for all control system issues. Form more information about NorthWind click HERE. Author: Jake Taylor - Service Manager Source: NorthWind's Technical Services
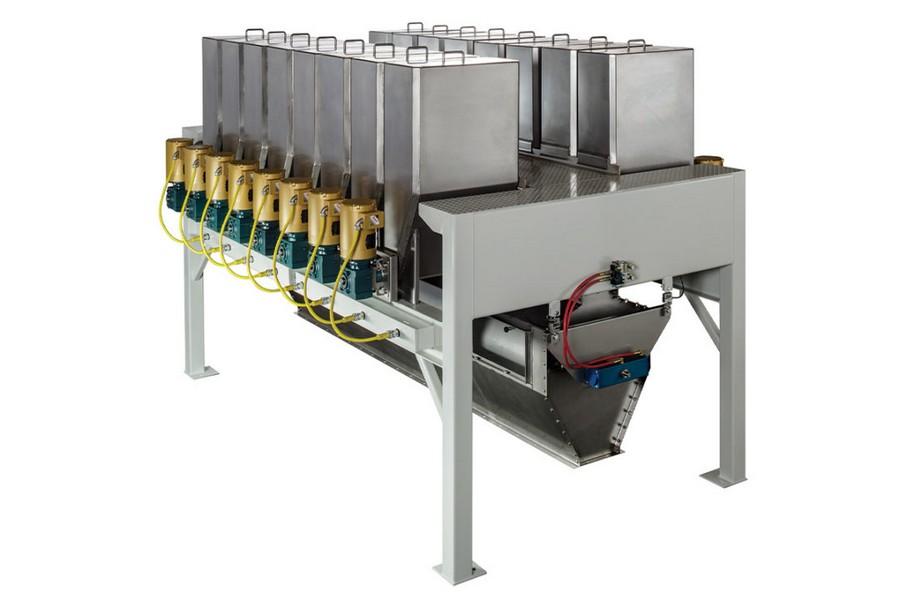
8+ MIN
02/03/2022
Benefits of modern batching systems
Batching systems play an important role in product quality and plant efficiency for pet food and treat processors. Equipment design can ensure product uniformity, consistent product flow, and efficient changeovers from batch to batch. There are a number of common options for batching systems in pet food and treat applications, and processors must consider several factors when looking to upgrade their facilities. Evaluating batching systems 'When considering an automated batching system for pet food ingredients, it is important to look at several factors which will influence the type of batching system recommended and optimize ingredient cost savings and overall ROI,' said Sharon Nowak, business development manager, Coperion K-Tron USA Food & Pharmaceutical Industries, Sewell, N.J. 'The top three for consideration include batch accuracy required for the specific ingredient, desired batch times, and overall plant design considerations including height limitations, space requirements, and support structures for the batching system.' 'It's a little different for everyone,' added Matt Lueger, vice president of sales, NorthWind Technical Services, Sabetha, Kan. 'But the big factors that we typically see are accuracy, traceability and flexibility. Most customers not only want a system that consistently produces a quality product, but also tells them what went into each batch without restricting their ability to continually change their ingredients or recipes.' Pete Ensch, chief executive officer, WEM Automation, LLC, New Berlin, Wis., agreed on the importance of traceability for today's processors. 'The batch system needs to incorporate lot code traceability,' he said. 'Pet food producers' value is directly linked to their track record of producing safe quality food. In the event that something goes wrong, you need the ability to quickly track the problem and contain it. Traceability needs to be automated and working in the background. Beyond the safety side, traceability also helps to control inventory management and control, and can be linked back to your ERP to help automate purchasing. This keeps production flowing and controls cost.' Other factors to take into consideration include throughput, types and quantities of product that need to be conveyed, and quality and repeatability. 'At the end of the day, you need a batching system that can accurately weigh out your ingredients and consistently mix them,' Ensch explained. 'Pet food has some unique challenges in that there are many different ingredients with a variety of densities and flow rates. Several of the raw ingredients, because of the nature of protein, have a significant amount of variability. Equipment and controls need to be able to handle the de variety. All of the downstream processes like extrusion and drying perform better if you provide them a consistent, quality input.' Batching options Modern batching systems are designed with factors such as accuracy, reliability, traceability, flexibility and food safety in mind. 'Due to the increased food safety regulations and requirements to adhering to exact ingredient percentages in a given pet food recipe, the use of high accuracy LIW [loss-in-weight] batching using gravimetric screw feeders is quickly becoming the most reliable batching device of choice,' Nowak said. 'LIW batching utilizing Coperion K-Tron high-accuracy screw feeders provides a significant accuracy and process time advantage over traditional GIW [gain-in-weight] batch techniques. LIW batching is used when the accuracy of individual ingredient weights in the completed batch is critical or when the batch cycle times need to be very short. In addition, LIW feeding affords broad material handling capability and thus excels in feeding a wide range of materials from low to high rates.' Regardless of feed rates, LIW batching can offer accuracy, speed and variability benefits over traditional GIW methods. (Source: Coperion) 'There are several different types of batching systems,' added Joe Lewis, marketing, Sterling Systems & Controls, Inc., Sterling, Ill. 'These include semi-automatic hand prompt/add batching systems, semi-automatic self-contained 'kitchen type' batching systems, and automatic batching systems.' Utilizing different systems and features allows pet food and treat processors to fine-tune the batch process from start to finish. Options include manual or automatic batch delivery, various ingredient storage methods, and integration to the ERP system to communicate production schedules and ingredient usages. 'Most modern batch controls have dozens of features, but a couple of useful ones for pet food are an order grid and automatic bin level checking,' Ensch said. 'An order grid includes order number, formula name, the amount of material to be produced, the required date, destination bins and comments. The grid can have orders entered direct or interfaces with your ERP system. Automatic bin level checking has the system check bin levels of each ingredient in a production run prior to starting the batch. The system will alert the operator of any insufficient ingredients. 'Another useful feature is production usage tracking and inventory management with lot code tracking,' Ensch added. 'This allows the batch system to track material used for each production run, batch, and track respective lot codes for ingredients. Statistical process control (SPC) charting is one more feature that's great for fine-tuning the batch process. A system tracks the production data to the level to produce statistical process control charts. Being able to understand when a system is in control or out of control and having the data to either troubleshoot it or reduce variation for greater accuracy can change your business.' Product quality There are several ways in which batching systems can impact product quality. 'Vacuum conveying systems help to provide the right amount of ingredients or final products to the next processing or packaging step,' said Andrea Bodenhagen, communication and content manager, Piab Vakuum GmbH, Butzbach, Germany. 'Thanks to the closed system, it also provides a dust free environment and protects the product from contamination. While the pet food industry is often still using mechanical or manual material handling, vacuum conveying systems are state of the art in the pharma and food sector. Pet food manufacturers, therefore, benefit from the long-term experience of Piab in these sectors as well as all the developments that have been done for these industries to keep the original product quality during the conveying process.' 'Batching systems play a significant role in the overall product quality of pet food and treats,' Lueger said. 'Not only in the accuracy and consistency of the ingredients that make up the product, but also in the visibility of what went into the product in the event of a quality issue. Batch reports and historical trends can go a long way toward preventing future product quality issues.' Jim Gaydusek, sales director, United States and Canada, Cozzini LLC, Chicago, agreed that batching systems have an important role to play in consistency and product quality. 'One of the greatest benefits is consistency from batch to batch,' he said. 'Auto management of recipes removes much of the human factor and reduces processing error. Scales accurately weigh the ingredients to ensure the proper weight(s) get added and the HMI [human-machine-interface] can sequence through the processing steps according to the program.' Plant efficiency Batching systems can also impact plant efficiency for pet food and treat processors. 'In addition to improving product quality over traditional manual weighing methods, the automation of the material handling/product transfer as well as the batching can greatly affect overall efficiency,' Nowak said. 'The use of automated dispensing systems, which can also integrate pneumatic conveying systems for material transfer, can greatly reduce the amount of human interaction as compared to manual methods of weighing and transfer. This maximizes social distancing and adheres to strict COVID guidelines of safety. 'Properly weighing and accurately delivering the ingredients without manual intervention can result in a number of process advantages, including overall food safety, fewer mistakes, better accuracy, lower bulk costs, improved product quality and savings in manufacturing costs,' he added. 'Eliminating manual batching reduces scrap costs, increases efficiency and throughput,' Lewis noted. 'Automatic systems can be customized with multiple scales for speed of batch production without sacrificing accuracy or quality, resulting in fast high batch rates and accuracy of weighments. Dust containment and collection options for automatic batching systems improves safety and operator efficiency.' Processors must be able to track and trace each ingredient throughout the process to ensure quality and safety and, in the case of a product issue, pinpoint exactly where and what went wrong. (Source: Coperion) To maximize overall efficiency, factors such as system design and sequencing must be taken into account. 'You want a system that moves from one batch to the next seamlessly and with little idle time between batches,' Ensch said. 'Some of this is system design, things like having holding vessels, surge bins and multiple scales so that you can weigh up ingredients before the mixer; optimizing cleanout times between batches and changeovers; the use of high and low bin level indicators and automated routing to make sure the batching system is never starved for ingredients. The system must manage all the timing, so the batching process is nearly continuous in nature.' New advancements Batching systems continue to evolve to meet changing needs and requirements. Modern batching systems now have huge advantages over their predecessors in a multitude of areas. 'Over the past decade the number of different types of formulations and the raw ingredients used has grown exponentially,' Ensch said. 'This has made batching systems larger and more complex. Having a blending control system that has formula-based scaling and mixing parameters is extremely helpful. The trend of higher protein pet food has also increased the content of fibrous protein ingredients, which have the much greater variation. Formulations contain many ingredients and there is a need for a batch system that can measure major, minor and micro ingredients with very low dispersions like vitamins and minerals.' 'There have been a significant number of design improvements to batching systems for pet food and treat processing,' Nowak said. 'They include improvement in weighing technologies and batching controls, improvements in overall design of equipment to improve cleanability and food safety while minimizing downtimes, improvements in feeder design options ideal for difficult flowing materials, and improvements in feeder technology to alleviate pressure/vacuum influences on the feeder output.' Advancements in technology have also vastly improved traceability of ingredients. 'The amount of technology that is utilized to track and trace ingredients continues to evolve,' Lueger noted. 'From simple bar-coded lot numbers on bags to RFID [radio-frequency identification] tracked totes/IBCs [intermediate bulk containers] and hoppers on tracks or AGVs [automated guided vehicle]. Innovation and technology gains continue to support traceability regardless of size, equipment configuration, system capacity, etc.' By Richard Rowlands & Matt Lueger Northwind Technical Services - Pet Food processing

3+ MIN
22/10/2021
Identifying critical system data with High-performance graphics
The control system's human machine interface (HMI) is the connection between an operator and each machine. HMIs provide processing data for operator and maintenance personnel to interact with the equipment. Traditional HMI graphics that are full of color, moving components, and detail are visually impressive but inefficient as the colors and animations detract from the actual data needed. Plant operators and maintenance personnel must quickly identify critical process information and high-performance graphics (HP graphics) allow them to do just that. By understanding HP graphics and how they help operators identify critical information, companies can confidently make the shift to new technology. High-Performance graphics vs traditional HMI graphics: Visual Differences HP graphics reduce troubleshooting time by highlighting pertinent information. While maintaining a visual representation of the equipment and system, HMIs provide a user with helpful alerts and status information. In traditional graphics, the proliferation of color is distracting. HP graphics reserve bold colors and movement only for instances when attention is needed. For example, if a receiver refill is disabled and the receiver is below low level, the low-level indication is visible, but the banner will be gray instead of yellow. This color change allows the operator to better focus on critical information. How to transition an HMI to HP Graphics It's possible that some personnel will not be initially accepting of the new graphics. The biggest push back when upgrading to HP graphics generally comes from operators that have been working with traditional HMIs for a long time and are used to a lot of color and detail on the screen. The grayscale color scheme brings a misconception that the new HP graphics will make it harder to understand what is happening in the system. However, with more muted tones, alerts and warnings are very easy to spot, providing the user a very readable HMI. HMI alerts and alarms that benefit from HP graphics include: System Status Device Faults Low Feed Rate Ingredient Setpoints Trends Process Variables Batch Details Implementing HP graphics on the plant floor NorthWind has moved to HP graphics as a standard for all projects. With this change, we have maintained the same overall feel, while providing a more readable HMI. Our HOA banners, menu bar, and feed point objects maintain similar aspects to our old graphics package but are now more visible when data is most critical. A lot of the changes incorporate the intentional use of color and adding dynamic visibility – displaying exactly what information the user needs to see at the critical moment. To further ease troubleshooting, reference points are built into the HMI, PLC, and electrical drawings, allowing personnel to quickly find the information they need. NorthWind trains and supports customers through the transition to HP graphics – from the startup process to complete integration. We also transition existing HMIs to HP graphics for a streamlined user experience across the entire manufacturing plant. At NorthWind, we're all about data. The efficiencies gained with the new graphics are everything we're about – accurate process data in the most usable form. Source: Northwind Technical Services LLC